- FMA
- The Fabricator
- FABTECH
- Canadian Metalworking
Categories
- Additive Manufacturing
- Aluminum Welding
- Arc Welding
- Assembly and Joining
- Automation and Robotics
- Bending and Forming
- Consumables
- Cutting and Weld Prep
- Electric Vehicles
- En Español
- Finishing
- Hydroforming
- Laser Cutting
- Laser Welding
- Machining
- Manufacturing Software
- Materials Handling
- Metals/Materials
- Oxyfuel Cutting
- Plasma Cutting
- Power Tools
- Punching and Other Holemaking
- Roll Forming
- Safety
- Sawing
- Shearing
- Shop Management
- Testing and Measuring
- Tube and Pipe Fabrication
- Tube and Pipe Production
- Waterjet Cutting
Industry Directory
Webcasts
Podcasts
FAB 40
Advertise
Subscribe
Account Login
Search
Blast room helps pipe fabrication shop handle increased product sizes
- August 30, 2023
- News Release
- Finishing
Situation
Based in Williamsport, Pa., NuWeld offers a variety of specialized welding, engineering, and fabrication services to the nuclear, natural gas, and power industries worldwide.
Part of the company’s operation includes full-service pipe, structural, and custom steel shop fabrication and field installation. A significant segment of the company’s business is fabricating piping for a gas industry customer, a process that involves abrasive blasting to prepare the piping for painting or coating before installation.
However, the piping, which used to be no more than 1 to 2 in. dia., has increased to as much as 24 in. over the years. This increased diameter has highlighted the deficiencies in the company’s abrasive blasting operation:
- The old blasting operation was a tarped-off area too small to accommodate the larger diameters.
- The blast media was contained in 3-cu.-ft. blast pots that had to be filled every eight minutes.
- To fill the pots, operators had to clean up all the blast media from the floor, as the material was not being reclaimed.
Resolution
Knowing it needed a complete overhaul of its abrasive blasting setup, NuWeld acquired a new blast room from Titan Abrasive Systems. At 20 ft. wide by 15 ft. high by 50 ft. long, the room accepts the 24-in. piping with ease while allowing operators ample room for unrestricted movement. The 4-ft.-wide by 50-ft.-long overhead crane slot with pneumatic door allows loading/unloading with the company’s existing overhead cranes.
The blast room also includes an efficient reclaim system, which uses an auger system with bucket elevator to recover blast media and feed it back into the blasting tank. Not only has this eliminated manual reclamation and bucket filling, it facilitated a switch in blast media that the company had been considering.
“We had been looking to switch to steel grit to blast our piping, but it’s extremely expensive,” said Noah Barrett, a NuWeld maintenance technician. “The problem is, if you don’t have a recovery process, it’s a highly impractical blasting media. With our previous blasting material, we were buying pallet after pallet of bags every time we began a new job. With the addition of the reclaim system to the blast room, it’s now economically feasible for us to use the steel grit. It not only cleans more quickly, but it also produces a better profile on our piping, creates better paint adhesion, and, ultimately, a better-quality product. We made the switch to steel grit and have not looked back.”
With the new reclamation system, operators can blast continuously for two hours before having to push the grit back into the auger. This has boosted work output and resulted in cost savings, since the initial amount of grit that was purchased when the blast room was installed is still in use.
Not only has the blast room made the finishing of gas production units easier, but it also allows the company to fabricate pressure vessels, water tanks, and burner units—all of which it is certified to handle but has never had the room to produce. The company now blasts 40-ft. frac tanks; 30-ton, 8-ft.-dia. pressure vessels; and wire spool stands more than 20 ft. long.
Dust collectors that came with the system keep dust to a minimum to protect workers from airborne particulates and maximize visibility.
Related Companies
subscribe now
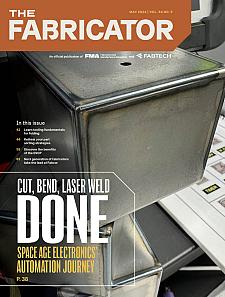
The Fabricator is North America's leading magazine for the metal forming and fabricating industry. The magazine delivers the news, technical articles, and case histories that enable fabricators to do their jobs more efficiently. The Fabricator has served the industry since 1970.
start your free subscription- Stay connected from anywhere
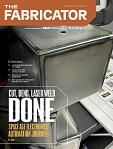
Easily access valuable industry resources now with full access to the digital edition of The Fabricator.
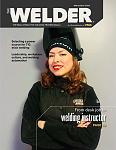
Easily access valuable industry resources now with full access to the digital edition of The Welder.
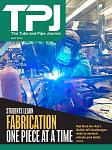
Easily access valuable industry resources now with full access to the digital edition of The Tube and Pipe Journal.
- Podcasting
- Podcast:
- The Fabricator Podcast
- Published:
- 04/16/2024
- Running Time:
- 63:29
In this episode of The Fabricator Podcast, Caleb Chamberlain, co-founder and CEO of OSH Cut, discusses his company’s...
- Trending Articles
Tips for creating sheet metal tubes with perforations
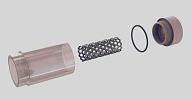
JM Steel triples capacity for solar energy projects at Pennsylvania facility
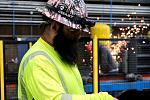
Are two heads better than one in fiber laser cutting?
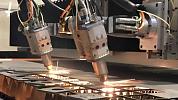
Supporting the metal fabricating industry through FMA
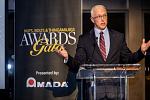
Omco Solar opens second Alabama manufacturing facility
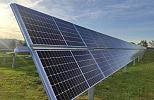
- Industry Events
16th Annual Safety Conference
- April 30 - May 1, 2024
- Elgin,
Pipe and Tube Conference
- May 21 - 22, 2024
- Omaha, NE
World-Class Roll Forming Workshop
- June 5 - 6, 2024
- Louisville, KY
Advanced Laser Application Workshop
- June 25 - 27, 2024
- Novi, MI