Editor-in-Chief
- FMA
- The Fabricator
- FABTECH
- Canadian Metalworking
Categories
- Additive Manufacturing
- Aluminum Welding
- Arc Welding
- Assembly and Joining
- Automation and Robotics
- Bending and Forming
- Consumables
- Cutting and Weld Prep
- Electric Vehicles
- En Español
- Finishing
- Hydroforming
- Laser Cutting
- Laser Welding
- Machining
- Manufacturing Software
- Materials Handling
- Metals/Materials
- Oxyfuel Cutting
- Plasma Cutting
- Power Tools
- Punching and Other Holemaking
- Roll Forming
- Safety
- Sawing
- Shearing
- Shop Management
- Testing and Measuring
- Tube and Pipe Fabrication
- Tube and Pipe Production
- Waterjet Cutting
Industry Directory
Webcasts
Podcasts
FAB 40
Advertise
Subscribe
Account Login
Search
Working overtime to fix the overtime problem
- By Dan Davis
- June 12, 2014
It’s rare nowadays to interact with a metal fabricating operation that isn’t running some kind of overtime. Sure, business may not be consistent throughout the year, which isn’t unusual for a job shop, and there may be relatively slow periods where the company hasn’t had to ask workers to put in the extra time. However, today’s lean work environments virtually guarantee that someone will be working late into the night or on a weekend to meet some deadline.
A recent study from Accenture and The Manufacturing Institute reinforces those observations on overtime. More than 70 percent of the 300 executives of large manufacturing companies (with an annual revenue of $100 million) said that they had witnessed at least a 5 percent increase in overtime costs in recent months. Thirty-two percent reported an increase of 10 percent or more. The Bureau of Labor Statistics echoes these findings; it reports that average overtime hours in the durable goods manufacturing sector have crept up to 4.6 hours per week from 4.3 a year ago.
In all honesty, the focus of the Accenture and The Manufacturing Institute study—“Out of Inventory: Skills Shortage Threatens Growth for U.S. Manufacturing”—is more focused on the reason that may be causing all of the overtime: the inability to find the right workers. But that topic has been discussed ad nauseam. It’s going to be a slow fix as manufacturers attempt to coax the next generation of workers to consider a career in manufacturing. The point that needs to be addressed is what can be done now because a consistent dose of overtime for a workforce is an easy way to overburden dependable workers and increase the chance for sloppy mistakes. (In that same survey, the manufacturing executives surveyed said that downtime increased by at least 5 percent as overtime increased because maintenance on machines was neglected.)
So what can metal fabricating companies do to avoid excessive overtime?
- Find out what skills exist within the employee ranks and then take steps to ensure more people are capable of doing multiple jobs. Drew Greenblatt, owner of Marlin Steel, Baltimore, has done just that, which allowed him to strengthen areas where he didn’t have a deep bench of knowledgeable workers.
- Establish a formalized training program to strengthen the in-house talent pool. Once the skill-set shortcomings have been identified, this is the only way to expand workers’ skills.
- Reach out to local community colleges or other educational institutions to find those new workers. This is something that a lot of metal fabricators don’t want to do, but it’s almost a necessity if they want to find the right fits for their organizations. You can read more about this here.
Most might argue that workers want the overtime, and they are probably correct. But sometimes management has to step in and do what’s right for the company and individual. A year’s worth of excessive overtime isn’t good for anyone.
subscribe now
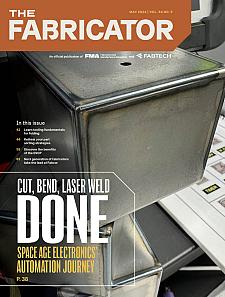
The Fabricator is North America's leading magazine for the metal forming and fabricating industry. The magazine delivers the news, technical articles, and case histories that enable fabricators to do their jobs more efficiently. The Fabricator has served the industry since 1970.
start your free subscriptionAbout the Author
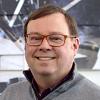
Dan Davis
2135 Point Blvd.
Elgin, IL 60123
815-227-8281
Dan Davis is editor-in-chief of The Fabricator, the industry's most widely circulated metal fabricating magazine, and its sister publications, The Tube & Pipe Journal and The Welder. He has been with the publications since April 2002.
- Stay connected from anywhere
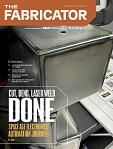
Easily access valuable industry resources now with full access to the digital edition of The Fabricator.
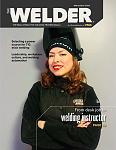
Easily access valuable industry resources now with full access to the digital edition of The Welder.
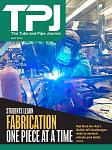
Easily access valuable industry resources now with full access to the digital edition of The Tube and Pipe Journal.
- Podcasting
- Podcast:
- The Fabricator Podcast
- Published:
- 04/16/2024
- Running Time:
- 63:29
In this episode of The Fabricator Podcast, Caleb Chamberlain, co-founder and CEO of OSH Cut, discusses his company’s...
- Trending Articles
Tips for creating sheet metal tubes with perforations
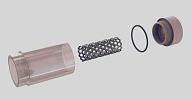
JM Steel triples capacity for solar energy projects at Pennsylvania facility
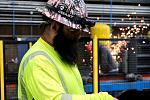
Are two heads better than one in fiber laser cutting?
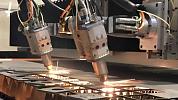
Supporting the metal fabricating industry through FMA
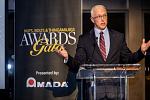
Omco Solar opens second Alabama manufacturing facility
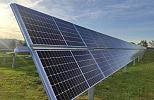
- Industry Events
16th Annual Safety Conference
- April 30 - May 1, 2024
- Elgin,
Pipe and Tube Conference
- May 21 - 22, 2024
- Omaha, NE
World-Class Roll Forming Workshop
- June 5 - 6, 2024
- Louisville, KY
Advanced Laser Application Workshop
- June 25 - 27, 2024
- Novi, MI