Editor-in-Chief
- FMA
- The Fabricator
- FABTECH
- Canadian Metalworking
Categories
- Additive Manufacturing
- Aluminum Welding
- Arc Welding
- Assembly and Joining
- Automation and Robotics
- Bending and Forming
- Consumables
- Cutting and Weld Prep
- Electric Vehicles
- En Español
- Finishing
- Hydroforming
- Laser Cutting
- Laser Welding
- Machining
- Manufacturing Software
- Materials Handling
- Metals/Materials
- Oxyfuel Cutting
- Plasma Cutting
- Power Tools
- Punching and Other Holemaking
- Roll Forming
- Safety
- Sawing
- Shearing
- Shop Management
- Testing and Measuring
- Tube and Pipe Fabrication
- Tube and Pipe Production
- Waterjet Cutting
Industry Directory
Webcasts
Podcasts
FAB 40
Advertise
Subscribe
Account Login
Search
A glimpse into the future
The FMA Annual Meeting provided metal fabricators a good idea of what’s heading their way
- By Dan Davis
- March 14, 2024
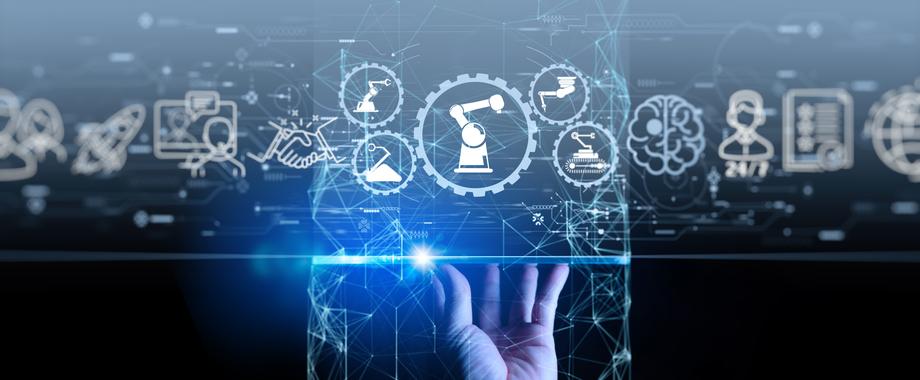
Plenty of growth opportunities await the North American metal fabricating base. Do metal fabricators have the personnel and equipment in place to take advantage of what lies ahead? greenbutterfly/iStock/Getty Images Plus
If you missed the FMA Annual Meeting in Clearwater Beach, Fla., at the end of February, you missed out on a good chance to see what the near future might hold for the North American manufacturing community. Let me try and summarize how all of this is connected.
On the first day, keynote speaker Gene Marks, a columnist for Forbes and other outlets, provided an overview of where industry is with artificial intelligence (AI) and what can be expected in the future. Today, AI technologies are being used for customer-facing applications, such as a chatbot on a consumer website, but tomorrow promises a whole lot more. In the front office, you are looking at AI taking on more administrative tasks, generating marketing communications, and investigating human resources issues, with the information being delivered in a format that can be reviewed and fine-tuned by a human. In the shop, AI makes machines smarter, which helps staff to stay on top of maintenance of metal fabricating equipment and makes things like autonomous material handling robots more user-friendly.
Marks mentioned that experts suggest the AI-related economy is expected to grow from $428 billion this year to $2 trillion in 2030. That’s incredible growth in a short amount of time.
It’s also energy-intensive growth. Right now, some speculate if the current energy grid in the U.S. can keep up with current energy requirements for continued digital demands. Check out the profile of Hennig Power Protection in the February 2024 issue of The Fabricator, and you’ll learn that the demand for diesel generators to act as back-up power sources for data farms is seemingly unrelenting. AI only intensifies energy requirements because much more computational power is required to support these digital advancements.
In fact, Tim Hill, commercial general manager of sustainability solutions, Nucor Corp., told the same crowd that the U.S. is in a “dire” situation when it comes to keeping up with energy needs. He went so far as to suggest that some parts of the country might experience temporary power outages this summer because of the strain put on the grid.
From a steelmaking perspective, the U.S. is well on its way to becoming the home of more environmentally responsible steelmakers. Hill estimated that about 70% of steel in this country is now made in electric arc furnaces, which have a much smaller carbon footprint than more traditional mills with blast furnaces. But these plants require a consistent supply of electricity to stay in operation.
