- FMA
- The Fabricator
- FABTECH
- Canadian Metalworking
Categories
- Additive Manufacturing
- Aluminum Welding
- Arc Welding
- Assembly and Joining
- Automation and Robotics
- Bending and Forming
- Consumables
- Cutting and Weld Prep
- Electric Vehicles
- En Español
- Finishing
- Hydroforming
- Laser Cutting
- Laser Welding
- Machining
- Manufacturing Software
- Materials Handling
- Metals/Materials
- Oxyfuel Cutting
- Plasma Cutting
- Power Tools
- Punching and Other Holemaking
- Roll Forming
- Safety
- Sawing
- Shearing
- Shop Management
- Testing and Measuring
- Tube and Pipe Fabrication
- Tube and Pipe Production
- Waterjet Cutting
Industry Directory
Webcasts
Podcasts
FAB 40
Advertise
Subscribe
Account Login
Search
Automated deburring/finishing system brings efficiency to laser cutting shop
- November 22, 2023
- News Release
- Finishing
Established in 2018 in Las Vegas, Precision Tube Laser provides on-demand laser cutting and forming of a variety of metals. Offering laser cutting of tube up to 6.625 in. OD and 5 by 5 in. square, the company didn’t receive many requests for deburring services, so it performed the task manually as needed. While the idea of automated deburring was mentioned around the shop, there didn’t seem to be much value in investing in the equipment.
After about 1-1/2 years in business, the company added flat metal processing, handling sheet up to 6 by 12 ft. and 0.75 in. thick.
“And then when we moved into this new building and really started pumping out a lot of flat parts, [deburring] came up even more in conversation,” said owner Jordan Yost. “I can’t have two or three people doing these parts manually and think we’re going to be making money off it or that it’s a legitimate way to do it as far as consistency and reliability.”
In addition, some bigger customers were pushing Yost for automated deburring as an added service. “We knew we’d get five or six really large companies that would use this process all the time,” he said.
Yost began looking into adding a deburring machine in early 2022, and he visited ARKU to see its automated systems in action. They discussed types of materials to be processed, and thicknesses, and the fact that Precision Tube Laser doesn’t make its own parts.
“We make others’ parts—customer parts—right.”
ResolutionAfter seeing all the equipment in action, Yost chose the EdgeBreaker 6000 deburring machine, designed for complete processing of materials after punching and laser cutting. Its grinding belt, rotary brushes, and finishing belt perform deburring, uniform edge rounding, and surface finishing in a single pass. Yost cites several reasons for settling on the 6000.
“For one, not all of my customers require a dual-side process. Some truly just want the burr removed,” he said.
“Second was being able to see the process as it happens,” he explained. “I can watch [it], and if I don't like something, I can make a change on the fly because I’m seeing the result as it’s actually happening.
“The final point, going along with our social media side, is that it's a show. When you walk into the shop and you see that thing whipping around, you immediately think, “What is that?’” he explained. “And when you’re watching, it’s hard to process what's going on. You’re thinking, ‘How many people would that take? And what’s really involved in this?’”
The EdgeBreaker 6000 takes the part (left) and deburrs, edge rounds, and provides a specified surface finish on it (right) in a single pass.
The deburring system has a minimum thickness capability of 0.04 in., depending on the belt. Precision Tube Laser stays around 0.60 to 0.75 in. And a year after it acquired the machine, about 85% of its customer base now accepts some part of this automated deburring process.
“It’s the easiest add-on service we’ve ever put through the shop. When we quote, we tell you what the deburring price is right off the bat, so it allows you to see what it’s going to cost to have your part deburred or prepped, but it also opens up some dialogue with customers about the different processes. It gives us a chance to educate them about the piece of equipment that we brought in. “
And even faced with the speed of the shop’s 12-kW TRUMPF 7030 laser cutting system, the deburring machine keeps up.
“We ran a job of 4- by 8-ft. aluminum panels that had a bunch of holes, and [the laser system] ran 184 panels in 28 hours. And these panels were going through the ARKU to be grained. Not only did it keep up with the feed rate, but [the deburring machine was] running two full panels to every one that was coming off the [laser system] … on a single pass and getting a perfect result every time.”
Yost says he’s shocked by how many customers are accepting the new machine and service. He estimates that in another five months, the machine will have generated enough income to pay for itself.
“For me, the money is a drop in the bucket,” he said. “And what it does to the service that you're bringing and the quality of parts that you're producing far outweighs its expense.”
Related Companies
subscribe now
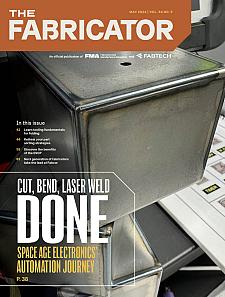
The Fabricator is North America's leading magazine for the metal forming and fabricating industry. The magazine delivers the news, technical articles, and case histories that enable fabricators to do their jobs more efficiently. The Fabricator has served the industry since 1970.
start your free subscription- Stay connected from anywhere
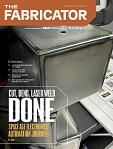
Easily access valuable industry resources now with full access to the digital edition of The Fabricator.
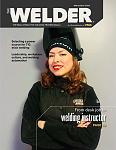
Easily access valuable industry resources now with full access to the digital edition of The Welder.
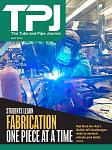
Easily access valuable industry resources now with full access to the digital edition of The Tube and Pipe Journal.
- Podcasting
- Podcast:
- The Fabricator Podcast
- Published:
- 04/16/2024
- Running Time:
- 63:29
In this episode of The Fabricator Podcast, Caleb Chamberlain, co-founder and CEO of OSH Cut, discusses his company’s...
- Trending Articles
Tips for creating sheet metal tubes with perforations
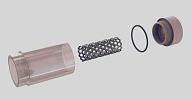
Are two heads better than one in fiber laser cutting?
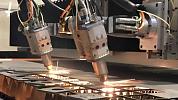
Supporting the metal fabricating industry through FMA
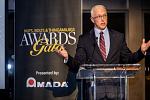
JM Steel triples capacity for solar energy projects at Pennsylvania facility
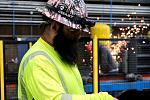
Omco Solar opens second Alabama manufacturing facility
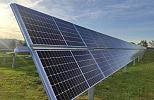
- Industry Events
16th Annual Safety Conference
- April 30 - May 1, 2024
- Elgin,
Pipe and Tube Conference
- May 21 - 22, 2024
- Omaha, NE
World-Class Roll Forming Workshop
- June 5 - 6, 2024
- Louisville, KY
Advanced Laser Application Workshop
- June 25 - 27, 2024
- Novi, MI