Editor-in-Chief
- FMA
- The Fabricator
- FABTECH
- Canadian Metalworking
Categories
- Additive Manufacturing
- Aluminum Welding
- Arc Welding
- Assembly and Joining
- Automation and Robotics
- Bending and Forming
- Consumables
- Cutting and Weld Prep
- Electric Vehicles
- En Español
- Finishing
- Hydroforming
- Laser Cutting
- Laser Welding
- Machining
- Manufacturing Software
- Materials Handling
- Metals/Materials
- Oxyfuel Cutting
- Plasma Cutting
- Power Tools
- Punching and Other Holemaking
- Roll Forming
- Safety
- Sawing
- Shearing
- Shop Management
- Testing and Measuring
- Tube and Pipe Fabrication
- Tube and Pipe Production
- Waterjet Cutting
Industry Directory
Webcasts
Podcasts
FAB 40
Advertise
Subscribe
Account Login
Search
The rapid pace of technology advancements speeds up
Right now additive manufacturing is a curiosity for many fabricators, but could it be a major manufacturing process in a few short years?
- By Dan Davis
- March 18, 2019
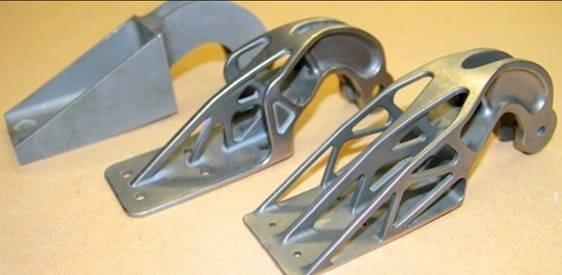
The parts to the right were 3D printed, but easily could have been made with traditional sheet metal fabricating methods.
In a meeting filled with plenty of takeaways, one moment in one session really stuck with me at The FABRICATOR’s Leadership Summit in Nashville, Tenn., March 5-7. If you aren’t thinking about additive manufacturing, you really need to change your mindset.
Jim Rogowski, vice president, technical services, and Stefan Fickenscher, sales director, TRUMPF Inc., were making a presentation on disruptive trends that could affect metal fabricators in the near future. One of the major disrupters discussed was additive manufacturing.
Now that’s not news to most in the metal fabricating world. In fact, many shops are using 3D printers to create welding fixtures, quality tools, and prototypes for sales purposes. We’ve covered some of their stories in The FABRICATOR’s sister publication The Additive Report. For instance, Boyce Technologies, Long Island City, N.Y., bought a 3D printer to find out what it could do for the company and later learned that it couldn’t live without it. The company regularly actually 3D-prints parts for its safety and communication kiosks. The printers are used for production parts a large majority of the time.
“It’s actually changing the way we think about how we are going to make production parts. We don’t know how to live without 3D anymore,” said Charles Boyce, the company’s president. (You can read more about companies such as Boyce Technologies as they investigate what 3D printing is doing for their manufacturing operations in The Additive Report. Visit www.thefabricator.com/subscription/publication to subscribe.)
Admittedly, the parts are made of plastic. They also are one-off items in many instances. But metal fabricators are all about meeting customer demands, and they should think about how additive manufacturing can help them do just that.
During his presentation, Rogowski showed a picture of three metal parts, one of which looked to be an early, traditionally made sheet metal version and two 3D-printed cousins. The 3D-printed parts were much more intricate and had features that would have been difficult and laborious to create in traditional sheet metal design.
Then it hit me: No welding is needed for that part. After hearing from other metal fabricators in attendance about how hard it is to find welders for their job openings and benefits being offered, I guess I had welding on the mind. The best way to eliminate a bottleneck in a plant, like welding, is to eliminate the process that’s at the heart of the bottleneck.
Understandably, 3D printing is not about to do that—yet. Additive manufacturing holds great promise today for on-demand expectations, such as when a customer needs a spare part for a machine, and low-volume production orders in some settings. The pace of technology advancements for additive manufacturing is not going to slow, which means new production possibilities await in the not-so-distant future.
“The rate of the progression of speed with 3D printing is astonishing,” Rogowski told the assembled metal fabricators in this hotel meeting room. “Two years ago we were using the laser metal deposition nozzle technology and the conventional deposition heads. We were trying to do a lot with that.”
