- FMA
- The Fabricator
- FABTECH
- Canadian Metalworking
Categories
- Additive Manufacturing
- Aluminum Welding
- Arc Welding
- Assembly and Joining
- Automation and Robotics
- Bending and Forming
- Consumables
- Cutting and Weld Prep
- Electric Vehicles
- En Español
- Finishing
- Hydroforming
- Laser Cutting
- Laser Welding
- Machining
- Manufacturing Software
- Materials Handling
- Metals/Materials
- Oxyfuel Cutting
- Plasma Cutting
- Power Tools
- Punching and Other Holemaking
- Roll Forming
- Safety
- Sawing
- Shearing
- Shop Management
- Testing and Measuring
- Tube and Pipe Fabrication
- Tube and Pipe Production
- Waterjet Cutting
Industry Directory
Webcasts
Podcasts
FAB 40
Advertise
Subscribe
Account Login
Search
CAD/CAM, nesting software enhances plasma, oxyfuel system capabilities
- December 29, 2020
- News Release
- Manufacturing Software
Situation
Kerf Developments, Rochdale, U.K., has been building plasma, oxyfuel, and waterjet cutting machines since 2002. The company originally started as a service-based organization repairing and upgrading profile cutting machinery. The experiences it gained working on a variety of equipment formed the basis of its current machine offering.
In addition to offering a standard line of profile cutting machines, Kerf develops customized machinery for specific applications, designing and building machines up to 4 m wide and any length, with a combination of plasma and oxyfuel heads. The smallest machine the company has supplied has a working area of 2.5 by 1.25 m; the largest machine’s working area is 40 by 4 m with multiple bridges. Plasma systems can cut material thicknesses up to 90 mm, while oxyfuel handles up to 150 mm.
As part of its continued development, the company needed to evaluate the capabilities of various CAD/CAM and nesting systems, as this was becoming an ever-increasing requirement from its customers.
Resolution
Following evaluation of several systems, the company chose Lantek Expert, and the training began.
“All our field service engineers have a copy of Lantek Expert software as part of their toolbox so that they can provide an instant response to any queries,” said Dan Taylor, Kerf’s managing director. “Lantek provides regular and valuable updates to the software and are always on hand to provide online support to fine-tune systems to work in line with our customers’ needs.”
For offline programming of the cutting machines, users can import CAD data directly into the software system, nest parts on the material to optimize usage, and automatically create the cutting path. This keeps the machine running to help achieve high productivity levels and short delivery times, the company reports.
As part of the collaboration, Lantek has worked closely with the Kerf engineering team to perfect its UltraSharp technology, which delivers high-quality parts with a square edge, better-quality edges, and 1-to-1 hole sizes (for example, a 5-mm hole in 5-mm material). This capability lets the operator use plasma rather than laser to manufacture parts, which is especially effective for thicker components.
“The UltraSharp technology involves internally enhanced software protocols, accelerating and decelerating the torch dynamics on tight contours and holes; controlling the power, gas pressure, and flow, amongst other things; and also automatically selecting special lead-in and lead-out configurations,” explained Taylor. “The result is a constant and true arc with no lag between the top and bottom of the material being cut. All the parameters required to achieve this are built into our technology tables, making it easy to achieve high-quality components direct from the CAD data.”
Related Companies
subscribe now
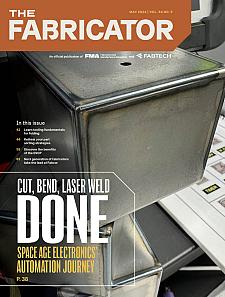
The Fabricator is North America's leading magazine for the metal forming and fabricating industry. The magazine delivers the news, technical articles, and case histories that enable fabricators to do their jobs more efficiently. The Fabricator has served the industry since 1970.
start your free subscription- Stay connected from anywhere
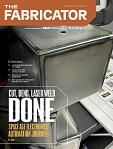
Easily access valuable industry resources now with full access to the digital edition of The Fabricator.
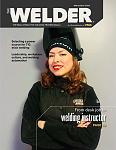
Easily access valuable industry resources now with full access to the digital edition of The Welder.
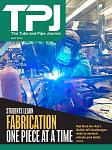
Easily access valuable industry resources now with full access to the digital edition of The Tube and Pipe Journal.
- Podcasting
- Podcast:
- The Fabricator Podcast
- Published:
- 04/16/2024
- Running Time:
- 63:29
In this episode of The Fabricator Podcast, Caleb Chamberlain, co-founder and CEO of OSH Cut, discusses his company’s...
- Trending Articles
Tips for creating sheet metal tubes with perforations
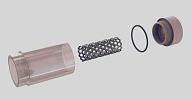
Are two heads better than one in fiber laser cutting?
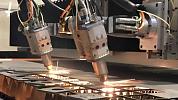
Supporting the metal fabricating industry through FMA
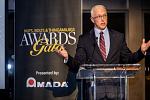
JM Steel triples capacity for solar energy projects at Pennsylvania facility
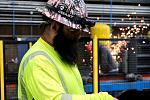
Omco Solar opens second Alabama manufacturing facility
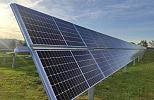
- Industry Events
16th Annual Safety Conference
- April 30 - May 1, 2024
- Elgin,
Pipe and Tube Conference
- May 21 - 22, 2024
- Omaha, NE
World-Class Roll Forming Workshop
- June 5 - 6, 2024
- Louisville, KY
Advanced Laser Application Workshop
- June 25 - 27, 2024
- Novi, MI