- FMA
- The Fabricator
- FABTECH
- Canadian Metalworking
Categories
- Additive Manufacturing
- Aluminum Welding
- Arc Welding
- Assembly and Joining
- Automation and Robotics
- Bending and Forming
- Consumables
- Cutting and Weld Prep
- Electric Vehicles
- En Español
- Finishing
- Hydroforming
- Laser Cutting
- Laser Welding
- Machining
- Manufacturing Software
- Materials Handling
- Metals/Materials
- Oxyfuel Cutting
- Plasma Cutting
- Power Tools
- Punching and Other Holemaking
- Roll Forming
- Safety
- Sawing
- Shearing
- Shop Management
- Testing and Measuring
- Tube and Pipe Fabrication
- Tube and Pipe Production
- Waterjet Cutting
Industry Directory
Webcasts
Podcasts
FAB 40
Advertise
Subscribe
Account Login
Search
FABTECH 2017—Day 2
What. A. Day.
- By Vicki Bell
- November 7, 2017
Day two of FABTECH started early. The press was invited to tour the TRUMPF booth at 8 a.m. Actually, as TRUMPF Inc. Vice President Burke Doar noted in his opening remarks, it really should be called the TRUMPF Pavilion, as the company has multiple booths at the show. Its theme for this year’s show is “the concept of connectivity.” Demonstrating connectivity, Toby Reuther, director of TRUMPF’s new Smart Factory, located in Hoffman Estates, Ill., presented a virtual tour live from the facility, which comprises 13 machines connected via TruConnect. The entire shop floor can be controlled from a control panel in the factory or remotely from a sofa anywhere. The key to successful connectivity is transparency, and the TruConnect software enables transparency.
If you visit the main booth (A2601), you can get a first-hand overview of TruConnect through the customized production of a part. After designing your part and submitting the order, you will receive live production updates as the company’s machinery, automation systems, and support technologies work together to complete the job. It’s a fun, interactive, and enlightening exercise.
Another theme for TRUMPF’s 2017 exhibit is “firsts.” Besides being the first year the company has had a facility in Illinois, it also is the first time a flagship product has been introduced in North America and not Germany. The product is the TruLaser 5030 fiber with a 10-kW TruDisk laser, which cuts up to 1-in. mild steel, up to 1.5-in. stainless, and up to 1-in aluminum. Its Smart Nozzle Automation with the integrated nozzle inspection feature now includes the option to load and unload nozzles while the machine continues cutting.
There’s a lot to see at the TRUMPF booths, so plan on staying a while. While you are there, check out the real-time order queue of machines the company has sold at the show.
The next press event was hosted by ESAB (B17074). Connectivity also was on display with CutCloud and WeldCloud, which originally was designed to collect welding data from ESAB machines. The acquisition of HKS facilitated the ability for WeldCloud to work with other manufacturers’ machines. This came from listening to customers who wanted the capability but had other machines in their shops.
Other products that captured my attention were the Suprarex™ HDX thermal cutting system with enhanced safety and the heavy-duty automated welding gantry for high productivity submerged arc welding (SAW) featuring ESAB’s ICE™ (integrated cold electrode) process. The latter’s demonstration was handled by a gentleman permanently placed with the Norfolk Naval Shipyard to support its underwater welding program. You have to see this ultraclean process with amazing repeatability.
One of my favorite booth visits each year isTigerstop (C Hall). Scott Brodie’s presentations are some of the best in the business. He knows the company’s products and demonstrates them with such enthusiasm and clarity that even the technically challenged (raising my hand) get it. Today, Scott demonstrated the a new product that eliminates the ironworker shear side “happy dance.”
With this system, the operator simply sets the cut parameter from the feed side, feeds the material, and the desired length is automatically cut and dropped. You must check that out.
Among the products so new that they didn’t make the press kit are UV-resistant labels created by a thermal transfer printer and a new “display” that shows all part info as it goes through the process. More about this later. It’s always exciting to see products so new that they were last-minute additions to the show. More than one exhibit I saw today featured these hot-off-the-press items.
A luncheon with welder and blogger Josh Welton and his wife Darla delayed my visit to Miller Electric Mfg. (B19037), but Miller was very understanding. Welton and the company go way back. He uses its equipment, and Miller frequently films him welding and uploads these videos to YouTube. In fact, a video was made at the recent SEMA show. When I have time to review the Miller press kit, I will share some of the newer products from the company, along with those from its partners, Hobart, Bernard, and Tregaskiss.
Next up was Weiler (B23058). The company featured Welton in its booth two years ago, where he demonstrated its products as he worked on his art. This year, the company has another featured guest, Barbie the welder.
