- FMA
- The Fabricator
- FABTECH
- Canadian Metalworking
Categories
- Additive Manufacturing
- Aluminum Welding
- Arc Welding
- Assembly and Joining
- Automation and Robotics
- Bending and Forming
- Consumables
- Cutting and Weld Prep
- Electric Vehicles
- En Español
- Finishing
- Hydroforming
- Laser Cutting
- Laser Welding
- Machining
- Manufacturing Software
- Materials Handling
- Metals/Materials
- Oxyfuel Cutting
- Plasma Cutting
- Power Tools
- Punching and Other Holemaking
- Roll Forming
- Safety
- Sawing
- Shearing
- Shop Management
- Testing and Measuring
- Tube and Pipe Fabrication
- Tube and Pipe Production
- Waterjet Cutting
Industry Directory
Webcasts
Podcasts
FAB 40
Advertise
Subscribe
Account Login
Search
FABTECH 2017—Day 4
- By Vicki Bell
- November 9, 2017
Short day, short post.
The last day of FABTECH is the shortest. Most attendees and exhibitors boarding the shuttle buses carried bags, as they would be heading home by the end of the day. For me, it was the day to make sure and stop by to see those exhibits I made promises to see at last night’s Meet the Editors and to keep rescheduled appointments. In some ways, it’s easier to conduct booth visits on this last day when there usually is lighter traffic and booth staff is less busy.
My first visit of the day was with RoboVent, a fume-extraction and air filtration system provider. The company’s products are dear to my heart, as I have a real concern about pollutants and air quality in general. My grandfather worked in the coal mines, and I’ve lost loved ones to lung cancer.
I met with Frank Cea, RoboVent’s director, marketing communications & business development, who is as knowledgeable and passionate about the company’s products as they come. I was impressed with the eQ Air Quality Monitoring System that monitors the current air quality in a facility and automatically regulates the filtration system.
I was even more impressed by the company’s new fume extraction welding gun line. Frank had an operator demonstrate the gun. As he welded behind an enclosure, I stood on my toes to peek over the side and observe, first with the fume extraction activated on the gun and then without. With, the welding process was totally smoke-free. Without it, the smoke was very much present—seen, smelled, and, no doubt, inhaled. With systems and equipment like RoboVent’s in place, manufacturing could do much to clean up its image.
My next stop was to check in on the Ajax Tocco booth, as promised. My contact wasn’t there, but I did get an opportunity to see the new Emmedi machine for tube mills introduced at the show. The compact machine is Industry 4.0-ready, short-circuit tolerant, and has silicon carbide transistors and X,Y,Z internal coil arm positioning versus an external adjustable table.
After leaving Ajax Tocco, I walked into the main concourse, where I saw several groups of students getting ready to tour the halls. I trust that the exhibitors engaged these future workers and encouraged them to pursue manufacturing careers.
Next up was a mission for a friend. When welder, blogger, and The WELDER columnist Josh Welton was at the show earlier in the week, he picked up a “mailbox” created by a Salvagnini bending machine. The company was making these at the show and giving them away. Josh was quite taken by the process and the finished product. After he went home, he posted a photo of it on Facebook, tagged me, and said that there was another box style being made, and he wished he had gotten one.
You can guess what happened next. I headed for the Salvagnini booth to scope out the activity and see if I could discover just what Josh was talking about. I read the description of the box to a company representative who first directed me to the “mailbox.” Nope. I read the description again and the lightbulb went on. I was talking about the “trash can” design. The top lifted up, and a drawer pulled out from the side. One was being made as I was there, but alas, it was made for a waiting “customer.” So, I was promised that more would be made and one would be set aside for me.
After I called on a couple more booths, I went back to Salvagnini. The bending machine was idle and no operators or visitors were around. However, I saw a “trash can” sitting on the floor with a piece of paper sitting on top that said “Lisa Belles.” Close enough. Someone helped me put it in a bag and off I went to FedEx. Josh will receive his trash can next week. All’s well that ends well, even though “I’m not Lisa.”
All’s well that ends well. That statement definitely applies to FABTECH 2017. It started well and ended well. It was one of the best shows I’ve seen in recent years.
See you next year in Atlanta!
subscribe now
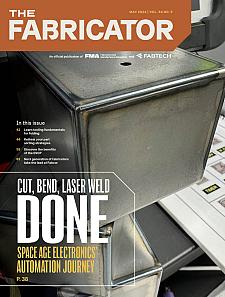
The Fabricator is North America's leading magazine for the metal forming and fabricating industry. The magazine delivers the news, technical articles, and case histories that enable fabricators to do their jobs more efficiently. The Fabricator has served the industry since 1970.
start your free subscriptionAbout the Author
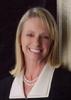
Vicki Bell
2135 Point Blvd
Elgin, IL 60123
815-227-8209
Related Companies
- Stay connected from anywhere
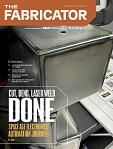
Easily access valuable industry resources now with full access to the digital edition of The Fabricator.
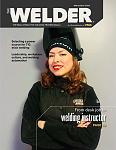
Easily access valuable industry resources now with full access to the digital edition of The Welder.
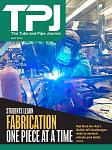
Easily access valuable industry resources now with full access to the digital edition of The Tube and Pipe Journal.
- Podcasting
- Podcast:
- The Fabricator Podcast
- Published:
- 04/16/2024
- Running Time:
- 63:29
In this episode of The Fabricator Podcast, Caleb Chamberlain, co-founder and CEO of OSH Cut, discusses his company’s...
- Trending Articles
Tips for creating sheet metal tubes with perforations
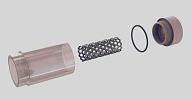
Are two heads better than one in fiber laser cutting?
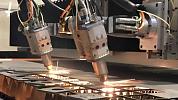
Supporting the metal fabricating industry through FMA
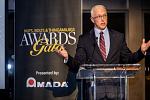
JM Steel triples capacity for solar energy projects at Pennsylvania facility
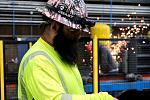
Omco Solar opens second Alabama manufacturing facility
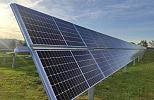
- Industry Events
16th Annual Safety Conference
- April 30 - May 1, 2024
- Elgin,
Pipe and Tube Conference
- May 21 - 22, 2024
- Omaha, NE
World-Class Roll Forming Workshop
- June 5 - 6, 2024
- Louisville, KY
Advanced Laser Application Workshop
- June 25 - 27, 2024
- Novi, MI