Editor-in-Chief
- FMA
- The Fabricator
- FABTECH
- Canadian Metalworking
Categories
- Additive Manufacturing
- Aluminum Welding
- Arc Welding
- Assembly and Joining
- Automation and Robotics
- Bending and Forming
- Consumables
- Cutting and Weld Prep
- Electric Vehicles
- En Español
- Finishing
- Hydroforming
- Laser Cutting
- Laser Welding
- Machining
- Manufacturing Software
- Materials Handling
- Metals/Materials
- Oxyfuel Cutting
- Plasma Cutting
- Power Tools
- Punching and Other Holemaking
- Roll Forming
- Safety
- Sawing
- Shearing
- Shop Management
- Testing and Measuring
- Tube and Pipe Fabrication
- Tube and Pipe Production
- Waterjet Cutting
Industry Directory
Webcasts
Podcasts
FAB 40
Advertise
Subscribe
Account Login
Search
Is the material you ordered the material you are getting to your fab shop?
To ensure the customer is getting what it is paying for, a metal fabricator needs to know just what material is being processed
- By Dan Davis
- September 9, 2022
A quality control technician checks the alloy content of incoming steel with a handheld material analyzer. Evident/Olympus Scientific Solutions
Almost all of articles in The FABRICATOR, in its sister publication, and on TheFabricator.com focus on activities that change sheet metal into parts that people are willing to pay for. Not much time is spent on the actual material, but maybe it should be. In the end, a customer is only going to be satisfied if the final fabricated part is made of the specified metal.
Visually identifying low-alloy steels like molybdenum or high-alloy steels like stainless might be easy for some in the industry, but that’s hardly something to base a quality assurance program on. Demanding customers won’t tolerate mistakes, especially if they are simple enough to address. What are most shops doing to verify the alloy content of materials entering their delivery doors? Is it something that these shops really want to leave up to their service centers to stay on top of?
Material verification becomes even more important for shops working with critical industry segments like aerospace or power generation, which involve complex work and the high quality expectations Shops wanting to pursue relationships in these highly demanding, but sometimes lucrative, manufacturing segments need to bolster their quality programs, verify materials, and provide proof to these customers.
For shops interested in expanding their quality control of incoming materials, Evident/Olympus Scientific Solutions has published a new white paper, “Alloy Verification in Metal Fabrication: From Handheld to In-Line XRF Analysis.” The whitepaper covers the use of X-ray fluorescence (XRF), a nondestructive elemental analysis technique.
XRF technology can help shops bolster their quality assurance and quality control efforts with a nominal investment. For ease of use, XRF is available in rugged, hand-held analyzers that provide alloy grades in seconds while withstanding the dust and moisture in industrial environments.
For companies involved in high-volume production, this XRF technology can be incorporated into in-line analyzers to keep up with the demands of a robust manufacturing environment.
For more information on this technology, download the white paper here.
subscribe now
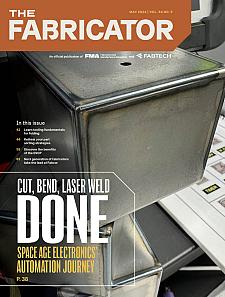
The Fabricator is North America's leading magazine for the metal forming and fabricating industry. The magazine delivers the news, technical articles, and case histories that enable fabricators to do their jobs more efficiently. The Fabricator has served the industry since 1970.
start your free subscriptionAbout the Author
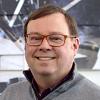
Dan Davis
2135 Point Blvd.
Elgin, IL 60123
815-227-8281
Dan Davis is editor-in-chief of The Fabricator, the industry's most widely circulated metal fabricating magazine, and its sister publications, The Tube & Pipe Journal and The Welder. He has been with the publications since April 2002.
Related Companies
- Stay connected from anywhere
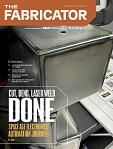
Easily access valuable industry resources now with full access to the digital edition of The Fabricator.
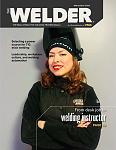
Easily access valuable industry resources now with full access to the digital edition of The Welder.
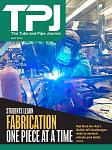
Easily access valuable industry resources now with full access to the digital edition of The Tube and Pipe Journal.
- Podcasting
- Podcast:
- The Fabricator Podcast
- Published:
- 04/16/2024
- Running Time:
- 63:29
In this episode of The Fabricator Podcast, Caleb Chamberlain, co-founder and CEO of OSH Cut, discusses his company’s...
- Trending Articles
Tips for creating sheet metal tubes with perforations
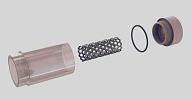
JM Steel triples capacity for solar energy projects at Pennsylvania facility
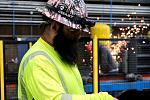
Are two heads better than one in fiber laser cutting?
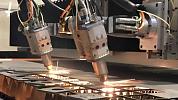
Supporting the metal fabricating industry through FMA
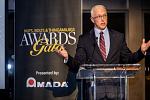
Omco Solar opens second Alabama manufacturing facility
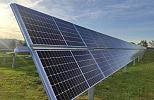
- Industry Events
16th Annual Safety Conference
- April 30 - May 1, 2024
- Elgin,
Pipe and Tube Conference
- May 21 - 22, 2024
- Omaha, NE
World-Class Roll Forming Workshop
- June 5 - 6, 2024
- Louisville, KY
Advanced Laser Application Workshop
- June 25 - 27, 2024
- Novi, MI