Sr. Digital Editor
- FMA
- The Fabricator
- FABTECH
- Canadian Metalworking
Categories
- Additive Manufacturing
- Aluminum Welding
- Arc Welding
- Assembly and Joining
- Automation and Robotics
- Bending and Forming
- Consumables
- Cutting and Weld Prep
- Electric Vehicles
- En Español
- Finishing
- Hydroforming
- Laser Cutting
- Laser Welding
- Machining
- Manufacturing Software
- Materials Handling
- Metals/Materials
- Oxyfuel Cutting
- Plasma Cutting
- Power Tools
- Punching and Other Holemaking
- Roll Forming
- Safety
- Sawing
- Shearing
- Shop Management
- Testing and Measuring
- Tube and Pipe Fabrication
- Tube and Pipe Production
- Waterjet Cutting
Industry Directory
Webcasts
Podcasts
FAB 40
Advertise
Subscribe
Account Login
Search
FABTECH Day 1: Game-changer in automated folding; Amada unveils fiber lasers
Unseasonable polar vortex hits Chicago, but FABTECH goers fill McCormick Place
- By Gareth Sleger
- November 12, 2019
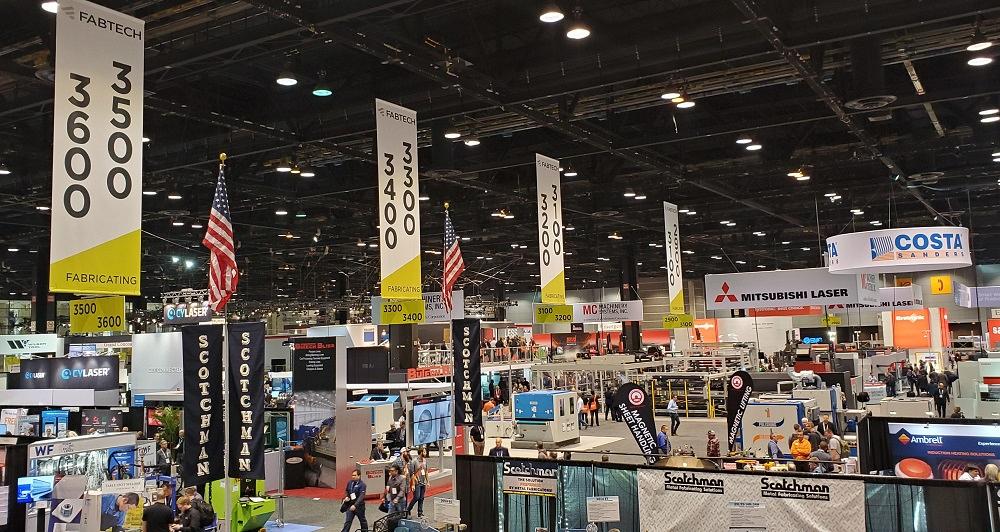
While an unseasonable polar vortex was hitting Chicago outside, Day 1 of FABTECH was booming inside the McCormick Center. Gareth Sleger
FABTECH 2019 rolled in with an unseasonable polar vortex.
Some might call it bad timing, but plenty of others saw it as all the more reason to file into Chicago’s McCormick Place. Thousands of attendees, exhibitors, and presenters filled the expo halls as snow fell and temperatures dropped.
As always, polar vortex or no polar vortex, there is plenty to see on Day 1 of FABTECH. Here are just a couple of things I took in on Monday:
Big reveal: Amada Ventis and Regius fiber lasers
On Monday morning, Amada America unveiled not just one, but two new fiber laser technologies: Ventis 3015 AJ and Regius 3015 AJ.
With both offering enhanced manipulation of the laser beam in different ways, these machines emphasis Amada’s push toward the holy grail of speed and automation.
“And quality,” Jason Hillenbrand, Amada America General Manager Blanking and Automation. “The Regius is that all-encompassing machine the highest level of every technology available. And if you’re doing a lot of stainless and aluminum, the Ventis is going to be unlike anything else.”
The Ventis operates at 4,000 watts – three to four times faster than conventional 4kw lasers. It also utilizes Amada’s new proprietary Locus Beam Control (LBC) technology, which includes three modes:
- Productivity Mode: Allows faster cuts by manipulating the laser beam.
- Quality Mode: Utilizes different pattern shapes while cutting for better edge quality.
- Kerf Control Mode: Widens the kerf for cutting thick materials and easier part removal.
“What makes [the Ventis] unique is it actually changes the pattern of the laser beam,” said Hillenbrand. “Most lasers change the actual mode, but we don't change the mode. We utilize all the power that the fiber laser can provide. So, you get a higher spot density. But what we do is we can actually move the beam and infinite number of shapes through the nozzle into the material.”
