- FMA
- The Fabricator
- FABTECH
- Canadian Metalworking
Categories
- Additive Manufacturing
- Aluminum Welding
- Arc Welding
- Assembly and Joining
- Automation and Robotics
- Bending and Forming
- Consumables
- Cutting and Weld Prep
- Electric Vehicles
- En Español
- Finishing
- Hydroforming
- Laser Cutting
- Laser Welding
- Machining
- Manufacturing Software
- Materials Handling
- Metals/Materials
- Oxyfuel Cutting
- Plasma Cutting
- Power Tools
- Punching and Other Holemaking
- Roll Forming
- Safety
- Sawing
- Shearing
- Shop Management
- Testing and Measuring
- Tube and Pipe Fabrication
- Tube and Pipe Production
- Waterjet Cutting
Industry Directory
Webcasts
Podcasts
FAB 40
Advertise
Subscribe
Account Login
Search
The pains of routine machine maintenance in a job shop
Why do machine problems hit all at once on a Monday?
- By Nick Martin
- August 22, 2022
You’ve probably heard the term “Sunday Funday”: extending the weekend a little too far or doing something spontaneous. And it’s most likely the reason why some people don’t show up to work on a Monday. Some of us have been there. We all need to let our guard down every now and then.
But is there such a thing as “Monday Funday?” I doubt it. Every now and then we have one of those Mondays that turn out to be a real head turner in the Branes MetalCrafters job shop, leaving us wondering, “What the heck is going on?”
A recent “Monday Funday” started off when our laser operator Derrick Whitaker approached me as soon as I walked in the door. He said the laser chiller wasn’t pumping enough coolant to turn on the laser (Image 1). We just had flushed the system and the pump was putting out more liters per minute than I was used to seeing on the readout. All was good until now. I told him to give me a few minutes and I would go take a look at it. I went into the office and knocked out a few emails and then BAM! The whole building lost power.
I immediately went out to the shop and told Derrick to kill the breakers to the lasers in case the power came back on. Machines don’t like getting shut down unexpectedly. We did as much prep as we could and then proceeded to figure out why we lost power. The city came out and said we no had power going up to the building so something else must be wrong.
Come to find out, the main breaker to the building had water all over it and it had shorted out. How in the heck could that have happened? Our building is fairly new, but it had rained an awful lot the weekend before. The water had to have come from inside the building. We came to the conclusion that the automatic water blow-off line from the air compressor got turned and shot water across the utility room and all over the main breaker.
In Eastern North Carolina, the humidity can get pretty bad. Your clothes are instantly sticky as soon as you walk outside, and everything eventually is wet. The compressors were producing a lot more water than normal and weren’t draining properly. It was fixed immediately, so we shouldn’t have that issue ever again.
The electrician who came to help us out used some air cans that we had in the office to clean out keyboards and computers. We got everything back up and running after losing about three hours of production.
Once things settled down, I began looking at the pump to the laser and we discovered that the pump was failing. We called a repairperson to come diagnose, but they couldn’t come to the shop for a few days. That was OK given that we didn’t have a whole lot of work for our older CO2 laser (Image 2).
A few days later, I heard the forklift cranking repeatedly. I looked over and the first thing I noticed was that no one was on it or around it. A coworker ran over and pulled the key to make sure the ghost rider didn’t want to go for a spin. That was very odd. It was time to call the forklift pros and get that thing fixed. They said they’d come out to the shop in a couple days.
Fast forward to following Monday, and we were greeted with a new problem. The saw wasn’t pumping coolant to the blade. Shop lead Nick Trueheart started troubleshooting with my dad, Tim Martin, and they narrowed it down to a couple culprits. Tim decided to call a local repairman to come fix it since we had other things that needed to be done.
While Nick and Tim were working on the saw, the forklift serviceman and the chiller serviceman were on-site as well. The forklift guy took less than 30 minutes to diagnose and repair the forklift. He was in and out. The chiller repairman worked with Derrick and I to figure out what was going on. He checked it out, but didn’t see anything out of the ordinary. We blew out some lines and narrowed it down to the pump. That's what he was there to do. As soon as the case to the pump was cracked open, the impeller started to fall apart. And that was why we couldn’t get the laser up to pressure.
Not the most major of fixes, but enough to slow us down for over a week. The guy working on the saw found that our pump had failed. What are the chances that two pumps fail on two important machines in almost a week apart? We told him to get the parts on order and do what he could.
No one knows what it is about Mondays. Normally, routine maintenance problems like this at our shop are more spread out, and we just roll with the punches. But every now and then, Mother Nature decides to screw with us and they hit all at once.
subscribe now
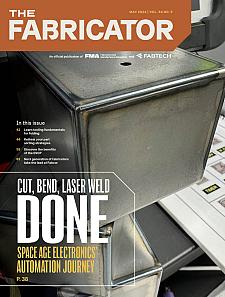
The Fabricator is North America's leading magazine for the metal forming and fabricating industry. The magazine delivers the news, technical articles, and case histories that enable fabricators to do their jobs more efficiently. The Fabricator has served the industry since 1970.
start your free subscriptionAbout the Author
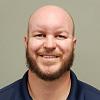
Nick Martin
2121 Industrial Park Drive SE
Wilson, NC, 27893
252-291-0925
- Stay connected from anywhere
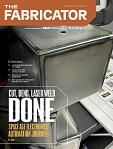
Easily access valuable industry resources now with full access to the digital edition of The Fabricator.
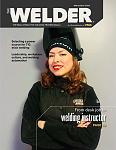
Easily access valuable industry resources now with full access to the digital edition of The Welder.
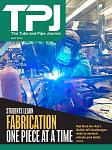
Easily access valuable industry resources now with full access to the digital edition of The Tube and Pipe Journal.
- Podcasting
- Podcast:
- The Fabricator Podcast
- Published:
- 04/16/2024
- Running Time:
- 63:29
In this episode of The Fabricator Podcast, Caleb Chamberlain, co-founder and CEO of OSH Cut, discusses his company’s...
- Trending Articles
Tips for creating sheet metal tubes with perforations
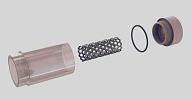
JM Steel triples capacity for solar energy projects at Pennsylvania facility
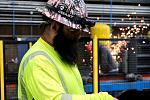
Are two heads better than one in fiber laser cutting?
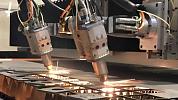
Supporting the metal fabricating industry through FMA
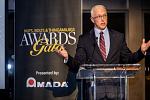
Omco Solar opens second Alabama manufacturing facility
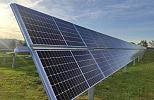
- Industry Events
16th Annual Safety Conference
- April 30 - May 1, 2024
- Elgin,
Pipe and Tube Conference
- May 21 - 22, 2024
- Omaha, NE
World-Class Roll Forming Workshop
- June 5 - 6, 2024
- Louisville, KY
Advanced Laser Application Workshop
- June 25 - 27, 2024
- Novi, MI