- FMA
- The Fabricator
- FABTECH
- Canadian Metalworking
Categories
- Additive Manufacturing
- Aluminum Welding
- Arc Welding
- Assembly and Joining
- Automation and Robotics
- Bending and Forming
- Consumables
- Cutting and Weld Prep
- Electric Vehicles
- En Español
- Finishing
- Hydroforming
- Laser Cutting
- Laser Welding
- Machining
- Manufacturing Software
- Materials Handling
- Metals/Materials
- Oxyfuel Cutting
- Plasma Cutting
- Power Tools
- Punching and Other Holemaking
- Roll Forming
- Safety
- Sawing
- Shearing
- Shop Management
- Testing and Measuring
- Tube and Pipe Fabrication
- Tube and Pipe Production
- Waterjet Cutting
Industry Directory
Webcasts
Podcasts
FAB 40
Advertise
Subscribe
Account Login
Search
From the Web: Low wages ‘major’ issue; inside a 3-D machine shop; ‘craftsmanship is still around’
- By Vicki Bell
- January 22, 2015
The skilled-labor shortage continues to be a topic of discussion, but the rhetoric around the topic has expanded to include factors beyond inadequate training programs.
In an opinion piece on grbj.com, Lou Glazer, president of Michigan Future Inc., wrote: “One problem: If there are skilled trades labor shortages, the prime cause is not an education system that overemphasizes four-year degrees, but employers’ unwillingness to raise wages. In market economies — which we all claim to believe in — price is what brings supply and demand into equilibrium. In labor markets, price is wages.
So if there is more demand for workers in an occupation than supply, the way you get more supply is by raising wages. (And other ways to make an occupation more attractive to job seekers: better work conditions, better benefits, not hiring through temporary agencies, more job security, etc.) Yet in most of the occupations where politicians and employers are complaining about labor shortages, wages are not going up.
“Manufacturing in upstate New York is far from over, and its future is in Freeville.”
So began an article about Freeville, N.Y.-based Incodema 3D, a metal additive manufacturing facility. Through an arrangement with Cornell, particularly its materials-science department, the company is taking part in Start Up NY, a program that provides a package of incentives and tax breaks that pairs start-ups with colleges and universities.
And it’s no small investment
“The heart of the operation is six $700,000 machines, part of a $10 million start-up investment financed mostly locally, that build prototype parts for customers using additive manufacturing—sometimes also called 3-D printing.”
Operations Director Scott Volk explained that parts with intricate internal connections would be all but impossible to make with traditional methods but are perfect for layer-by-layer additive construction.
"This doesn't replace traditional manufacturing but it limits the need for it," he said.
The company currently has 10 employees and expects the number to grow to as many as 75 in five years.
Winnebago Manufacturing, Blue Earth, Minn., recently was named Business of the Year by Blue Earth’s Chamber of Commerce. The 62-year-old job shop owned by Daryle Pomranke is a model of a successful shop, largely because it focuses on what it does best, makes sure it uses the best techniques and equipment for its operation, and takes care of its employees.
Pomranke acknowledged that the company, which produces products for original equipment manufacturers like Caterpiller, Emerson Electric, Surestrike, and Jarraff, is most efficient with OEM manufacturing and doesn’t want “to venture off of being a job shop.”
Its employees (42 full-time, three part-time) spend each day building the framework or parts of a larger mechanism for items such as rock crushers, excavation equipment, fire truck bodies and boom trucks, large and small generators, and industrial sized laundry equipment.
About the employees, Pomranke said, We frequently update and practice our procedures so that our employees stay up-to-date and safe.” Doing so is paying off, as the company has seen a retention of rate of 94 percent over the past few years at a time when manufacturers are struggling to find workers.
During what typically is its slowest quarter of the year, Hawkeye Industries Inc., Tupelo, Miss., is busier now than it’s been in a long time, said President and CEO Bryan Hawkins.
And with growth often comes the need for investing in technology. To that end, Hawkeye, a regional contract manufacturer of precision sheet metal components and assemblies, recently invested $750,000 in a punching machine that will expand plant capacity.
Growth also can mean job creation. Hawkeye plans to hire up to five workers.
Despite all the talk of new technology, automation, and button-pushing, there’s still a demand for the old-fashioned craftsperson.
Meet Ed Goff, the owner of Goff Metal Fab, Twin Falls, Idaho.
Profiled on magicvalley.com, Goff said, “I love metal. I bend it, cut it, weld it, grind it, shape it—that’s what I love to do.
“Craftsmanship is still around, but not as prevalent as it was many years ago. During World War II, guys sometimes had to make their own parts. Now parts are manufactured in the tens of thousands. When I make things, it is usually just one or two parts.”
Goff specializes in automotive and racing projects, but also has fabricated metal window frames and ornamental fences and gates. He has two requirements for each item he crafts: It must look cool and function.
Among his current projects are customizing a 1950 Willy’s Wagon; building a new suspension, roll cage, and bumper for a 1970 Jeepster Commando; and customizing a grille for a 1952 Dodge truck. For the grille, Goff and the owner drew up plans for flat stainless-steel tubing to give the vehicle a unique look. Unique and craftsmanship go hand-in-hand. Not the case with unique and mass-produced.
subscribe now
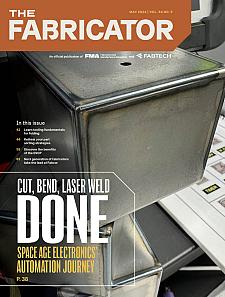
The Fabricator is North America's leading magazine for the metal forming and fabricating industry. The magazine delivers the news, technical articles, and case histories that enable fabricators to do their jobs more efficiently. The Fabricator has served the industry since 1970.
start your free subscriptionAbout the Author
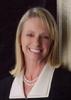
Vicki Bell
2135 Point Blvd
Elgin, IL 60123
815-227-8209
- Stay connected from anywhere
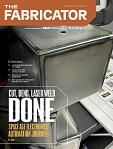
Easily access valuable industry resources now with full access to the digital edition of The Fabricator.
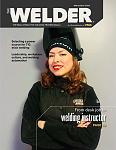
Easily access valuable industry resources now with full access to the digital edition of The Welder.
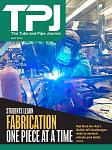
Easily access valuable industry resources now with full access to the digital edition of The Tube and Pipe Journal.
- Podcasting
- Podcast:
- The Fabricator Podcast
- Published:
- 04/16/2024
- Running Time:
- 63:29
In this episode of The Fabricator Podcast, Caleb Chamberlain, co-founder and CEO of OSH Cut, discusses his company’s...
- Trending Articles
Tips for creating sheet metal tubes with perforations
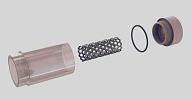
Are two heads better than one in fiber laser cutting?
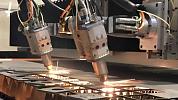
Supporting the metal fabricating industry through FMA
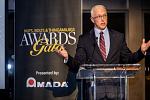
JM Steel triples capacity for solar energy projects at Pennsylvania facility
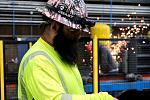
Omco Solar opens second Alabama manufacturing facility
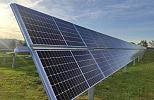
- Industry Events
16th Annual Safety Conference
- April 30 - May 1, 2024
- Elgin,
Pipe and Tube Conference
- May 21 - 22, 2024
- Omaha, NE
World-Class Roll Forming Workshop
- June 5 - 6, 2024
- Louisville, KY
Advanced Laser Application Workshop
- June 25 - 27, 2024
- Novi, MI