- FMA
- The Fabricator
- FABTECH
- Canadian Metalworking
Categories
- Additive Manufacturing
- Aluminum Welding
- Arc Welding
- Assembly and Joining
- Automation and Robotics
- Bending and Forming
- Consumables
- Cutting and Weld Prep
- Electric Vehicles
- En Español
- Finishing
- Hydroforming
- Laser Cutting
- Laser Welding
- Machining
- Manufacturing Software
- Materials Handling
- Metals/Materials
- Oxyfuel Cutting
- Plasma Cutting
- Power Tools
- Punching and Other Holemaking
- Roll Forming
- Safety
- Sawing
- Shearing
- Shop Management
- Testing and Measuring
- Tube and Pipe Fabrication
- Tube and Pipe Production
- Waterjet Cutting
Industry Directory
Webcasts
Podcasts
FAB 40
Advertise
Subscribe
Account Login
Search
Learning a process is an ongoing process
- By Nick Martin
- June 30, 2016
How do you train your employees? It is a simple question, but when you think about it, how easy is it to answer?
Large companies have orientations and videos to get the ball rolling, but smaller shops like ours have to dive head-first in the shallow end and get our hands dirty.
Good training comes at a cost. You don’t normally train your experienced employees unless you purchase new equipment or new software. The vendor usually sends someone to your facility, and you dedicate as many people as possible or needed for training while still keeping the ball rolling on the production floor.
You have a limited amount of time to soak up all that knowledge, and the next questions have to be handled from a telephone or remotely connected computers. (The older generation didn’t have this luxury!) All the questions you have won’t be thought of until the comfort zone instructor has left the building. I’m sure you’ve experienced this before.
What happens when you have a machine that has been around for a while and you have a new employee who needs to learn how to use it? You should have a few people who know how and can take the time to teach the new worker. The experienced employees have to use their time to educate, and if you are lucky, they can do their jobs while class is in session.
There’s also the situation in which you have a machine that no current employee knows how to use. This is very rare, and I highly recommend not allowing it to happen. It sounds dumb, but this can happen pretty quickly in a small shop with few employees.We have a Tauring CNC angle roller that sat in our warehouse for several years, because the employees who were trained to use it were no longer with us. We basically had to force ourselves to relearn it, so we hired a guy to fly out from California to teach us.
This time we had a few guys with notepads in hand giving him their full attention, myself included. We’ve since made up lost production time with successful jobs on the machine, but like all training, it came at a price.
Our laser has been around for eight years, and our current laser operator, Jason Barnes, has been excelling at using it for a few years now. I was his trainer, and I vividly remember telling him that I couldn’t teach him some things until the teaching occasion came along. I didn’t have a schedule or timeline on how I was teaching him, because I also had my own job to do. We basically worked together, and I taught him as we went.
I remember when he asked how I learned how to run the laser. I told him that I had a week with an instructor at our shop. The look on his face was priceless! He said, “You learned how to run the laser in a week?” I told him no. I had a week to learn as much as I could from the instructor. It takes a long time to learn the peculiarities of a laser, and I will never stop learning them. Everything you learn on a day-to-day basis needs to be put in your library of shop knowledge.
When the laser is down and our team of guys can’t fix it, we call in a service tech. Jason uses this time as on-site training by picking the tech’s brain as much as he can in the short time he is there. Training can be in disguise. You need to always be on the lookout for it.
Over the past few years, I’ve trained a couple of interns, my nephew Anthony Moleta, and a couple other people on how to use Autodesk® Inventor®. I’ve learned several lessons, but I still can’t say that I have a training program. I also can’t say that I want one. Some methods work and others don’t. YouTube is a big help, but not all videos are preaching what I need to be teaching to get the job done our way. Sending employees off to training is costly, and small job shops may not have the time or money to invest.
In our shop, everyone has their role, and it is often done while wearing several hats. We are our own substitutes for jobs that often rely on one person. Who can teach you what you need to know? When you are busy every day, you don’t have time to constantly train the next guy. Learning as you go is a team effort, and we aren’t shy to ask for help or another opinion in our shop.
We’ve come to the realization that we need to be our own experts. You can’t sit around and wait on the next guy to solve problems. This is done as a whole in our shop. Learning is continuous, but we don’t sit down regularly and say we are “training.”
How does your shop go about training?
subscribe now
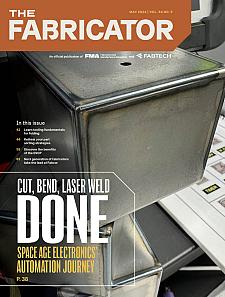
The Fabricator is North America's leading magazine for the metal forming and fabricating industry. The magazine delivers the news, technical articles, and case histories that enable fabricators to do their jobs more efficiently. The Fabricator has served the industry since 1970.
start your free subscriptionAbout the Author
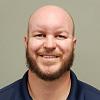
Nick Martin
2121 Industrial Park Drive SE
Wilson, NC, 27893
252-291-0925
Related Companies
- Stay connected from anywhere
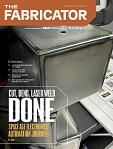
Easily access valuable industry resources now with full access to the digital edition of The Fabricator.
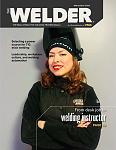
Easily access valuable industry resources now with full access to the digital edition of The Welder.
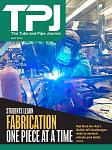
Easily access valuable industry resources now with full access to the digital edition of The Tube and Pipe Journal.
- Podcasting
- Podcast:
- The Fabricator Podcast
- Published:
- 04/16/2024
- Running Time:
- 63:29
In this episode of The Fabricator Podcast, Caleb Chamberlain, co-founder and CEO of OSH Cut, discusses his company’s...
- Trending Articles
Tips for creating sheet metal tubes with perforations
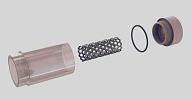
Are two heads better than one in fiber laser cutting?
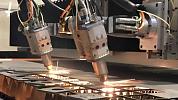
Supporting the metal fabricating industry through FMA
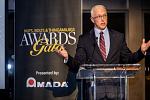
JM Steel triples capacity for solar energy projects at Pennsylvania facility
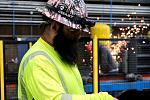
Omco Solar opens second Alabama manufacturing facility
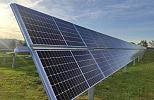
- Industry Events
16th Annual Safety Conference
- April 30 - May 1, 2024
- Elgin,
Pipe and Tube Conference
- May 21 - 22, 2024
- Omaha, NE
World-Class Roll Forming Workshop
- June 5 - 6, 2024
- Louisville, KY
Advanced Laser Application Workshop
- June 25 - 27, 2024
- Novi, MI