- FMA
- The Fabricator
- FABTECH
- Canadian Metalworking
Categories
- Additive Manufacturing
- Aluminum Welding
- Arc Welding
- Assembly and Joining
- Automation and Robotics
- Bending and Forming
- Consumables
- Cutting and Weld Prep
- Electric Vehicles
- En Español
- Finishing
- Hydroforming
- Laser Cutting
- Laser Welding
- Machining
- Manufacturing Software
- Materials Handling
- Metals/Materials
- Oxyfuel Cutting
- Plasma Cutting
- Power Tools
- Punching and Other Holemaking
- Roll Forming
- Safety
- Sawing
- Shearing
- Shop Management
- Testing and Measuring
- Tube and Pipe Fabrication
- Tube and Pipe Production
- Waterjet Cutting
Industry Directory
Webcasts
Podcasts
FAB 40
Advertise
Subscribe
Account Login
Search
Automated SAW system speeds up production of large-diameter shells
- August 5, 2020
- News Release
- Assembly and Joining
Situation
Custom Steel Fabricators Inc. was established in the early 1970s in Columbia, Tenn., to fabricate stainless steel plate and nickel alloys for industrial markets. Today, with 40 employees in two workshops covering about 50,000 sq. ft., the manufacturer processes 300 series stainless, duplex steels, 6% moly grades, and most nickel alloys for such industries as power, chemical, and cement.
“As the scope of our work and our customer base grew, one of the challenges we faced in our fabrication process was the fitting and welding of large-diameter shells,” explained Tony Sciotto, president. The company was using turning rolls and a welding manipulator with submerged arc welding (SAW) to produce the shells, but as the requested diameters continued to grow, the system proved inadequate.
While manual fitting was accurate, it was also slow. The company needed to improve fit-up speed while maintaining accuracy on the large cylinders.
Resolution
To help ensure better fitting and welding of the shells, the manufacturer recently purchased equipment from Pemamek: a Pema TW5000-25 assembly station with side-support arms and integration to a Pema MD 4.5×5 column and boom with a single SAW head.
The automated system has made fabrication of the large-diameter shells faster and more efficient. “By using the side-support arms, we are now able to support the cylinder as we fit the joint and also throughout the welding process. No more manual fit-ups,” Sciotto said.
It also has improved fit-up quality on the company’s current project: a 1/2-in.-thick alloy 2205 duplex stainless cylinder, 156 in. in diameter.
“I believe we will be seeing even higher results as time passes; we are improving daily and learning the right methods to utilize Pema machinery,” Sciotto concluded.
Pemamek pemamek.com/us
subscribe now
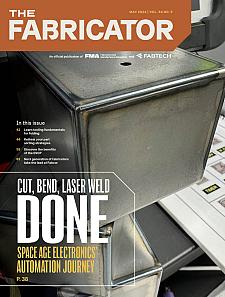
The Fabricator is North America's leading magazine for the metal forming and fabricating industry. The magazine delivers the news, technical articles, and case histories that enable fabricators to do their jobs more efficiently. The Fabricator has served the industry since 1970.
start your free subscription- Stay connected from anywhere
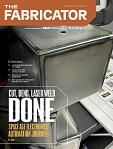
Easily access valuable industry resources now with full access to the digital edition of The Fabricator.
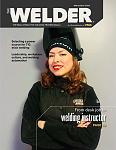
Easily access valuable industry resources now with full access to the digital edition of The Welder.
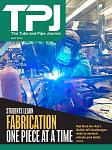
Easily access valuable industry resources now with full access to the digital edition of The Tube and Pipe Journal.
- Podcasting
- Podcast:
- The Fabricator Podcast
- Published:
- 04/16/2024
- Running Time:
- 63:29
In this episode of The Fabricator Podcast, Caleb Chamberlain, co-founder and CEO of OSH Cut, discusses his company’s...
- Trending Articles
Tips for creating sheet metal tubes with perforations
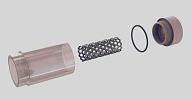
Supporting the metal fabricating industry through FMA
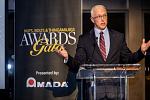
JM Steel triples capacity for solar energy projects at Pennsylvania facility
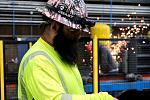
Are two heads better than one in fiber laser cutting?
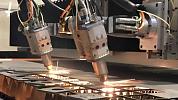
Fabricating favorite childhood memories
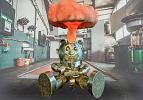
- Industry Events
16th Annual Safety Conference
- April 30 - May 1, 2024
- Elgin,
Pipe and Tube Conference
- May 21 - 22, 2024
- Omaha, NE
World-Class Roll Forming Workshop
- June 5 - 6, 2024
- Louisville, KY
Advanced Laser Application Workshop
- June 25 - 27, 2024
- Novi, MI