In the April 2024 issue of The Fabricator in the Steel News column, Michael Cowden of Steel Market Update delved into this issue a little deeper. He made the same point as Hill: Nuclear energy looks to be the answer to fill the gap where renewable energy sources, such as wind and solar, can’t. The key is getting Washington, D.C., to step up and modernize regulations to reflect the advent of new nuclear plant designs.
Energy grid upgrades and potential nuclear facilities need metal fabrications to become a reality. On top of that, Jason Ray, co-founder and CEO, Paperless Parts, stressed during a breakout session at the FMA Annual Meeting that billions in manufacturing is going to return to North American shores by 2030. He added that 50% of the shops that use its automated quoting software expect a surge in time spent quoting in the coming months.
Ray mentioned that the average size of a job shop, which includes both machining and metal fabricating companies from his company’s perspective, is about $4 million. He suggested that over the next five years, such a shop could grow its business five times over just with the amount of work that will be available.
Now, you might quibble about how much larger the metal fabrication pie might grow in North America over the coming years, but you really can’t deny that it’s growing—and likely will continue to do so. Private equity companies are looking to invest in this sector for a reason.
Those shops that have established a knowledgeable and responsive team and invested in modern metal fabricating technology in recent years are poised to take on the challenges of what awaits. On the other hand, those now embarking on a modernization journey have to tend with an even tighter job market and rising interest rates.
Change is inevitable, but it provides opportunities for metal fabricators to thrive. Just don’t wait around for it to happen. Make plans and act. You know what’s coming.
subscribe now
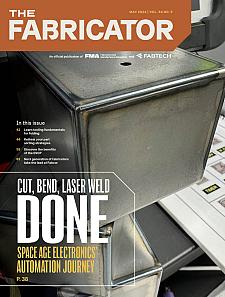
The Fabricator is North America's leading magazine for the metal forming and fabricating industry. The magazine delivers the news, technical articles, and case histories that enable fabricators to do their jobs more efficiently. The Fabricator has served the industry since 1970.
start your free subscriptionAbout the Author
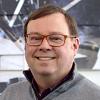
Dan Davis
2135 Point Blvd.
Elgin, IL 60123
815-227-8281
Dan Davis is editor-in-chief of The Fabricator, the industry's most widely circulated metal fabricating magazine, and its sister publications, The Tube & Pipe Journal and The Welder. He has been with the publications since April 2002.
- Stay connected from anywhere
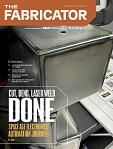
Easily access valuable industry resources now with full access to the digital edition of The Fabricator.
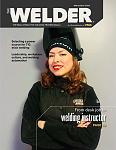
Easily access valuable industry resources now with full access to the digital edition of The Welder.
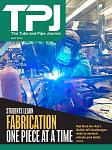
Easily access valuable industry resources now with full access to the digital edition of The Tube and Pipe Journal.
- Podcasting
- Podcast:
- The Fabricator Podcast
- Published:
- 04/16/2024
- Running Time:
- 63:29
In this episode of The Fabricator Podcast, Caleb Chamberlain, co-founder and CEO of OSH Cut, discusses his company’s...
- Trending Articles
Tips for creating sheet metal tubes with perforations
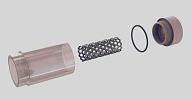
JM Steel triples capacity for solar energy projects at Pennsylvania facility
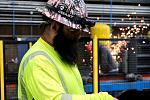
Are two heads better than one in fiber laser cutting?
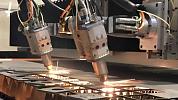
Supporting the metal fabricating industry through FMA
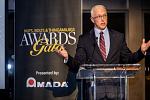
Omco Solar opens second Alabama manufacturing facility
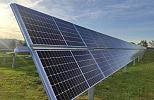
- Industry Events
16th Annual Safety Conference
- April 30 - May 1, 2024
- Elgin,
Pipe and Tube Conference
- May 21 - 22, 2024
- Omaha, NE
World-Class Roll Forming Workshop
- June 5 - 6, 2024
- Louisville, KY
Advanced Laser Application Workshop
- June 25 - 27, 2024
- Novi, MI