The heads in question were large, like welding heads. The laser beam came down from the center and melted the powdered metal supplied through attached orifices, established the layer, and then repeated the layering until the part was created. The printer heads were not really conducive to complex rapid manufacturing because of the much larger beam diameter and the limitations of the motion system. They also were messy because the powder was not contained in an enclosed chamber, even though the actual melt area can be controlled quite well.
In the latest iteration of the laser metal fusion process, manufacturers are using a build table that has the powdered metal on it and a laser delivery method that relies on mirrors, instead of a large printer head and a gantry motion system.
“The mirror can move that beam in microseconds instead of seconds,” Rogowski said.
Things get really interesting when multiple lasers are used to expedite the build process. Parts are being made much faster than they were just two years ago.
So that led to a question that Rogowski asked the audience to think about: How fast will the 3D printing process be in five years?
“Faster” may not be an exact answer, but it’s the correct answer. That’s why everyone is bullish on the industry.
McKinsey & Co., a business intelligence firm, issued a report in 2017 stating that the direct market for additive manufacturing will reach $100 billion to $250 billion by 2025 if adoption rates continue at the same pace of recent years. That’s much larger than the figure tossed out by other industry observers only several years before—roughly $20 billion by 2020.
Additive manufacturing is a nice-to-have for any metal fabricator today. It might be a need-to-have in the coming years. Fabricators should do themselves a favor and get to know the technology before their competitors do.
subscribe now
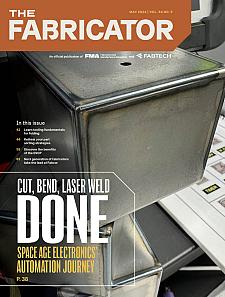
The Fabricator is North America's leading magazine for the metal forming and fabricating industry. The magazine delivers the news, technical articles, and case histories that enable fabricators to do their jobs more efficiently. The Fabricator has served the industry since 1970.
start your free subscriptionAbout the Author
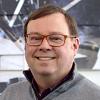
Dan Davis
2135 Point Blvd.
Elgin, IL 60123
815-227-8281
Dan Davis is editor-in-chief of The Fabricator, the industry's most widely circulated metal fabricating magazine, and its sister publications, The Tube & Pipe Journal and The Welder. He has been with the publications since April 2002.
Related Companies
- Stay connected from anywhere
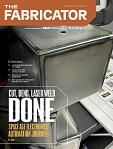
Easily access valuable industry resources now with full access to the digital edition of The Fabricator.
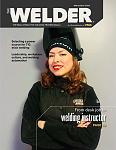
Easily access valuable industry resources now with full access to the digital edition of The Welder.
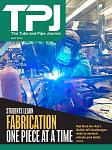
Easily access valuable industry resources now with full access to the digital edition of The Tube and Pipe Journal.
- Podcasting
- Podcast:
- The Fabricator Podcast
- Published:
- 04/16/2024
- Running Time:
- 63:29
In this episode of The Fabricator Podcast, Caleb Chamberlain, co-founder and CEO of OSH Cut, discusses his company’s...
- Trending Articles
Tips for creating sheet metal tubes with perforations
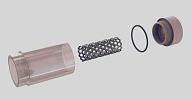
Supporting the metal fabricating industry through FMA
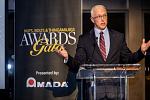
JM Steel triples capacity for solar energy projects at Pennsylvania facility
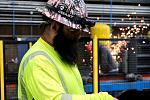
Are two heads better than one in fiber laser cutting?
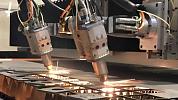
Fabricating favorite childhood memories
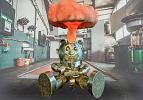
- Industry Events
16th Annual Safety Conference
- April 30 - May 1, 2024
- Elgin,
Pipe and Tube Conference
- May 21 - 22, 2024
- Omaha, NE
World-Class Roll Forming Workshop
- June 5 - 6, 2024
- Louisville, KY
Advanced Laser Application Workshop
- June 25 - 27, 2024
- Novi, MI