Editor-in-Chief
- FMA
- The Fabricator
- FABTECH
- Canadian Metalworking
Categories
- Additive Manufacturing
- Aluminum Welding
- Arc Welding
- Assembly and Joining
- Automation and Robotics
- Bending and Forming
- Consumables
- Cutting and Weld Prep
- Electric Vehicles
- En Español
- Finishing
- Hydroforming
- Laser Cutting
- Laser Welding
- Machining
- Manufacturing Software
- Materials Handling
- Metals/Materials
- Oxyfuel Cutting
- Plasma Cutting
- Power Tools
- Punching and Other Holemaking
- Roll Forming
- Safety
- Sawing
- Shearing
- Shop Management
- Testing and Measuring
- Tube and Pipe Fabrication
- Tube and Pipe Production
- Waterjet Cutting
Industry Directory
Webcasts
Podcasts
FAB 40
Advertise
Subscribe
Account Login
Search
Fabricating thoughts from the road
- By Dan Davis
- June 6, 2014
I, sir, am no Jack Kerouac, but I was on the road quite a bit in late spring and came away with some interesting tidbits.
At the Fabricators & Manufacturers Association’s Technology Educators and Manufacturers Summit in Ogden, Utah, attendees had the opportunity to hear from panelists on the subject “Transitioning to the next generation of company leaders.” On that panel Steve Moore, general manager, Barnes Aerospace Fabrications, Ogden, Utah, shared some of the steps his company has taken to create a culture of continuous improvement that is sustained by all employees, not simply driven down from the management suite.
“We have tried to change the culture from ‘having to’ to ‘wanting to,’” Moore told the audience.
Part of that effort to boost employee engagement is “Do Anything Fridays.” On that day every week, employees leaving their manufacturing duties behind and “do a deep dive” into 6S, Moore said. (6S is based on a lean manufacturing tool borrowed from the Toyota Production System that helps to promote a clean and orderly work environment. Some U.S. companies later added “safety” to the 5S method—sort, stabilize, shine, standardize, and sustain—to focus more importance on worker safety.)
However, once all of the production areas have been organized and any workplace process issues have been addressed, employees have the opportunity to tackle whatever work-related activity they want to do. It doesn’t have to be on a schedule. It doesn’t have to be part of a long-term project. It could be time set aside for mentoring or skill improvement. It’s up to the individual employee.
Moore said Barnes Aerospace Fabrications started this unusual approach to Fridays about two years ago and he believes the results have been well worth the freedom given to employees. Unburdened by daily production pressures, the employees can calmly and casually think about how they work. Moore said that such engagement has resulted in some great shop floor improvements that might not have otherwise occurred.
***During that same panel session, Jeff Stapel, human resource and safety manager, Shickel Corp., Bridgewater, Va., said his company allows its employees to use the shop and its equipment to work on their own metal fabricating projects when they clock out. Again, this type of perk helps to strengthen the bond between employer and employee. It also helps to shapren skills as employees continue to use their fabricating talents on their own time, perhaps even trying out new things that may prove beneficial for a customer project down the road.
“We have a lot of trailers being worked on during weekends,” Stapel said.
*** Diane Thielfoldt, co-founder of The Learning Café and frequent contributor to FMA conferences, talked about integrating the next generation of workers, called millennials because they were the last large demographic group born around the turn of the century (1977-1998), and some of the challenges that brings with it. Many baby boomers (born 1946-1964) and Generation Xers (1965-1976) like to point out that today’s young people think they know everything and want to be paid like it right from the start; in a way, that’s not too far from the truth. Millennials need constant reassurance and interaction so that they know what needs to be worked on and what’s next once the current project is finished. They need a form of micromanaging to be successful. That translates into a need for metal fabricators to make a real commitment to new workers in this age group right from the start. Thielfoldt said that the onboarding process for a millennial can last anywhere from 90 days to two years. It definitely requires more than a two-hour meeting with the human resources director and then turning the employee loose on the shop floor. She said fabricating shops should plan to have formal and ongoing mentoring programs to help bring millennials along as they venture into a manufacturing career. *** FABTECH® Mexico, held in Mexico City in early May, welcomed more than 500 exhibitors and 11,000 attendees over the three-day show. All forms of advanced fabricating equipment—fiber laser cutting machines, modern press brakes, and robotic welding cells, for example—could be found on the show floor, but the number of servo-driven mechanical stamping presses was noteworthy. Mexican manufacturers have a thirst for the latest forming technology. It’s easy to understand why when you consider how the country has transformed into an automobile manufacturing hub. By 2018, Mexican factories are expected to produce more than 4 million vehicles, which is pretty strong growth considering that the country produced only 2.93 million in 2013. Honda, Mazda, and Nissan have all opened production plants in Mexico within the past 12 months. The North American Free Trade Agreement is 20 years old, and we still haven’t seen it completely play out. I guess some things simply don’t move at the speed of the Internet.subscribe now
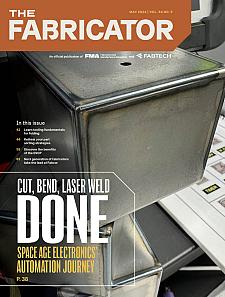
The Fabricator is North America's leading magazine for the metal forming and fabricating industry. The magazine delivers the news, technical articles, and case histories that enable fabricators to do their jobs more efficiently. The Fabricator has served the industry since 1970.
start your free subscriptionAbout the Author
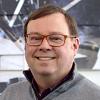
Dan Davis
2135 Point Blvd.
Elgin, IL 60123
815-227-8281
Dan Davis is editor-in-chief of The Fabricator, the industry's most widely circulated metal fabricating magazine, and its sister publications, The Tube & Pipe Journal and The Welder. He has been with the publications since April 2002.
- Stay connected from anywhere
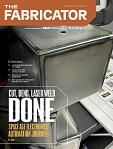
Easily access valuable industry resources now with full access to the digital edition of The Fabricator.
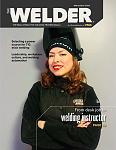
Easily access valuable industry resources now with full access to the digital edition of The Welder.
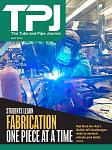
Easily access valuable industry resources now with full access to the digital edition of The Tube and Pipe Journal.
- Podcasting
- Podcast:
- The Fabricator Podcast
- Published:
- 04/16/2024
- Running Time:
- 63:29
In this episode of The Fabricator Podcast, Caleb Chamberlain, co-founder and CEO of OSH Cut, discusses his company’s...
- Trending Articles
Tips for creating sheet metal tubes with perforations
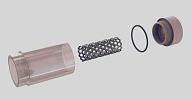
JM Steel triples capacity for solar energy projects at Pennsylvania facility
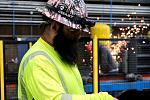
Are two heads better than one in fiber laser cutting?
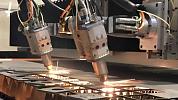
Supporting the metal fabricating industry through FMA
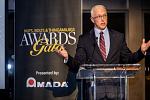
Omco Solar opens second Alabama manufacturing facility
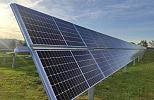
- Industry Events
16th Annual Safety Conference
- April 30 - May 1, 2024
- Elgin,
Pipe and Tube Conference
- May 21 - 22, 2024
- Omaha, NE
World-Class Roll Forming Workshop
- June 5 - 6, 2024
- Louisville, KY
Advanced Laser Application Workshop
- June 25 - 27, 2024
- Novi, MI