- FMA
- The Fabricator
- FABTECH
- Canadian Metalworking
Categories
- Additive Manufacturing
- Aluminum Welding
- Arc Welding
- Assembly and Joining
- Automation and Robotics
- Bending and Forming
- Consumables
- Cutting and Weld Prep
- Electric Vehicles
- En Español
- Finishing
- Hydroforming
- Laser Cutting
- Laser Welding
- Machining
- Manufacturing Software
- Materials Handling
- Metals/Materials
- Oxyfuel Cutting
- Plasma Cutting
- Power Tools
- Punching and Other Holemaking
- Roll Forming
- Safety
- Sawing
- Shearing
- Shop Management
- Testing and Measuring
- Tube and Pipe Fabrication
- Tube and Pipe Production
- Waterjet Cutting
Industry Directory
Webcasts
Podcasts
FAB 40
Advertise
Subscribe
Account Login
Search
ARKU formally welcomes fabricators to new facility
- May 29, 2022
- News Release
- Finishing
ARKU’s FlatMaster leveler series has an easy-to-extract and -retract cassette feature to give operators quick access to the leveling and backup rollers.
ARKU Inc., a manufacturer of roller levelers, press feeding equipment, and deburring and edge-rounding machinery, moved into its new facility in Cincinnati two years ago, but the pandemic pushed back plans for a formal open house event recognizing the move. On May 23-26, that changed as ARKU welcomed metal fabricators and manufacturers to its Leveling + Deburring InfoDays at the new building.
The new office and shop were modeled after the company’s headquarters in Baden-Baden, Germany, according to Denis Weinfurtner, marketing for ARKU. The 15,000-sq-ft. office space has open work areas for informal collaboration and conference areas for more formal business discussions and virtual meetings. The 25,000-sq.-ft. shop area has several ARKU leveling and deburring machines, where InfoDays visitors could see parts being processed.
The ARKU shop is unique in that it’s a production facility as well as a showroom for the company’s equipment. Customers from all over North America send parts, sheets, and plates to be leveled. Weinfurtner said that up to 300,000 lbs. of material are being processed each week.
Who exactly is sending parts to be leveled? The customer portfolio is wide-ranging. Service centers receive sheets from the mill that are not flat, and the mills won’t take them back. Manufacturers’ flame-cut parts that are then warped, and the companies don’t want to scrap the parts. Shops that provide perforated sheet often see their final products curled because of the punching process, and they need help getting the sheets flat again. Those are just a few of the companies looking for flat and stress-relieved materials.
The shop has the latest ARKU equipment. One such machine was The FlatMaster 88, a machine that can level material from 0.04 to 1.1 in. and up to 79 in. wide. Visitors got to see the machine’s cassette feature for the leveling rollers. With the push of a button, the cassettes can be pulled out and removed easily for cleaning and maintenance.
The EdgeBreaker 5000 also was processing parts. Visitors got to see the machine’s powerful pins remove the slag from plasma- and oxyfuel-cut parts.
The EdgeBreaker 6000 was the newest machine on display in the shop. This machine is designed to deburr, edge-round, and surface finish in a single pass. It can process materials as small as 2 by 2 in. thanks to a vacuum belt.
Recognizing that a lot of metal fabricating companies have inexperienced machine operators on the shop floor, ARKU engineers have created software enhancements that take the guesswork out of tool selection and eliminate the need to tweak performance parameters. Machine operators enter the part properties and the desired processing result, and a programming wizard handles the machine set up and automatically adjusts to achieve the specified results at the best possible processing speed.
Fabricators interested in learning more about ARKU’s machines and who couldn’t make it to the open house can contact the company directly to arrange a visit or reach out to ARKU representatives at FABTECH, Nov. 8-11, in Atlanta.
—Dan Davis, Editor-in-Chief
Related Companies
subscribe now
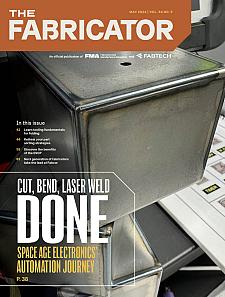
The Fabricator is North America's leading magazine for the metal forming and fabricating industry. The magazine delivers the news, technical articles, and case histories that enable fabricators to do their jobs more efficiently. The Fabricator has served the industry since 1970.
start your free subscription- Stay connected from anywhere
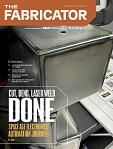
Easily access valuable industry resources now with full access to the digital edition of The Fabricator.
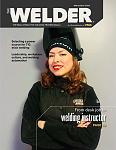
Easily access valuable industry resources now with full access to the digital edition of The Welder.
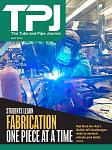
Easily access valuable industry resources now with full access to the digital edition of The Tube and Pipe Journal.
- Podcasting
- Podcast:
- The Fabricator Podcast
- Published:
- 04/16/2024
- Running Time:
- 63:29
In this episode of The Fabricator Podcast, Caleb Chamberlain, co-founder and CEO of OSH Cut, discusses his company’s...
- Trending Articles
Tips for creating sheet metal tubes with perforations
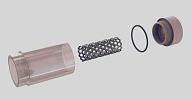
JM Steel triples capacity for solar energy projects at Pennsylvania facility
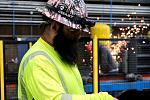
Are two heads better than one in fiber laser cutting?
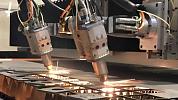
Supporting the metal fabricating industry through FMA
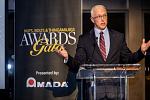
Omco Solar opens second Alabama manufacturing facility
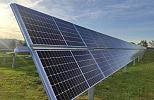
- Industry Events
16th Annual Safety Conference
- April 30 - May 1, 2024
- Elgin,
Pipe and Tube Conference
- May 21 - 22, 2024
- Omaha, NE
World-Class Roll Forming Workshop
- June 5 - 6, 2024
- Louisville, KY
Advanced Laser Application Workshop
- June 25 - 27, 2024
- Novi, MI