Owner, Brown Dog Welding
- FMA
- The Fabricator
- FABTECH
- Canadian Metalworking
Categories
- Additive Manufacturing
- Aluminum Welding
- Arc Welding
- Assembly and Joining
- Automation and Robotics
- Bending and Forming
- Consumables
- Cutting and Weld Prep
- Electric Vehicles
- En Español
- Finishing
- Hydroforming
- Laser Cutting
- Laser Welding
- Machining
- Manufacturing Software
- Materials Handling
- Metals/Materials
- Oxyfuel Cutting
- Plasma Cutting
- Power Tools
- Punching and Other Holemaking
- Roll Forming
- Safety
- Sawing
- Shearing
- Shop Management
- Testing and Measuring
- Tube and Pipe Fabrication
- Tube and Pipe Production
- Waterjet Cutting
Industry Directory
Webcasts
Podcasts
FAB 40
Advertise
Subscribe
Account Login
Search
Getting back to basics—Human element enhances a machine’s potential
- By Josh Welton
- January 22, 2015
Last year Toyota made for some sensational headlines when President Akio Toyoda went public with his company’s renewed emphasis on skilled-trades training for its workforce: “Humans Steal Jobs from Robots” (Bloomberg), “Toyota Retires Robots in Favor of Humans” (Just Car News), “Toyota is Replacing Robots with Humans” (Supply Chain Digest). The blasts all had a similar tone.
As often is the case with these “click bait” type headlines, the meat of the story isn’t accurately depicted. Toyota is not replacing machines with people; it hasn’t turned back the clock to a time when automobiles were handcrafted, and it isn’t scrapping years of innovation in automation to add humans to the payroll. But what it is doing, in my opinion, is just as important.
When automobile manufacturers first moved into the automation age, they did so with a workforce that still understood what it took to create any given part by hand. These workers had a basic, fundamental knowledge of how that part was built, and because of that they helped create and streamline the automation process and could troubleshoot when necessary.
As time went on, the majority of automotive factories became almost exclusively reliant on machines. The workforce devolved from hands-on creators and builders to merely button pushers. That’s not necessarily a bad thing for productivity, but the latent effect is a depleted knowledge and skill base. When that first generation of workers transitioned from being hands-on to basically overseeing a machine doing all the work, they had years of experience to draw from to look for hitches in the process, to troubleshoot, and to improve the operation. The farther away we get from that first generation, the less we understand the creation process at an elemental level.
So Toyota turned back the clock with a “new” training program. In plants across Japan, workstations were developed to give the younger workforce a core education in hands-on production. From welding a chassis to forging crankshafts, the next generation is being equipped with the knowledge it takes to build a car without relying on robots. In some instances, workers are even asked to sketch out certain processes on paper to force the visualization of the operation.
The results are improved quality and efficiency with automation. Armed with a deeper understanding of how and why a part is built, the workers are able to spot flaws, develop fixes, and streamline production in a way that simply was not possible when all they knew how to do was push a button. Far from replacing robots, the human element enhances the machine’s potential.
subscribe now
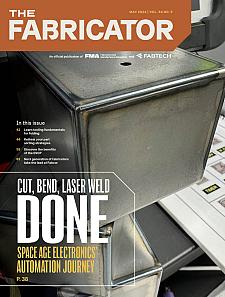
The Fabricator is North America's leading magazine for the metal forming and fabricating industry. The magazine delivers the news, technical articles, and case histories that enable fabricators to do their jobs more efficiently. The Fabricator has served the industry since 1970.
start your free subscriptionAbout the Author
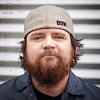
- Stay connected from anywhere
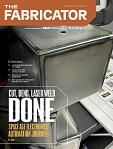
Easily access valuable industry resources now with full access to the digital edition of The Fabricator.
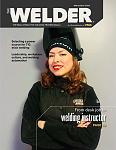
Easily access valuable industry resources now with full access to the digital edition of The Welder.
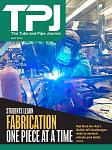
Easily access valuable industry resources now with full access to the digital edition of The Tube and Pipe Journal.
- Podcasting
- Podcast:
- The Fabricator Podcast
- Published:
- 04/16/2024
- Running Time:
- 63:29
In this episode of The Fabricator Podcast, Caleb Chamberlain, co-founder and CEO of OSH Cut, discusses his company’s...
- Trending Articles
Tips for creating sheet metal tubes with perforations
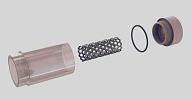
Are two heads better than one in fiber laser cutting?
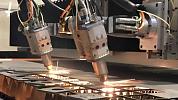
Supporting the metal fabricating industry through FMA
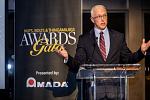
JM Steel triples capacity for solar energy projects at Pennsylvania facility
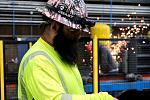
Omco Solar opens second Alabama manufacturing facility
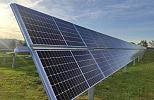
- Industry Events
16th Annual Safety Conference
- April 30 - May 1, 2024
- Elgin,
Pipe and Tube Conference
- May 21 - 22, 2024
- Omaha, NE
World-Class Roll Forming Workshop
- June 5 - 6, 2024
- Louisville, KY
Advanced Laser Application Workshop
- June 25 - 27, 2024
- Novi, MI