Editor-in-Chief
- FMA
- The Fabricator
- FABTECH
- Canadian Metalworking
Categories
- Additive Manufacturing
- Aluminum Welding
- Arc Welding
- Assembly and Joining
- Automation and Robotics
- Bending and Forming
- Consumables
- Cutting and Weld Prep
- Electric Vehicles
- En Español
- Finishing
- Hydroforming
- Laser Cutting
- Laser Welding
- Machining
- Manufacturing Software
- Materials Handling
- Metals/Materials
- Oxyfuel Cutting
- Plasma Cutting
- Power Tools
- Punching and Other Holemaking
- Roll Forming
- Safety
- Sawing
- Shearing
- Shop Management
- Testing and Measuring
- Tube and Pipe Fabrication
- Tube and Pipe Production
- Waterjet Cutting
Industry Directory
Webcasts
Podcasts
FAB 40
Advertise
Subscribe
Account Login
Search
Fabricators and engineers: A failure to communicate
To acknowledge some communication problems exist is the first step to improving the relationship
- By Dan Davis
- September 19, 2018
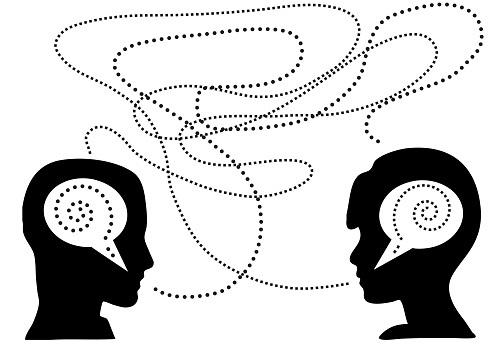
Communication gaps regularly occur between engineers and fabricators. To solve the problem, both sides need to listen and be open to learning from each other.
In late August The FABRICATOR’s Facebook page ran a meme (see Figure 1) poking fun at engineers. The black-and-white photo, likely from the early 20th century, shows a welder with his hood up asking a priest sitting next to him, “Am I going to hell, father?” The priest responds, “Oh no, son. The good Lord knows why you swear and drink often. He knows it’s because of engineers. He knows your frustration.”
Well, that attempt at humor proved to be unfunny to engineers who saw it. They were quick to defend themselves as people who work with welders to make their work easier. These engineers communicated with the shop floor to explain why certain requests were made on the drawings. One engineer summed it up nicely: “That holier than thou … s**t don’t fly with me.”
But there’s a reason that meme received more than 260 likes and was shared more than 1,500 times: It’s reality for a lot of welders and fabricators.
Yuval Doron, founder and president, Exosent Engineering, College Station, Texas, agrees. He’s a mechanical engineer who also happens to be a fabricator. (You can read more about him and his engineering/fabricating firm Exosent Engineering in “New pressure vessel designs keep roads safer,” p. XX.) In fact, he was solely responsible for running the company’s four-roll plate roller until this summer, when a longtime employee was trained to do the same. Doron also lectures in the engineering department at Texas A&M, so he has seen all sides of this discussion.
“There's a massive disconnect. It’s a broken chain link, if you will, between the mechanical engineer/engineering education and the practical application of engineering methodology,” he said. “One of the reasons they still keep me [at Texas A&M] is because I'm able to fill in the gap between what's in the field and what’s in the book.”
Doron explained that mechanical engineering programs have not changed much over the past several decades, which is OK in terms of learning principles that will last a lifetime, but not great at keeping tabs on what is happening in private industry. The situation is exacerbated with many of these universities focusing solely on research. That creates a “revolving door scenario,” Doron said, where engineering students pursue advanced degrees and eventually earn teaching and research jobs at the university level, but never really spend any time in the real world practicing what they learned in school. It’s basically the inexperienced teaching the inexperienced.
That’s why it’s so important that metal fabricating companies open their doors to students of all ages. Engineering students at the college level need to understand what has to take place to create metal parts in an efficient and cost-effective way, and to do that, they must be familiar with how fab operations work.
