Editor-in-Chief
- FMA
- The Fabricator
- FABTECH
- Canadian Metalworking
Categories
- Additive Manufacturing
- Aluminum Welding
- Arc Welding
- Assembly and Joining
- Automation and Robotics
- Bending and Forming
- Consumables
- Cutting and Weld Prep
- Electric Vehicles
- En Español
- Finishing
- Hydroforming
- Laser Cutting
- Laser Welding
- Machining
- Manufacturing Software
- Materials Handling
- Metals/Materials
- Oxyfuel Cutting
- Plasma Cutting
- Power Tools
- Punching and Other Holemaking
- Roll Forming
- Safety
- Sawing
- Shearing
- Shop Management
- Testing and Measuring
- Tube and Pipe Fabrication
- Tube and Pipe Production
- Waterjet Cutting
Industry Directory
Webcasts
Podcasts
FAB 40
Advertise
Subscribe
Account Login
Search
Engaging the millennials
- By Dan Davis
- May 23, 2014
A majority of the U.S. workforce is about to clock out for the last time, and that’s leaving industry and educational institutions scrambling to find out who will replace the baby boomers as they retire.
That was the prime motivator for the first Fabricators & Manufacturers Association’s Technology Educators and Manufacturers (T.E.A.M.) Summit three years ago, and this year’s edition of the conference carried a similar theme: How can manufacturers and educators collaborate to help close this skills gap? Plenty of discussion revolved around competency-based learning, learning models, and skills certifications, but a lot of focus fell on just trying to get the millennials, those born between 1977 and 1998, interested in manufacturing.
In her keynote, Diane Thielfoldt, co-founder of The Learning Café, reminded the audience of educators and manufacturing employers that baby boomers are exiting the manufacturing workforce at a rapid pace. About 8,000 boomers, those born between 1946 and 1964, turn 65 every day. By 2016, 25 percent of all U.S. employees will be seniors.
Who will replace them? It’s not going to be Generation X, who were born between 1965 and 1976, because there simply aren’t enough of them. Further complicating the matter is the fact that Gex X women are showing greater tendencies of leaving the workforce in favor of raising the family or some other non-work-related endeavor, Thielfoldt added.
That leaves the millennials, 83 percent of which admit to sleeping with their smartphone, according to Thielfoldt. They are a different breed.
“They admit that they don’t have the same beliefs about work as older generations,” she said.
To be successful in the manufacturing environment, millennials need “fast and frequent” feedback, Thielfoldt said. They need coaching. They require schedules of work activity to be laid out in front of them. They want to be challenged. It sounds a bit like micromanaging, but in the end, this type of interaction with millennials works well, she added.
On the Metal Fabricating Front
During a panel session featuring manufacturers that are actively looking to bring younger workers into their facilities, all admitted the necessity of reaching out to not just community colleges, but also elementary, middle, and high schools. In short, the manufacturers—Shickel Corp., Bridgewater, Va.; Wyoming Machine, Stacy, Minn.; and Barnes Aerospace, Ogden, Utah—rarely turn down an opportunity to take people through their facilities. Visitors get an upclose opportunity to see what metal manufacturing—and the related skills and technology—is all about.
“We feel it’s important to get teachers and counselors into our facility because we find that their perception of manufacturing is not always what is actually out there,” said Jeff Stapel, Shickel’s human resources manager.
To be fully effective, the panelists agreed manufacturing companies have to be committed to more than just an occasional tour. For example, these manufacturers provide advisers to local technical training programs, have representatives actively interacting with technical curriculum developers at nearby community colleges, provide judges for activities such as SkillsUSA, offer internships to local students, and support specialized recruitment programs that target young girls or military veterans.
What seemed to emerge as a point of concern among the panelists was that many of these efforts are targeted at high school and postsecondary students, when in fact most of those young people probably have already dismissed manufacturing as an intriguing occupational option. They are beyond the point of really being influenced, according to Lori Tapani, Wyoming Machine’s co-president. She noticed this in a Women in Technology program that her company and nearby Pine Technical College put together each year.
“What we have found is that if you want to reach out to the girls, you have to do it in middle school,” she said.
On the Technical Education Front
The Ogden-Weber Applied Technology College (OWATC), where the T.E.A.M. Summit was held May 19-21, is taking a different approach to preparing the next generation of manufacturing workers as well. The school and its seven sister campuses spread across Utah are competency-based learning institutions: Students advance when they show they can competently complete the task assigned to them, not when they muster a passing grade on a written exam.
For example, as part of the WOATC CNC Operations 1 curriculum, the student must complete projects that reflect accuracy in terms of correctly reading blueprints, properly deburring and measuring, and conducting a complete final inspection. The student has two attempts to make the “article,” as machining program coordinator Bret Holmes called it, and if the pupil isn’t successful during those two attempts, he or she has to consult the instructor.
