Editor-in-Chief
- FMA
- The Fabricator
- FABTECH
- Canadian Metalworking
Categories
- Additive Manufacturing
- Aluminum Welding
- Arc Welding
- Assembly and Joining
- Automation and Robotics
- Bending and Forming
- Consumables
- Cutting and Weld Prep
- Electric Vehicles
- En Español
- Finishing
- Hydroforming
- Laser Cutting
- Laser Welding
- Machining
- Manufacturing Software
- Materials Handling
- Metals/Materials
- Oxyfuel Cutting
- Plasma Cutting
- Power Tools
- Punching and Other Holemaking
- Roll Forming
- Safety
- Sawing
- Shearing
- Shop Management
- Testing and Measuring
- Tube and Pipe Fabrication
- Tube and Pipe Production
- Waterjet Cutting
Industry Directory
Webcasts
Podcasts
FAB 40
Advertise
Subscribe
Account Login
Search
Preparedness is the best medicine for any metal fabrication shop
When a shop is cross-trained and has automation, it can survive employee absences that might otherwise shut down competitors
- By Dan Davis
- UPDATED December 14, 2022
- December 17, 2022
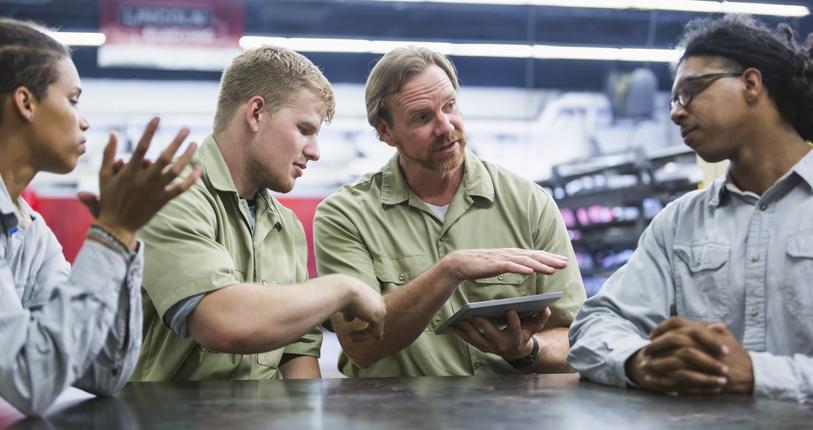
Cross-training is one way that metal fabricating companies are able to soften the impact of unexplained absences due to illness. kali9/E+/Getty Images
A rhetorical “How are things going?” to begin a conversation with a Midwest metal fabricator resulted in a statement that reflected the health situation for a good bit of the U.S. in early December: “Well, we have about 17 to 18 people out sick today, so we’re trying to work through that. It’s not easy, but we have to keep at it.”
That wasn’t too much of a surprise given other stories I heard from people elsewhere. This is the winter of our respiratory discontent.
As much as people don’t want to hear about it, COVID-19 is still floating around causing people trouble. (My 81-year-old mom going through cancer treatments was in the hospital with it.) Flu strains are no stranger this time of year. There even has been spikes of cases involving respiratory syncytial virus (RSV), which can lead to pneumonia and bronchiolitis. A power air-purifying respirator might make a good gift not only for the welder in your life, but also for other family members with big plans for the coming weekend.
But people get sick all the time, so that wasn’t the issue that came to my mind as we spoke. After hearing about the number of people who were absent because of illness, I asked, “That’s got to be difficult to get things done with that many people gone.” The metal fabricator agreed, but again reiterated that they had to deal with the reality.
For most metal fabricators, the shop floor reality is that they are busy. Staying on top of delivery deadlines is only exacerbated when key personnel are unavailable. If those absentees happen to be in an area without a lot of depth because open positions can’t be filled easily, such as in the welding department, a bottleneck can start to build and throw production flow off for several shifts.
“The Forming & Fabricating Job Shop Consumption Report” (FFJSCR) for the second quarter of 2022, a survey of membership conducted twice a year by the Fabricators & Manufacturers Association, reveals that these anecdotal tales of swamped shops are factual. In that most recent survey, respondents report a capacity utilization of 73.5%, which is pretty high for job shops that like to keep machine time open for hot jobs and other non-regular jobs, such as rework or prototyping. (Chris Kuehl, FMA’s economist, suggests that 80% to 85% is the “ideal” capacity utilization for most manufacturers.)
