- FMA
- The Fabricator
- FABTECH
- Canadian Metalworking
Categories
- Additive Manufacturing
- Aluminum Welding
- Arc Welding
- Assembly and Joining
- Automation and Robotics
- Bending and Forming
- Consumables
- Cutting and Weld Prep
- Electric Vehicles
- En Español
- Finishing
- Hydroforming
- Laser Cutting
- Laser Welding
- Machining
- Manufacturing Software
- Materials Handling
- Metals/Materials
- Oxyfuel Cutting
- Plasma Cutting
- Power Tools
- Punching and Other Holemaking
- Roll Forming
- Safety
- Sawing
- Shearing
- Shop Management
- Testing and Measuring
- Tube and Pipe Fabrication
- Tube and Pipe Production
- Waterjet Cutting
Industry Directory
Webcasts
Podcasts
FAB 40
Advertise
Subscribe
Account Login
Search
Thank you, welders
- By Vicki Bell
- September 12, 2012
As noted in a Wikipedia article about the building, along with the protection offered by the 185-foot (56 m) windowless concrete base—intended to protect it against truck bombs and other ground-level terror threats—a number of other safety features were included in its design to better prepare it for a major accident or terrorist attack: 3-foot (91 cm) thick reinforced concrete walls for all stairwells, elevator shafts, risers, and sprinkler systems; extra-wide, pressurized stairwells; a dedicated set of stairwells exclusively for the use of firefighters; and biological and chemical filters throughout its ventilation system.
The building is no longer 25 feet (8 m) away from West Street, as the Twin Towers were; at its closest point, West Street is 65 feet (20 m) away. The windows on the side of the building facing in this direction are equipped with specially tempered blast-resistant plastic, which looks nearly the same as the glass used in the other sides of the building. The 70 elevators and nine escalators for 1 World Trade Center will be provided by ThyssenKrupp, with steel counterweights supplied by Concord Steel.
The Port Authority has stated: "Its structure is designed around a strong, redundant steel moment frame consisting of beams and columns connected by a combination of welding and bolting. Paired with a concrete-core shear wall, the moment frame lends substantial rigidity and redundancy to the overall building structure while providing column-free interior spans for maximum flexibility."
How many of us have considered the welds as we’ve driven across bridges, boarded a ship or an airplane, taken a ride in our cars, peered out of a window on the top floor of a high-rise building, or turned on the gas heat in our homes? I imagine a show of hands would result in few if any. However, the welding that goes into each of these entities, from bridges to gas pipelines, is critical.
In 2011, a former shipyard welding inspector was sentenced to 37 months in prison for lying about the certification of weld inspections on Navy vessels. The inspector plead guilty to a charge that in 2007 he knowingly signed and put his employee ID number on the record of a pipe joint weld he knew he had not inspected. This pipe weld on the Missouri submarine had a half-inch crack on the bottom that could have sunk the sub.
In sentencing the inspector, the judge said, “ … you put the lives of potentially thousands of people, it seems to me, at risk. It almost leaves me speechless.”
Just last month, CBS News reported that Pacific Gas & Electric settlement documents showed more than $2 million went to a teenager burned in the San Bruno gas pipeline explosion. The 2010 blast that killed eight people and destroyed dozens of homes was blamed on an inferior pipeline weld.
Keep in mind that only inferior welds that cause harm make the news. For every bad weld, there are countless sound welds that enable us to go about our lives safely—to cross that bridge, fly to a city, and enjoy the view from a skyscraper.
Thank you, welders.
Follow fabcomlady on Twitter.
Become a fan of The Fabricator® on Facebook.
subscribe now
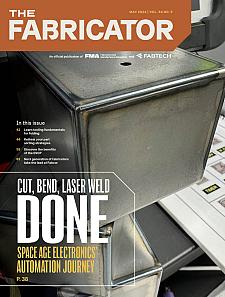
The Fabricator is North America's leading magazine for the metal forming and fabricating industry. The magazine delivers the news, technical articles, and case histories that enable fabricators to do their jobs more efficiently. The Fabricator has served the industry since 1970.
start your free subscriptionAbout the Author
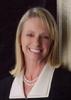
Vicki Bell
2135 Point Blvd
Elgin, IL 60123
815-227-8209
- Stay connected from anywhere
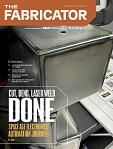
Easily access valuable industry resources now with full access to the digital edition of The Fabricator.
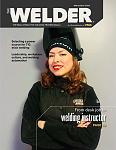
Easily access valuable industry resources now with full access to the digital edition of The Welder.
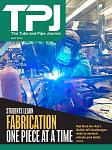
Easily access valuable industry resources now with full access to the digital edition of The Tube and Pipe Journal.
- Podcasting
- Podcast:
- The Fabricator Podcast
- Published:
- 04/16/2024
- Running Time:
- 63:29
In this episode of The Fabricator Podcast, Caleb Chamberlain, co-founder and CEO of OSH Cut, discusses his company’s...
- Trending Articles
Tips for creating sheet metal tubes with perforations
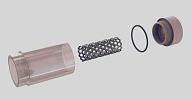
JM Steel triples capacity for solar energy projects at Pennsylvania facility
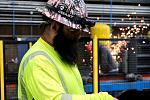
Are two heads better than one in fiber laser cutting?
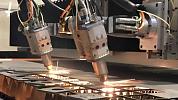
Supporting the metal fabricating industry through FMA
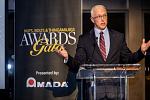
Omco Solar opens second Alabama manufacturing facility
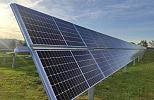
- Industry Events
16th Annual Safety Conference
- April 30 - May 1, 2024
- Elgin,
Pipe and Tube Conference
- May 21 - 22, 2024
- Omaha, NE
World-Class Roll Forming Workshop
- June 5 - 6, 2024
- Louisville, KY
Advanced Laser Application Workshop
- June 25 - 27, 2024
- Novi, MI