Of course, not all engineers are clueless when it comes to metal fabricating. Engineers who are familiar with punched-hole-to-material thickness ratios and and K-factors are valuable resources.
Phil Carlon, director of operations, Enterprise Welding & Fabricating Inc., Mentor, Ohio, earned a bachelor’s degree in mechanical engineering from Youngstown State in 2008, but he also started welding in high school and worked in a fabricating shop during college. He got into manufacturing and has been there ever since, which helps to give him instant credibility with the shop floor.
“It helps here with things like pushing through new projects,” Carlon said. “You go out, and you have to kind of earn the trust of the guys. It makes it a lot easier when you can go and say, ‘This works because of this,’ and then they go do it and realize I know what I’m talking about. So that definitely helps.”
And while it may be easy to laugh about the difficulties that some engineers cause for fabricators, engineers should be recognized for what they can bring to the table. Doron’s company started out strictly as an engineering firm, and its design work has led to some noteworthy advances in pressure vessel tanker designs. Plate rolling skills are needed to fabricate the cones that are a key part of the vessel designs, but drawings need to be created before those vessel components are fabricated.
Engineers are exposed to the latest in new material developments and advanced design tools that, frankly, may not be communicated to the manufacturing masses for several years, if ever. Engineering programs are producing talented individuals who sometimes need a refresher course on manufacturing basics.
So when it comes down to the fabricator-engineer relationship, it’s about communication. Both sides need to listen and be open-minded to change, when they can. A failure to communicate only creates frustration and fodder for silly memes.
subscribe now
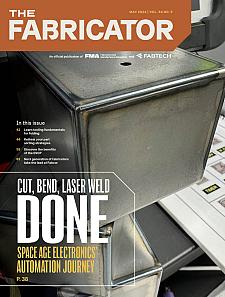
The Fabricator is North America's leading magazine for the metal forming and fabricating industry. The magazine delivers the news, technical articles, and case histories that enable fabricators to do their jobs more efficiently. The Fabricator has served the industry since 1970.
start your free subscriptionAbout the Author
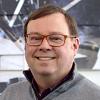
Dan Davis
2135 Point Blvd.
Elgin, IL 60123
815-227-8281
Dan Davis is editor-in-chief of The Fabricator, the industry's most widely circulated metal fabricating magazine, and its sister publications, The Tube & Pipe Journal and The Welder. He has been with the publications since April 2002.
- Stay connected from anywhere
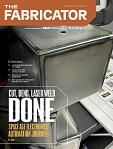
Easily access valuable industry resources now with full access to the digital edition of The Fabricator.
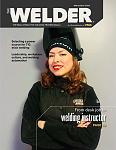
Easily access valuable industry resources now with full access to the digital edition of The Welder.
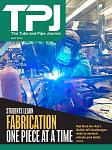
Easily access valuable industry resources now with full access to the digital edition of The Tube and Pipe Journal.
- Podcasting
- Podcast:
- The Fabricator Podcast
- Published:
- 04/16/2024
- Running Time:
- 63:29
In this episode of The Fabricator Podcast, Caleb Chamberlain, co-founder and CEO of OSH Cut, discusses his company’s...
- Trending Articles
Tips for creating sheet metal tubes with perforations
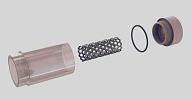
Supporting the metal fabricating industry through FMA
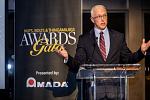
JM Steel triples capacity for solar energy projects at Pennsylvania facility
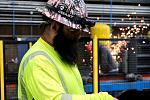
Are two heads better than one in fiber laser cutting?
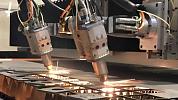
Fabricating favorite childhood memories
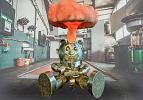
- Industry Events
16th Annual Safety Conference
- April 30 - May 1, 2024
- Elgin,
Pipe and Tube Conference
- May 21 - 22, 2024
- Omaha, NE
World-Class Roll Forming Workshop
- June 5 - 6, 2024
- Louisville, KY
Advanced Laser Application Workshop
- June 25 - 27, 2024
- Novi, MI