When you combine that statistical note with the fact that 75% of the respondents to the FFJSCR are companies with 50 or fewer employees, you are talking about companies without a lot of personnel depth to begin with. The absence of a few key skilled workers can make a tremendous impact on the day’s productivity.
If metal fabricators learned any lesson from the pandemic, however, it’s that they need to let sick people recover at home. If they bring that bug to work, they are only creating the potential for making more co-workers ill. The metal fabrication industry doesn’t find itself in the same position as the railroad industry, which practices what is called precision-scheduled railroading, which makes it almost impossible for companies to offer sick time to its limited number of employees. (In fact, to prevent the nation’s economy from grinding to a halt, President Joe Biden and Congress prevented the rail unions from striking and forced a new contact on them, one that doesn’t grant them the paid sick days they were seeking.)
Metal fabricators also have been preparing themselves for these absences with aggressive cross-training. The initial motivation, of course, was probably to ensure that someone is always available to jump on another machine or assume another task, providing the company with more flexibility in its workforce. But the push for cross-training has also helped companies dealing with illnesses and people leaving the company, either quitting or retiring.
The metal fabricator mentioned previously actually has an aggressive cross-training program. It’s very common at that shop to have one employee trained as a welder, a robot technician, a punching press operator, and a laser cutting machine operator. When all can do something, it’s fun to watch all things get done as efficiently as possible.
Of course, the continued investment in automation has helped as well. By removing employees from dull, low-skill jobs, they can be moved to more valuable work. They also avoid jobs that can cause repetitive-motion injuries. That helps to keep people on the job, not using sick leave.
In many instances, metal fabricating shops are ready to deal with waves of flus and other contagious bugs because they have to be flexible enough to deal with several customers in different manufacturing sectors with different manufacturing requirements and expectations. Survival in the metal fabricating industry means that you are ready to take on anything. It’s next man up and keep moving forward.
subscribe now
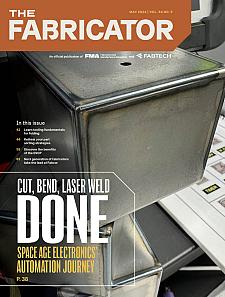
The Fabricator is North America's leading magazine for the metal forming and fabricating industry. The magazine delivers the news, technical articles, and case histories that enable fabricators to do their jobs more efficiently. The Fabricator has served the industry since 1970.
start your free subscriptionAbout the Author
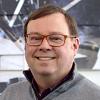
Dan Davis
2135 Point Blvd.
Elgin, IL 60123
815-227-8281
Dan Davis is editor-in-chief of The Fabricator, the industry's most widely circulated metal fabricating magazine, and its sister publications, The Tube & Pipe Journal and The Welder. He has been with the publications since April 2002.
- Stay connected from anywhere
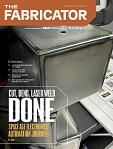
Easily access valuable industry resources now with full access to the digital edition of The Fabricator.
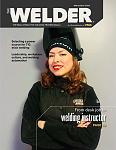
Easily access valuable industry resources now with full access to the digital edition of The Welder.
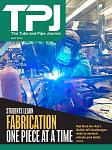
Easily access valuable industry resources now with full access to the digital edition of The Tube and Pipe Journal.
- Podcasting
- Podcast:
- The Fabricator Podcast
- Published:
- 04/16/2024
- Running Time:
- 63:29
In this episode of The Fabricator Podcast, Caleb Chamberlain, co-founder and CEO of OSH Cut, discusses his company’s...
- Trending Articles
Tips for creating sheet metal tubes with perforations
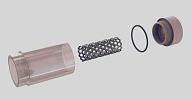
JM Steel triples capacity for solar energy projects at Pennsylvania facility
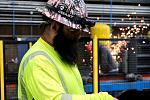
Are two heads better than one in fiber laser cutting?
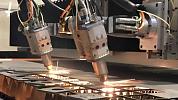
Supporting the metal fabricating industry through FMA
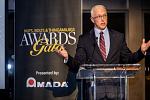
Omco Solar opens second Alabama manufacturing facility
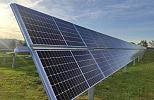
- Industry Events
16th Annual Safety Conference
- April 30 - May 1, 2024
- Elgin,
Pipe and Tube Conference
- May 21 - 22, 2024
- Omaha, NE
World-Class Roll Forming Workshop
- June 5 - 6, 2024
- Louisville, KY
Advanced Laser Application Workshop
- June 25 - 27, 2024
- Novi, MI