Editor-in-Chief
- FMA
- The Fabricator
- FABTECH
- Canadian Metalworking
Categories
- Additive Manufacturing
- Aluminum Welding
- Arc Welding
- Assembly and Joining
- Automation and Robotics
- Bending and Forming
- Consumables
- Cutting and Weld Prep
- Electric Vehicles
- En Español
- Finishing
- Hydroforming
- Laser Cutting
- Laser Welding
- Machining
- Manufacturing Software
- Materials Handling
- Metals/Materials
- Oxyfuel Cutting
- Plasma Cutting
- Power Tools
- Punching and Other Holemaking
- Roll Forming
- Safety
- Sawing
- Shearing
- Shop Management
- Testing and Measuring
- Tube and Pipe Fabrication
- Tube and Pipe Production
- Waterjet Cutting
Industry Directory
Webcasts
Podcasts
FAB 40
Advertise
Subscribe
Account Login
Search
Tapping and trapping institutional knowledge in a fab shop
Don’t let operational efficiencies walk out the door when experienced personnel leave
- By Dan Davis
- May 3, 2021
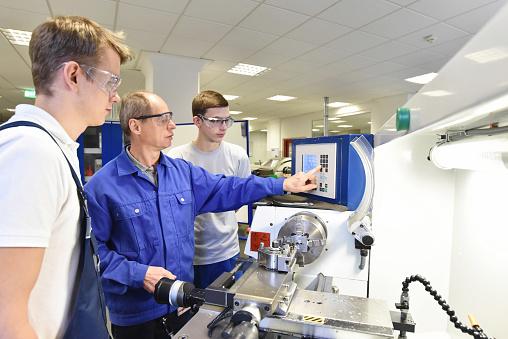
Fabricating company owners and managers need to tap the knowledge of experienced workers before they walk out the door for good. Getty Images
My little brother, who is about 2 in. taller and about 50 lbs. heavier than me, works shift work in a manufacturing plant. I had the chance to get together with him during the most recent spring break, and like always, I learned something.
Here’s his definition of institutional knowledge: “So this guy came into the break room and he wanted to use the microwave. ‘Does this thing work?’ he asked. I told him, ‘Yeah, but every time it’s used you need to unplug it. That’s why it’s unplugged now.’ So the guy plugged it in and tried to set the timer. ‘Does this thing work?’ he asked again. I told him, ‘The only button that will set the timer is the popcorn button, but it sets it for six minutes. You can’t stop it with the button on the panel. You need to unplug it when you are ready to shut the microwave down.’ So the guy put his meal in there, hit the popcorn button, and pulled the plug when his meal was heated up.”
After having a pretty good laugh, I told my brother that was the best example of institutional knowledge that I’ve ever heard. I finally learned what the popcorn button was good for on a microwave!
My brother has been at his job for almost 20 years now. With that tenure, his knowledge about making that microwave work is probably one of the least valuable things related to his job in his noggin. There’s a reason he gets a call on most of his days or nights off: He provides answers to questions about production and insights into how things might work a little more efficiently. He might not be the most valuable person in that facility, but his experience makes him more valuable than his less-experienced co-workers.
For metal fabricators, tapping and trapping institutional knowledge has been a major challenge: How do you keep the people that know the most from taking all that knowledge with them as they retire and walk out the door for good? Over the years, I’ve seen the different ways that shops have attempted to extract that institutional knowledge and make it available to others, and for the most part, owners and managers seemed to be pleased with the results.
Probably the most popular attempt at capturing an individual’s knowledge of machinery or processes is documenting detailed instructions. At one time, this meant pictures and step-by-step instructions in a workstation binder or on a nearby bulletin board. Today recording a video of a person actually going through a job is as simple as picking up a smartphone and pressing a button. In the most basic setup, the video can sit on a server and be accessed when needed. On digitally connected shop floors, the video can be attached to jobs along with the print, and it can be accessed by touchscreen monitors attached to the machine, tablets assigned to the workstation, or even a smartphone. Video is a powerful tool, and an entire generation is becoming visual learners because of the ubiquity of smartphones.