Among the eight new products Weiler is showcasing is the Roughneck Max which offers a modified, tighter twist; 25 percent more wire; pretrimming on the outside; cleaning on contact; and no break in. Another is the Tiger Ceramic line allowing for less pressure, delivering more control, can suitable for hard-to-grind materials. The line includes discs for processing aluminum, which can be difficult to work with because grinding produces no sparks to indicate performance. Stop by and see these products demonstrated. Hands-on demonstrations are available.
Suhner (B35022) has three divisions: Power Tools and Abrasives, Power Transmission Elements, and Automation. The first and last are represented at FABTECH. New in Automation is the Somex deep hole milling machine, which mills up to ½-in. dia. holes up to 800 mm deep. It’s designed for a niche market and is applicable for the smaller end projects. Shops can purchase a whole system or components that will work with existing equipment. It today’s world, most of the jobs such as this are farmed out, but these relatively inexpensive options may make shops consider taking the process in-house.
Featured in the Power Tools and Abrasives division is the PowerMaster heavy-duty ceramic abrasive, which reportedly lasts longer, cuts cooler, and comprises proprietary ceramic. Another abrasive wheel is so new that it has not yet been named. Also featured is the Sun-Tint removal machine, which makes it easy to remove discoloration caused by the sun from stainless steel. This is a really interesting product.
My last stop of the day was
Airgas (B27013). I’ve been aware of the company for many years and associated it with gas supply systems. I had zero idea of the scope of its operation, and now that it’s been bought out by Air Liquide, that scope has grown by leaps and bounds based on the collaboration between the two entities. During my booth tour, I saw a small footprint robotic welding cell containing a Miller/Panasonic robot using Airgas gas and wire. I also saw a Magnatech machine that allows for cutting holes in tubes, as well as cutting flat parts from sheet metal. There also was a gantry with multiple process stations that could allow different operations to run at the same time, and a really cool machine for joining tube sections for piping operations.
And then there’s the free analysis of how changing processes can affect cost and training sessions to enable welders to make the changes to realize these cost savings. Be looking for some case studies on thefabricator.com to illustrate how these initiatives have saved shops hundreds of thousands of dollars.
That’s my wrap-up for today. Look for Day 3 highlights tomorrow.
subscribe now
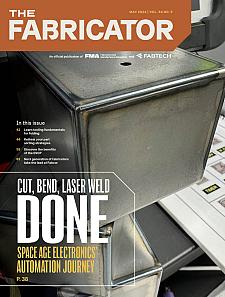
The Fabricator is North America's leading magazine for the metal forming and fabricating industry. The magazine delivers the news, technical articles, and case histories that enable fabricators to do their jobs more efficiently. The Fabricator has served the industry since 1970.
start your free subscriptionAbout the Author
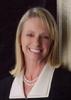
Vicki Bell
2135 Point Blvd
Elgin, IL 60123
815-227-8209
Related Companies
- Stay connected from anywhere
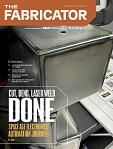
Easily access valuable industry resources now with full access to the digital edition of The Fabricator.
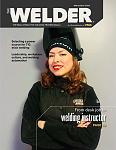
Easily access valuable industry resources now with full access to the digital edition of The Welder.
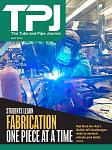
Easily access valuable industry resources now with full access to the digital edition of The Tube and Pipe Journal.
- Podcasting
- Podcast:
- The Fabricator Podcast
- Published:
- 04/16/2024
- Running Time:
- 63:29
In this episode of The Fabricator Podcast, Caleb Chamberlain, co-founder and CEO of OSH Cut, discusses his company’s...
- Trending Articles
Tips for creating sheet metal tubes with perforations
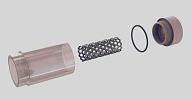
JM Steel triples capacity for solar energy projects at Pennsylvania facility
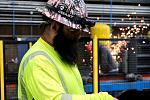
Are two heads better than one in fiber laser cutting?
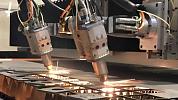
Supporting the metal fabricating industry through FMA
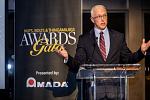
Omco Solar opens second Alabama manufacturing facility
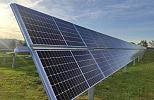
- Industry Events
16th Annual Safety Conference
- April 30 - May 1, 2024
- Elgin,
Pipe and Tube Conference
- May 21 - 22, 2024
- Omaha, NE
World-Class Roll Forming Workshop
- June 5 - 6, 2024
- Louisville, KY
Advanced Laser Application Workshop
- June 25 - 27, 2024
- Novi, MI