Editor-in-Chief
- FMA
- The Fabricator
- FABTECH
- Canadian Metalworking
Categories
- Additive Manufacturing
- Aluminum Welding
- Arc Welding
- Assembly and Joining
- Automation and Robotics
- Bending and Forming
- Consumables
- Cutting and Weld Prep
- Electric Vehicles
- En Español
- Finishing
- Hydroforming
- Laser Cutting
- Laser Welding
- Machining
- Manufacturing Software
- Materials Handling
- Metals/Materials
- Oxyfuel Cutting
- Plasma Cutting
- Power Tools
- Punching and Other Holemaking
- Roll Forming
- Safety
- Sawing
- Shearing
- Shop Management
- Testing and Measuring
- Tube and Pipe Fabrication
- Tube and Pipe Production
- Waterjet Cutting
Industry Directory
Webcasts
Podcasts
FAB 40
Advertise
Subscribe
Account Login
Search
How serious are metal fabricators about recruiting workers?
If finding skilled labor is a crisis, the metalworking industry should act accordingly
- By Dan Davis
- September 2, 2021
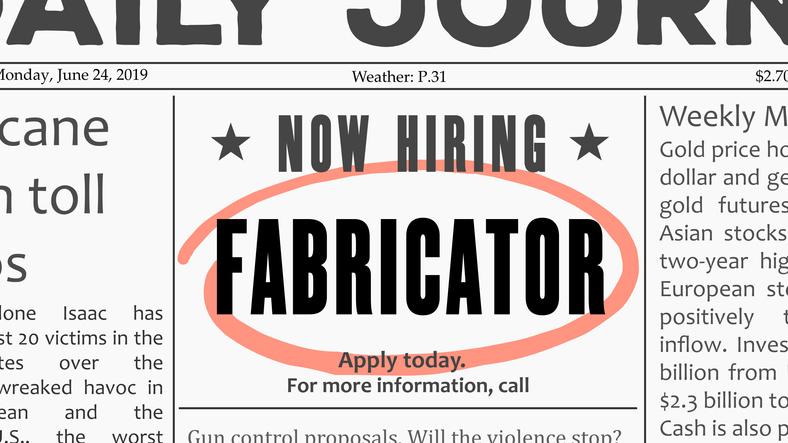
Metal fabricators regularly mention their inability to find skilled workers, but after almost a decade of hearing the same refrain, you have to ask 'Are they trying hard enough?' tupungato/iStock / Getty Images Plus
Driving down the road, I couldn’t miss the handmade sign on the right side of the road as I cruised by: “Toolmaker,” scribbled with a marker under the words “Help Wanted.”
Did I really just see that? Was the company seeking an experienced toolmaker by relying on the same tactics that people use to promote garage sales?
I shook my head as I made my way home. Good toolmakers are hard to come by, and if a company doesn’t have a relationship with a nearby community college or its own apprenticeship program, finding new tool- and diemaking talent can be an incredible challenge. But expecting a handwritten sign to lure in an experienced toolmaker isn’t a good bet.
Seeing this act of hiring desperation came around the same time that I was working on the feature about the 2021 edition of The FABRICATOR’s “What Keeps You up at Night?” survey, which will be revealed soon. This is a quick check with metal fabricating subscribers to see how they are coping with the stresses of the business.
The results from the biennial survey, particularly when it comes to the main question, haven’t changed much in recent years. Since 2013 metal fabricators have responded that the availability of skilled workers was their No. 1 concern, overshadowing things like material costs, health insurance costs, increasing customer demands, availability of credit, and lack of business planning. (In the 2009 and 2011 surveys, the economy dominated the thoughts of fabricators that were surveyed.) This year the lack of skilled workers ranked as high as it has ever been—53%, which is saying something considering that many metal fabricating companies are having to cope with steel prices that are triple what they were paying 12 months ago.
Hiring obviously is exacerbated by the fact that everyone else is looking for workers as well. It’s not uncommon to see fast food and retail touting a $15/hour wage, where it once was below $10/hour.
These companies aren’t stopping with higher pay, either. An Associated Press story from the beginning of August quoted a ZipRecruiter spokesperson as saying that more companies were offering perks such as 401(k) retirement accounts, flexible scheduling, and other benefits. Companies are getting serious about attracting workers, and that’s made the competition to stand out as a desirable employer even more difficult.
