- FMA
- The Fabricator
- FABTECH
- Canadian Metalworking
Categories
- Additive Manufacturing
- Aluminum Welding
- Arc Welding
- Assembly and Joining
- Automation and Robotics
- Bending and Forming
- Consumables
- Cutting and Weld Prep
- Electric Vehicles
- En Español
- Finishing
- Hydroforming
- Laser Cutting
- Laser Welding
- Machining
- Manufacturing Software
- Materials Handling
- Metals/Materials
- Oxyfuel Cutting
- Plasma Cutting
- Power Tools
- Punching and Other Holemaking
- Roll Forming
- Safety
- Sawing
- Shearing
- Shop Management
- Testing and Measuring
- Tube and Pipe Fabrication
- Tube and Pipe Production
- Waterjet Cutting
Industry Directory
Webcasts
Podcasts
FAB 40
Advertise
Subscribe
Account Login
Search
Stamper reduces scrap, increases die life and part quality with servo presses
- January 19, 2023
- News Release
- Bending and Forming
Situation
Small Parts Inc., a precision metal stampings provider in Logansport, Ind., was experiencing some part quality challenges when using its mechanical presses.
Among other issues, the company was getting excessive scrap from an automotive progressive die, and the sharp edge profiles on a nonautomotive die were breaking or wearing down multiple times while stamping an order.
Resolution
Small Parts purchased two unitized-frame, two-point, direct-drive model DSF-N2 servo presses from AIDA-America. The stamper has quickly realized several benefits on jobs moved from its mechanical presses to its new servo presses, including increased strokes per minute and uptime per run.
After modifying the existing automotive progressive die to run on the new 110-ton servo press, the stamper achieved burr reduction and less part distortion, which it attributes to complete programmability throughout the entire stroke of the servo press, decreasing parts failure post-sorting. Moving this die from a mechanical to a servo press also shortened the feed length. These combined improvements resulted in a scrap reduction of approximately 30% on this automotive part.
Switching the nonautomotive die to the new press has already reduced die maintenance by 50%, which is expected to increase to a 60% to 70% reduction when further tooling improvements are complete.
With another existing automotive die, making new cutting inserts to reduce the cutting clearance immediately yielded a 55% increase in die life when moved from a mechanical press to the new servo press.
On another job moved to one of the servo presses purely for capacity gain, the company instantly stamped better-looking parts but noticed the angles were overformed because the servo press allowed operators to form the parts so much better than the mechanical press did with the existing die. Adjusting the form insert angles resulted in the best-looking part the stamper had ever produced and eliminated the multiple hits previously required in the mechanical press to compensate for springback.
Furthermore, seeing these positive results on the two servo presses has given the company confidence to quote servo press jobs that would have been troublesome to stamp on mechanical presses.
Related Companies
subscribe now
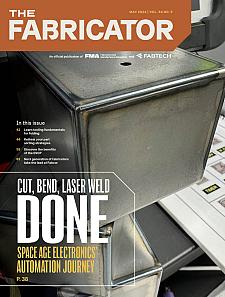
The Fabricator is North America's leading magazine for the metal forming and fabricating industry. The magazine delivers the news, technical articles, and case histories that enable fabricators to do their jobs more efficiently. The Fabricator has served the industry since 1970.
start your free subscription- Stay connected from anywhere
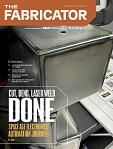
Easily access valuable industry resources now with full access to the digital edition of The Fabricator.
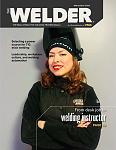
Easily access valuable industry resources now with full access to the digital edition of The Welder.
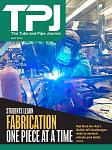
Easily access valuable industry resources now with full access to the digital edition of The Tube and Pipe Journal.
- Podcasting
- Podcast:
- The Fabricator Podcast
- Published:
- 04/16/2024
- Running Time:
- 63:29
In this episode of The Fabricator Podcast, Caleb Chamberlain, co-founder and CEO of OSH Cut, discusses his company’s...
- Trending Articles
Tips for creating sheet metal tubes with perforations
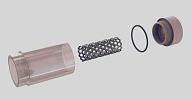
JM Steel triples capacity for solar energy projects at Pennsylvania facility
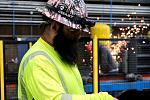
Are two heads better than one in fiber laser cutting?
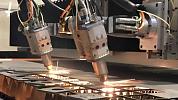
Supporting the metal fabricating industry through FMA
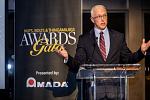
Omco Solar opens second Alabama manufacturing facility
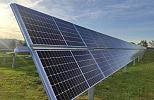
- Industry Events
16th Annual Safety Conference
- April 30 - May 1, 2024
- Elgin,
Pipe and Tube Conference
- May 21 - 22, 2024
- Omaha, NE
World-Class Roll Forming Workshop
- June 5 - 6, 2024
- Louisville, KY
Advanced Laser Application Workshop
- June 25 - 27, 2024
- Novi, MI