The Regius integrates four technologies: 3-axis linear drive, Amada’s ENSIS technology, laser integration system, and remote function/setup.
“The Regius machine is the pinnacle,” said Hillenbrand. “It's all the latest and highest-end technologies all rolled into one machine. So, we're using the fastest linear drives in the industry and the highest acceleration rates. We're using our 9,000-watt ENSIS technology, which automatically changes the mode of the beam from thick to thin.”
The Regius also has a more autonomous operation for the nozzle. There's an auto nozzle changer, auto nozzle inspection, auto nozzle beam alignment, lens detection to monitor if dirt/debris, and head crash recovery to prevent operators from manual troubleshooting.
Cool product: Automated metal folding for the big, thick, and heavy
After debuting internationally last year at EuroBlech in Hanover, Germany, Metalforming Inc. introduced the Schröder MAK 4 Evolution UD ATC with Advanced Handling System (AHS) to the North American market at FABTECH.
What the AHS technology offers is new level of folding automation to the big, thick, and heavy.
“We have the capability of accurately turning a 5x12 foot piece of 10 gauge and make 20-inch deep boxes,” said Geoff Stone, found and CEO of MetalForming, which is the exclusive North American partner for Schröder precision folder products. “So, we can do all the things that people have wanted to do in an automated fashion, but never been able to. There was never anything like this prior to this machine.”
Before this technology, the best option was an operator standing in the middle of a semi-automatic machine to manually move the part. The AHS device simply replaces that by-hand process but can be removed to allow for manual processes when absolutely necessary.
“We can take a blank off of any first operation system, and it’s automatically loaded onto the table, automatically manipulated through the bending sequence, and automatically kicked back out again while the next one is being loaded,” said David Prokop, MetalForming Executive Vice President.
And based on the crowd surrounding the machine in the McCormick Place Hall A, the North American metal forming sector is excited about it not only because of the game-changing automation but also because it improves safety standards.
“It completely changes what the struggles have been for years of people bending large-format parts,” said Prokop. “Big parts are very hard to bend. They're extremely unsafe. Sheet lifters don't help because if you have to flip the part, it does nothing for you. And panel benders, as great as they are for the certain sized parts, just can't bend the big, thick, and heavy parts.”
Coming later: Interview with metal artist David Madero
Later this week, I’ll have an interview with renowned metal artist David Madero. He’ll talk about his partnership ESAB, the artistic influence from his father, and much more. So, stay posted.
subscribe now
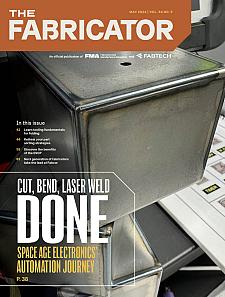
The Fabricator is North America's leading magazine for the metal forming and fabricating industry. The magazine delivers the news, technical articles, and case histories that enable fabricators to do their jobs more efficiently. The Fabricator has served the industry since 1970.
start your free subscriptionAbout the Author
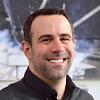
Related Companies
- Stay connected from anywhere
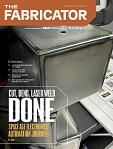
Easily access valuable industry resources now with full access to the digital edition of The Fabricator.
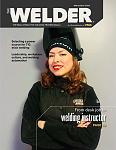
Easily access valuable industry resources now with full access to the digital edition of The Welder.
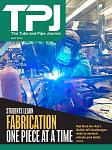
Easily access valuable industry resources now with full access to the digital edition of The Tube and Pipe Journal.
- Podcasting
- Podcast:
- The Fabricator Podcast
- Published:
- 04/16/2024
- Running Time:
- 63:29
In this episode of The Fabricator Podcast, Caleb Chamberlain, co-founder and CEO of OSH Cut, discusses his company’s...
- Trending Articles
Tips for creating sheet metal tubes with perforations
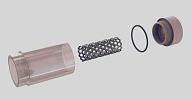
JM Steel triples capacity for solar energy projects at Pennsylvania facility
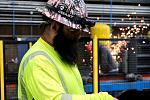
Are two heads better than one in fiber laser cutting?
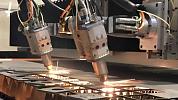
Supporting the metal fabricating industry through FMA
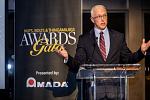
Omco Solar opens second Alabama manufacturing facility
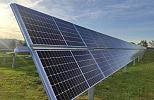
- Industry Events
16th Annual Safety Conference
- April 30 - May 1, 2024
- Elgin,
Pipe and Tube Conference
- May 21 - 22, 2024
- Omaha, NE
World-Class Roll Forming Workshop
- June 5 - 6, 2024
- Louisville, KY
Advanced Laser Application Workshop
- June 25 - 27, 2024
- Novi, MI