That’s why that handwritten sign advertising for a toolmaker doesn’t do much for the hiring company specifically or the manufacturing industry in general. It reinforces a stereotype of a manufacturing job as just a job, not a career. It also begs the question: Are fabricating shops content bitching about not being able to find workers, or are they willing to do something about it?
The 2021 “What Keeps You up at Night?” survey included this question: “In the areas of human resources/workforce development, what areas do you expect to devote resources to in the next two years?” The focus on recruiting and retaining skill labor was high (66%), but steps like establishing internships or apprenticeships (13%) or working with local educational institutions (8%) barely registered. If you are a regular reader of this publication, you know how successful these types of efforts can be, particularly connecting with a local high school or community college’s vocational technology program. Something as simple as meeting the program coordinator or just donating metal scraps can go a long way. Think of it as an investment in scouting for local manufacturing talent. Administrators and teachers often are on the front lines and can spot who might be a good fit for a local metal fabricating employer.
That, unfortunately, doesn’t appear to be happening in any major way—even with the light shining more favorably on the trades. Parents and students are becoming more skeptical of spending the exorbitant amounts of money on a four-year college degree that doesn’t translate into a sure and well-paying career path. Communities all over the U.S. have responded to calls from local manufacturers and invested in their community colleges, specifically by modernizing their welding training facilities. Now is the time for metal fabricating companies to put their best foot forward to show a new generation what modern manufacturing is all about.
Not all fab shops are going to feel compelled to do this, and that’s their prerogative. Maintaining external relationships with local education and political officials takes time, and that seemingly is something that fabricators are constantly short of.
If these shops want the best and the brightest working for them, however, they better make the time, or the next handwritten sign they put out will say “Closed.”
subscribe now
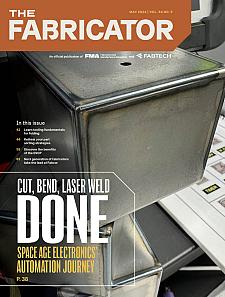
The Fabricator is North America's leading magazine for the metal forming and fabricating industry. The magazine delivers the news, technical articles, and case histories that enable fabricators to do their jobs more efficiently. The Fabricator has served the industry since 1970.
start your free subscriptionAbout the Author
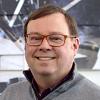
Dan Davis
2135 Point Blvd.
Elgin, IL 60123
815-227-8281
Dan Davis is editor-in-chief of The Fabricator, the industry's most widely circulated metal fabricating magazine, and its sister publications, The Tube & Pipe Journal and The Welder. He has been with the publications since April 2002.
- Stay connected from anywhere
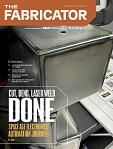
Easily access valuable industry resources now with full access to the digital edition of The Fabricator.
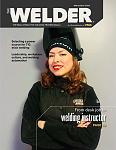
Easily access valuable industry resources now with full access to the digital edition of The Welder.
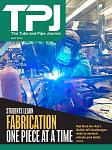
Easily access valuable industry resources now with full access to the digital edition of The Tube and Pipe Journal.
- Podcasting
- Podcast:
- The Fabricator Podcast
- Published:
- 04/16/2024
- Running Time:
- 63:29
In this episode of The Fabricator Podcast, Caleb Chamberlain, co-founder and CEO of OSH Cut, discusses his company’s...
- Trending Articles
Tips for creating sheet metal tubes with perforations
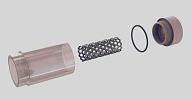
Are two heads better than one in fiber laser cutting?
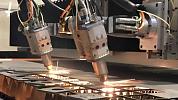
Supporting the metal fabricating industry through FMA
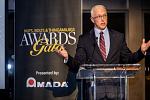
JM Steel triples capacity for solar energy projects at Pennsylvania facility
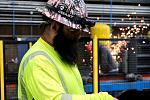
Omco Solar opens second Alabama manufacturing facility
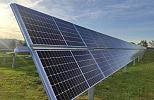
- Industry Events
16th Annual Safety Conference
- April 30 - May 1, 2024
- Elgin,
Pipe and Tube Conference
- May 21 - 22, 2024
- Omaha, NE
World-Class Roll Forming Workshop
- June 5 - 6, 2024
- Louisville, KY
Advanced Laser Application Workshop
- June 25 - 27, 2024
- Novi, MI