- FMA
- The Fabricator
- FABTECH
- Canadian Metalworking
Categories
- Additive Manufacturing
- Aluminum Welding
- Arc Welding
- Assembly and Joining
- Automation and Robotics
- Bending and Forming
- Consumables
- Cutting and Weld Prep
- Electric Vehicles
- En Español
- Finishing
- Hydroforming
- Laser Cutting
- Laser Welding
- Machining
- Manufacturing Software
- Materials Handling
- Metals/Materials
- Oxyfuel Cutting
- Plasma Cutting
- Power Tools
- Punching and Other Holemaking
- Roll Forming
- Safety
- Sawing
- Shearing
- Shop Management
- Testing and Measuring
- Tube and Pipe Fabrication
- Tube and Pipe Production
- Waterjet Cutting
Industry Directory
Webcasts
Podcasts
FAB 40
Advertise
Subscribe
Account Login
Search
Multiprocess welding machine increases contract manufacturer’s efficiency
- October 26, 2023
- News Release
- Arc Welding
Situation
Ferrum.AT Metallverarbeitung GmbH, Ennsdorf, Austria, is a medium-sized contract manufacturer for industry and commerce, producing a variety of metal components for national and international clients. Its cross-industry service and product portfolio includes outdoor facilities, roof components, facade and steel construction elements, pressure vessels, machine and wagon components, and designs for bridge construction.
Known for its flexibility and support of new product and prototype development, the company welds aluminum, steel, stainless, brass, and copper in a variety of sheet thicknesses and also offers laser cutting, rolling, and bending. Ferrum.AT begins many of its challenging manufacturing tasks with an extensive feasibility check, during which company experts evaluate the weldability of components in terms of design, material, and dimension; the suitability of welding processes; or the effect of welding sequences on component distortion.
For the company to meet component accessibility, material, and design requirements, it maintained both MIG and TIG welding systems. They took up a lot of space, and constantly switching between the two systems was inefficient. So the company began looking for an efficient, reliable multifunctional welding system to help the company save time without compromising welding quality or increasing downtime.
Resolution
As a long-standing Fronius customer, Ferrum.AT was one of the first to test the new iWave AC/DC 400i digital multiprocess welding machine for a month.
“We now have two unrivalled machines that allow us to rapidly switch between the two welding processes of MIG/MAG and TIG,” said Managing Director Hannes Holl. “At the same time, we benefit from a considerable time saving, paired with a huge increase in convenience and weld quality.”
The ultrafast SpeedNet communication between the system components combines with the high computing power of the welding machine to enable the use of new, advanced welding processes. Functions such as CycleTIG and Pulse Multi Control for MIG stabilize the arc, optimize droplet detachment, and reduce heat input while helping to ensure high deposition rates and constant penetration, the company says.
Gap tolerances are compensated for automatically, and 100% control of the weld pool is assured, even in out-of-position welding. With the help of the tacking function, the weld pool briefly oscillates at the beginning of the welding process. As a result, tacking takes place in a single step because both component edges merge without burning the edges. Very little to no temper coloration occurs at the tacking points. In addition, filler metal is not required for air gaps up to 1.5 mm.
The welds are visually perfect, eliminating spatter removal, grinding off weld reinforcements, and other time-consuming rework.
If welders want to repeat certain welding parameters, they can create jobs in the machine and subsequently retrieve up to 1,000 of them on the JobMaster welding torch. Recurring jobs can be saved as favorites, five of which can be set as so-called “easy jobs” on the welding torch.
Depending on the job, the unit recognizes when it has to change from MIG to TIG for certain applications. It automatically changes the necessary parameter settings and lowers the main current slowly and in a controlled manner for a clean weld toe.
Related Companies
subscribe now
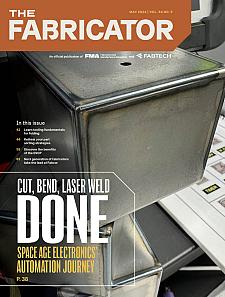
The Fabricator is North America's leading magazine for the metal forming and fabricating industry. The magazine delivers the news, technical articles, and case histories that enable fabricators to do their jobs more efficiently. The Fabricator has served the industry since 1970.
start your free subscription- Stay connected from anywhere
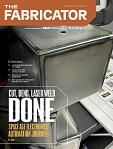
Easily access valuable industry resources now with full access to the digital edition of The Fabricator.
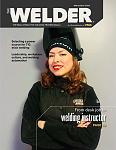
Easily access valuable industry resources now with full access to the digital edition of The Welder.
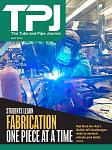
Easily access valuable industry resources now with full access to the digital edition of The Tube and Pipe Journal.
- Podcasting
- Podcast:
- The Fabricator Podcast
- Published:
- 04/16/2024
- Running Time:
- 63:29
In this episode of The Fabricator Podcast, Caleb Chamberlain, co-founder and CEO of OSH Cut, discusses his company’s...
- Trending Articles
Tips for creating sheet metal tubes with perforations
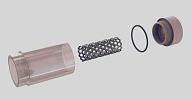
Are two heads better than one in fiber laser cutting?
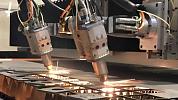
Supporting the metal fabricating industry through FMA
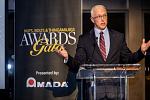
JM Steel triples capacity for solar energy projects at Pennsylvania facility
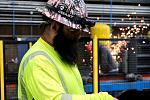
Omco Solar opens second Alabama manufacturing facility
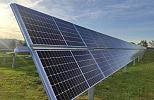
- Industry Events
16th Annual Safety Conference
- April 30 - May 1, 2024
- Elgin,
Pipe and Tube Conference
- May 21 - 22, 2024
- Omaha, NE
World-Class Roll Forming Workshop
- June 5 - 6, 2024
- Louisville, KY
Advanced Laser Application Workshop
- June 25 - 27, 2024
- Novi, MI