Also, this particular program has open enrollment. An orientation program is held every Monday. As a result, the program is filled with people at different stages of the curriculum, all working at their own pace. The students set their own schedule and don’t have many excuses if they aren’t staying on top of their coursework, Holmes said.
The WOATC curriculum helps to produce skilled workers at three machinist levels: 1, 2, and 3. Holmes said that many students don’t advance to the second and third levels as they have job opportunities with nearby manufacturing companies after the complete the first level of training. In some instances, high school students have completed the Machinist Level 1 curriculum, but have to wait until accepting full-time jobs because they have yet to graduate from high school.
JD Machine, an Ogden, Utah, machine job shop that also does some sheet metal fabricating as a value-added operations, has established a formal apprenticeship program with OWATC machining students. They are paid to learn on the job and also get one paid hour per week while at work to study course curriculum or work on class projects. JD Machine management indicated that the apprenticeship program was key in helping it to ramp up to 140 employees over the past five years, a more than 30 percent increase.
“A big reason for our success is the ability to access skilled workers, and that is made possible because of the relationship with Ogden-Weber,” said JD Machine President Matt Wardle, who has been involved with the college’s manufacturing technology program for the past 20 years. In fact, his son is halfway through the school’s machinist program.
Wardle said JD Machine’s relationship with its local community college is good not just for its business, but for local industry too—even those manufacturers that may not be engaged in supporting the school’s educational efforts but still benefit from hiring its graduates.
“At JD Machine, we feel a responsibility to get the word out about the great opportunities in the skilled trades,” Wardle said.
The opportunities will be there for workers in the future. Todd Bingham, president, Utah Manufacturers Association, told summit attendees during a lunchtime address that they have no other choice than to be successful in inspiring the next generation to follow a manufacturing career path. He used a recent announcement of private jet manufacturer SyberJet’s new assembly facility to be constructed in Cedar City, Utah. It’s going to need 400 new manufacturing workers within the next six years.
“They have to come from somewhere,” he said.
subscribe now
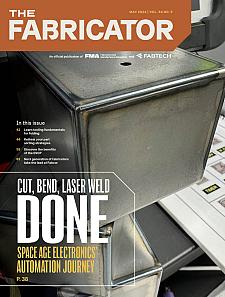
The Fabricator is North America's leading magazine for the metal forming and fabricating industry. The magazine delivers the news, technical articles, and case histories that enable fabricators to do their jobs more efficiently. The Fabricator has served the industry since 1970.
start your free subscriptionAbout the Author
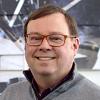
Dan Davis
2135 Point Blvd.
Elgin, IL 60123
815-227-8281
Dan Davis is editor-in-chief of The Fabricator, the industry's most widely circulated metal fabricating magazine, and its sister publications, The Tube & Pipe Journal and The Welder. He has been with the publications since April 2002.
- Stay connected from anywhere
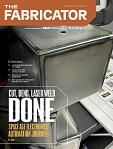
Easily access valuable industry resources now with full access to the digital edition of The Fabricator.
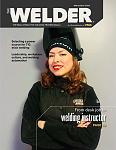
Easily access valuable industry resources now with full access to the digital edition of The Welder.
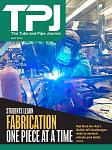
Easily access valuable industry resources now with full access to the digital edition of The Tube and Pipe Journal.
- Podcasting
- Podcast:
- The Fabricator Podcast
- Published:
- 04/16/2024
- Running Time:
- 63:29
In this episode of The Fabricator Podcast, Caleb Chamberlain, co-founder and CEO of OSH Cut, discusses his company’s...
- Trending Articles
Tips for creating sheet metal tubes with perforations
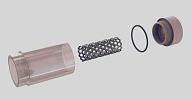
JM Steel triples capacity for solar energy projects at Pennsylvania facility
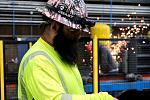
Are two heads better than one in fiber laser cutting?
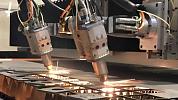
Supporting the metal fabricating industry through FMA
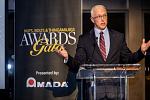
Omco Solar opens second Alabama manufacturing facility
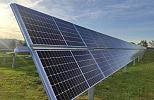
- Industry Events
16th Annual Safety Conference
- April 30 - May 1, 2024
- Elgin,
Pipe and Tube Conference
- May 21 - 22, 2024
- Omaha, NE
World-Class Roll Forming Workshop
- June 5 - 6, 2024
- Louisville, KY
Advanced Laser Application Workshop
- June 25 - 27, 2024
- Novi, MI