One of the more creative approaches to maintaining institutional knowledge is by enticing the knowledge-holders to stay as long as possible. I recently spoke with a small family job shop whose workforce comprised part-time fabricators of retirement age. They liked their free time in the afternoon to spend with grand kids, tend to hobbies, or just take a nap, but they also liked staying a bit busy, which made time spent on the shop floor a perfect medicine. The shop owners got a skilled and knowledgeable workforce, and the workforce had the flexibility they needed to ease into their retirement years. The shop owner joked that a youngster—a 29 year old—had just been hired, so the mentoring process has begun in earnest.
If those two scenarios don’t work, a shop can just buy some new machinery. Of course, technology is not a direct substitute for a knowledgeable individual, but maybe it makes some institutional knowledge obsolete. A new microwave that functioned as it was designed probably would have saved people a lot of frustrating moments at my brother’s place of work. That same scenario likely applies on a shop floor.
The final lesson of the wonky microwave is these attempts at capturing institutional knowledge or at least minimizing the impact of the loss of such knowledge are more successful with good communication. Most people want to help; they just need to be asked. That’s how you find out how the popcorn button makes all things right.
subscribe now
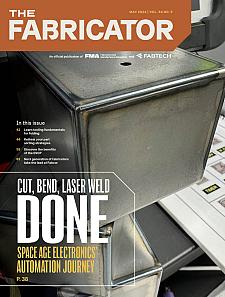
The Fabricator is North America's leading magazine for the metal forming and fabricating industry. The magazine delivers the news, technical articles, and case histories that enable fabricators to do their jobs more efficiently. The Fabricator has served the industry since 1970.
start your free subscriptionAbout the Author
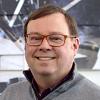
Dan Davis
2135 Point Blvd.
Elgin, IL 60123
815-227-8281
Dan Davis is editor-in-chief of The Fabricator, the industry's most widely circulated metal fabricating magazine, and its sister publications, The Tube & Pipe Journal and The Welder. He has been with the publications since April 2002.
- Stay connected from anywhere
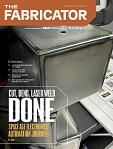
Easily access valuable industry resources now with full access to the digital edition of The Fabricator.
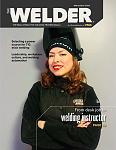
Easily access valuable industry resources now with full access to the digital edition of The Welder.
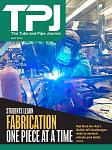
Easily access valuable industry resources now with full access to the digital edition of The Tube and Pipe Journal.
- Podcasting
- Podcast:
- The Fabricator Podcast
- Published:
- 04/16/2024
- Running Time:
- 63:29
In this episode of The Fabricator Podcast, Caleb Chamberlain, co-founder and CEO of OSH Cut, discusses his company’s...
- Trending Articles
Tips for creating sheet metal tubes with perforations
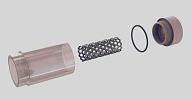
Supporting the metal fabricating industry through FMA
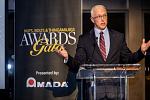
JM Steel triples capacity for solar energy projects at Pennsylvania facility
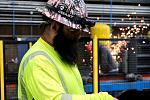
Are two heads better than one in fiber laser cutting?
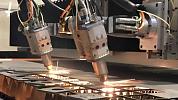
Fabricating favorite childhood memories
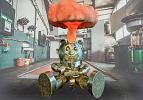
- Industry Events
16th Annual Safety Conference
- April 30 - May 1, 2024
- Elgin,
Pipe and Tube Conference
- May 21 - 22, 2024
- Omaha, NE
World-Class Roll Forming Workshop
- June 5 - 6, 2024
- Louisville, KY
Advanced Laser Application Workshop
- June 25 - 27, 2024
- Novi, MI