- FMA
- The Fabricator
- FABTECH
- Canadian Metalworking
Categories
- Additive Manufacturing
- Aluminum Welding
- Arc Welding
- Assembly and Joining
- Automation and Robotics
- Bending and Forming
- Consumables
- Cutting and Weld Prep
- Electric Vehicles
- En Español
- Finishing
- Hydroforming
- Laser Cutting
- Laser Welding
- Machining
- Manufacturing Software
- Materials Handling
- Metals/Materials
- Oxyfuel Cutting
- Plasma Cutting
- Power Tools
- Punching and Other Holemaking
- Roll Forming
- Safety
- Sawing
- Shearing
- Shop Management
- Testing and Measuring
- Tube and Pipe Fabrication
- Tube and Pipe Production
- Waterjet Cutting
Industry Directory
Webcasts
Podcasts
FAB 40
Advertise
Subscribe
Account Login
Search
Tooling system takes fabricator from setup to bending in 10 seconds
- January 26, 2024
- News Release
- Bending and Forming
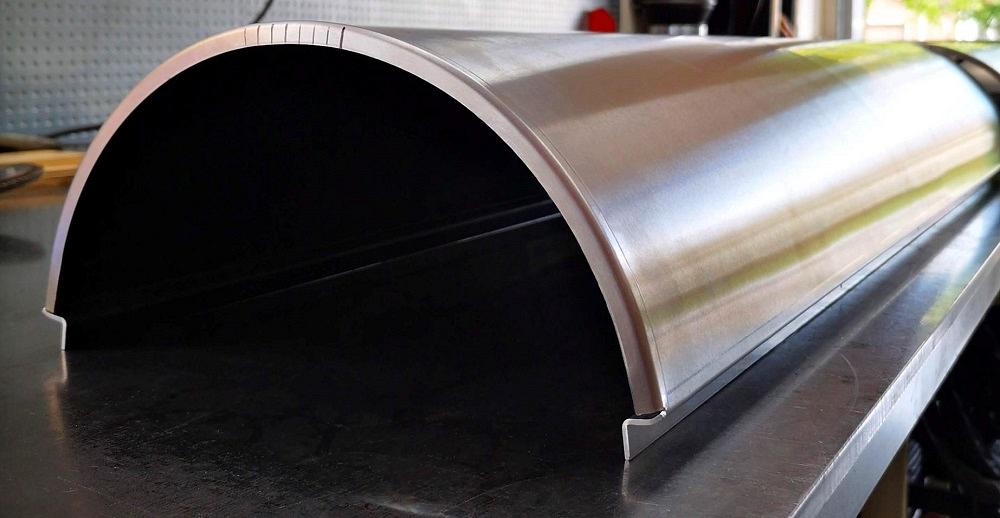
This 16-ga. clamshell column flashing to cover a galvanized structural column was formed on a press brake to continue the radius right to the connection flange.
Situation
Bilan Metalworks is a fabricator of small to medium design-build projects for the commercial, industrial, and residential industries. The Pickering, Ont., company focuses on the design and manufacture of quick-turnaround, turnkey luxury products that are both unique and highly functional.
According to President/Owner Chris Bilan, “On every job, we are challenged to be profitable in the face of low-volume projects and frequent, nonstop setups. That includes requests from contractors with an emergency need for a specialized component to complete a job.
“A dozen components is a big run for us,” Bilan continued, “so … we’re changing setups constantly. In addition, our press brake is only 4 ft. long with at times three different setups for a typical job. With conventional tooling, it’s practically impossible to seat this many sets of tooling at once without crashing.”
As a result, Bilan is constantly looking for better ways to fabricate quality components.
Resolution
When Peter Visser, Mate Precision Technologies’ regional sales manager, introduced the company’s American Precision Style press brake tooling with Maglock during a visit, it proved to be the right fit for Bilan.
With no buttons, springs, or pins that can fail, the patented system uses rare-earth magnets to hold the punches in place, making it possible to install even large tools in the forward or rearward direction. Most important, while the system does not replace standard press brake clamping systems (the holder clamping system must be engaged when a brake is in operation), the design eliminates safety concerns over a punch falling out of the upper holder and possibly damaging the tool or harming the operator.
The rare-earth magnets quickly attach and seat the punch to the holder with no separation between the surfaces. Since there is no separation, there’s no need to seat the tooling before use, a significant time saver. Bilan reports that setups have been reduced from 10 minutes to 10 seconds. For a shop with two shifts and three setups per shift, that saves 59 minutes of labor per day, or 247 hours of labor per year (based on 252 workdays).
When he switched to this system, Bilan set aside thousands of dollars’ worth of conventional press brake tooling—a difficult decision for any manufacturer, but especially so for a startup company with limited cash flow.
“I bought the Mate Maglock tooling a couple of months after the machine. I’d already invested maybe $40,000 in competitive tooling brands, but I won’t use any of it now unless there’s no other choice. Simply put, the Maglock system offers huge advantages. It’s been a real game-changer for Bilan Metalworks.”
Related Companies
subscribe now
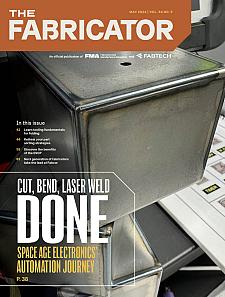
The Fabricator is North America's leading magazine for the metal forming and fabricating industry. The magazine delivers the news, technical articles, and case histories that enable fabricators to do their jobs more efficiently. The Fabricator has served the industry since 1970.
start your free subscription- Stay connected from anywhere
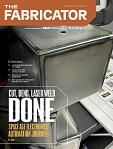
Easily access valuable industry resources now with full access to the digital edition of The Fabricator.
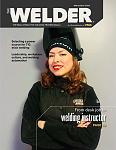
Easily access valuable industry resources now with full access to the digital edition of The Welder.
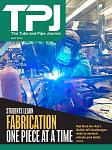
Easily access valuable industry resources now with full access to the digital edition of The Tube and Pipe Journal.
- Podcasting
- Podcast:
- The Fabricator Podcast
- Published:
- 04/16/2024
- Running Time:
- 63:29
In this episode of The Fabricator Podcast, Caleb Chamberlain, co-founder and CEO of OSH Cut, discusses his company’s...
- Trending Articles
Tips for creating sheet metal tubes with perforations
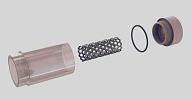
Are two heads better than one in fiber laser cutting?
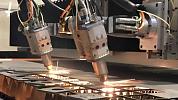
Supporting the metal fabricating industry through FMA
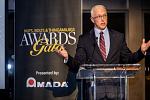
JM Steel triples capacity for solar energy projects at Pennsylvania facility
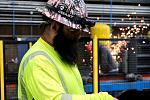
Omco Solar opens second Alabama manufacturing facility
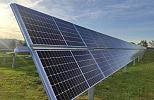
- Industry Events
16th Annual Safety Conference
- April 30 - May 1, 2024
- Elgin,
Pipe and Tube Conference
- May 21 - 22, 2024
- Omaha, NE
World-Class Roll Forming Workshop
- June 5 - 6, 2024
- Louisville, KY
Advanced Laser Application Workshop
- June 25 - 27, 2024
- Novi, MI