Senior Editor
- FMA
- The Fabricator
- FABTECH
- Canadian Metalworking
Categories
- Additive Manufacturing
- Aluminum Welding
- Arc Welding
- Assembly and Joining
- Automation and Robotics
- Bending and Forming
- Consumables
- Cutting and Weld Prep
- Electric Vehicles
- En Español
- Finishing
- Hydroforming
- Laser Cutting
- Laser Welding
- Machining
- Manufacturing Software
- Materials Handling
- Metals/Materials
- Oxyfuel Cutting
- Plasma Cutting
- Power Tools
- Punching and Other Holemaking
- Roll Forming
- Safety
- Sawing
- Shearing
- Shop Management
- Testing and Measuring
- Tube and Pipe Fabrication
- Tube and Pipe Production
- Waterjet Cutting
Industry Directory
Webcasts
Podcasts
FAB 40
Advertise
Subscribe
Account Login
Search
Lean manufacturing, line of sight, and old buildings
- By Tim Heston
- June 23, 2014
Whenever I talk with shop owners and managers, be they contract fabricators or product-line manufacturers (both usually of the high-product-mix variety), about continuous improvement, quite often they talked about line-of-sight issues. Can workers see where work is coming from and where it’s going? Such an open floor plan works well not only because parts can flow quickly from one process to the next, but also because workers see the effects of their actions all around them. It’s not about how many parts per hour they can punch, bend, or weld. It’s about how quickly can the company ship quality parts.
That was the thinking behind Gap Partners Inc.’s new facility in the hills of northern Georgia. Workers themselves helped lay out the facility, previously a Fruit of the Loom factory, where they were graced with a large, open space. The U shaped floor plan has parts coming in on one end, then making their way around to cutting, bending, hardware insertion, welding, grinding, powder coating, and assembly.
The floor is about as far as you can get from the traditional departmental layout that dominated many manufacturing facilities of the past, which emphasized what Henry Ford emphasized: local efficiency. Workers were told to do their job and focus on their department, and supervisors worked to increase the efficiency of those departments. So one department was walled from the next, keeping people focused on the job at hand. Don’t worry about the time between the customer order and the ship date; your job is to punch or bend as many units as possible.
So how do you transform such an old, “departmental” building so it abides by the concepts of lean manufacturing? At several past LeanFab Shop Tours and Workshops, events that focus on continuous improvement in metal fabrication, we’ve visited several older facilities that have effectively transformed departmental floor plans to ones that promote continuous flow.
Some aren’t perfect—there’s only so much you can do in some buildings. But a few weeks ago I attended a LeanFab event in Connecticut, hosted by TRUMPF Inc., that included a shop tour of Wiremold, one of Legrand’s largest North American facilities, in West Hartford, Conn.
There, workers fabricate enclosures and structures that hold various wires, from electrical to Cat5 internet cables. Many units are relatively simple. In fact, they’re what most people would think would be ripe for outsourcing, if not to Asia, then at least to the South or Mexico. But the company continues to manufacture in Connecticut, not an inexpensive place to do business.
Its key to success is lean manufacturing, adapted for a very high-product-mix operation. The quick-die-change process alone is something to behold. So are the buildings, including their age. One of the original facilities is supported by a grid of closely placed wooden columns.
But you can still see parts flow, and the key to it is the company’s cellular approach. In one assembly cell, you can see how wire assemblies are inserted in the sheet metal enclosure, packaged, labeled, and ready for shipment, all in a span of several meters, and all built among a forest of inconvenient wooden columns.
That’s not bad for a building that’s about 100 years old.
subscribe now
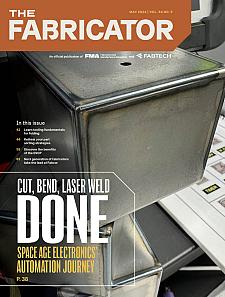
The Fabricator is North America's leading magazine for the metal forming and fabricating industry. The magazine delivers the news, technical articles, and case histories that enable fabricators to do their jobs more efficiently. The Fabricator has served the industry since 1970.
start your free subscriptionAbout the Author
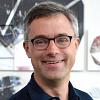
Tim Heston
2135 Point Blvd
Elgin, IL 60123
815-381-1314
Tim Heston, The Fabricator's senior editor, has covered the metal fabrication industry since 1998, starting his career at the American Welding Society's Welding Journal. Since then he has covered the full range of metal fabrication processes, from stamping, bending, and cutting to grinding and polishing. He joined The Fabricator's staff in October 2007.
Related Companies
- Stay connected from anywhere
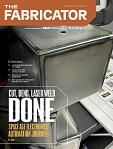
Easily access valuable industry resources now with full access to the digital edition of The Fabricator.
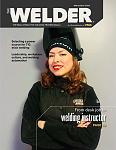
Easily access valuable industry resources now with full access to the digital edition of The Welder.
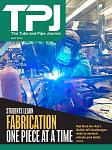
Easily access valuable industry resources now with full access to the digital edition of The Tube and Pipe Journal.
- Podcasting
- Podcast:
- The Fabricator Podcast
- Published:
- 04/30/2024
- Running Time:
- 53:00
Seth Feldman of Iowa-based Wertzbaugher Services joins The Fabricator Podcast to offer his take as a Gen Zer...
- Industry Events
Pipe and Tube Conference
- May 21 - 22, 2024
- Omaha, NE
World-Class Roll Forming Workshop
- June 5 - 6, 2024
- Louisville, KY
Advanced Laser Application Workshop
- June 25 - 27, 2024
- Novi, MI
Precision Press Brake Certificate Course
- July 31 - August 1, 2024
- Elgin,