- FMA
- The Fabricator
- FABTECH
- Canadian Metalworking
Categories
- Additive Manufacturing
- Aluminum Welding
- Arc Welding
- Assembly and Joining
- Automation and Robotics
- Bending and Forming
- Consumables
- Cutting and Weld Prep
- Electric Vehicles
- En Español
- Finishing
- Hydroforming
- Laser Cutting
- Laser Welding
- Machining
- Manufacturing Software
- Materials Handling
- Metals/Materials
- Oxyfuel Cutting
- Plasma Cutting
- Power Tools
- Punching and Other Holemaking
- Roll Forming
- Safety
- Sawing
- Shearing
- Shop Management
- Testing and Measuring
- Tube and Pipe Fabrication
- Tube and Pipe Production
- Waterjet Cutting
Industry Directory
Webcasts
Podcasts
FAB 40
Advertise
Subscribe
Account Login
Search
Penn State researchers receive $535K to manufacture metal parts for naval applications
- June 11, 2018
- News Release
- Finishing
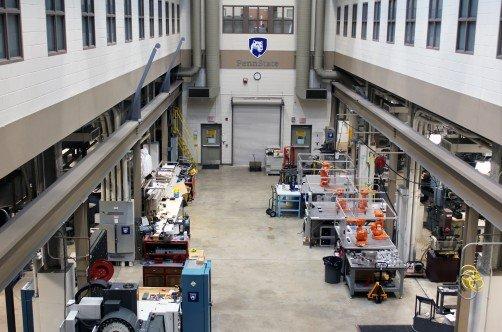
The new superfinishing lab will be installed in the Factory for Advanced Manufacturing Education Lab, a 10,000-sq.-ft. integrated high-bay laboratory for teaching and research.
Penn State researchers in University Park, Pa., have received more than $535,000 to install a state-of-the-art superfinishing lab for 3-D-printed metal parts. The new lab will complement the existing subtractive processing technology in the Factory for Advanced Manufacturing Education (FAME) Lab within the Harold and Inge Marcus Department of Industrial and Manufacturing Engineering.
Together the machinery will provide the subtractive processing capability necessary to transform printed parts into components ready for product assembly. The equipment in the FAME Lab will be used for both the instruction of engineering students and academic research.
Funding for the one-year project, titled “Super Finishing of Printed Metallic Parts for High Performance Naval Systems,” is being provided by the Defense University Research Instrumentation Program, which operates through the Department of Defense’s Office of Naval Research.
Ed DeMeter, a professor in the Marcus department, is the principal investigator on the project.
“The Navy has a strong interest in identifying and researching the technical issues of using 3-D-printed metal parts for naval applications now and in the future,” said DeMeter. “They want to better understand how to design parts while identifying potential barriers and also benefits that may arise between the metal printing process and any secondary processing that is done to smooth out the surface texture of these parts.”
Metal parts can be printed to near net shape but require thermal processing to improve their material properties and hard tool machining processes to remove supports and create functional surfaces, according to DeMeter.
“Superfinishing processes are used to remove burrs and to smooth surfaces. All three postprocesses are needed to produce parts for demanding national defense applications, which include jet engines and sea vessels,” he said.
Functional surfaces of the parts need to have extremely tight geometric control and a very smooth surface finish, explained DeMeter. If a part is subjected to a lot of cyclic loading (such as force and vibration) and has rough surfaces, it promotes the formation of cracks and premature failure of the parts.
subscribe now
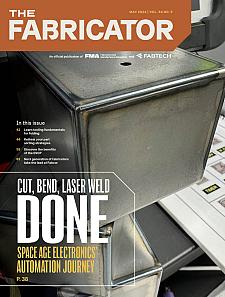
The Fabricator is North America's leading magazine for the metal forming and fabricating industry. The magazine delivers the news, technical articles, and case histories that enable fabricators to do their jobs more efficiently. The Fabricator has served the industry since 1970.
start your free subscription- Stay connected from anywhere
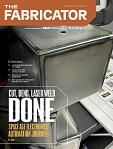
Easily access valuable industry resources now with full access to the digital edition of The Fabricator.
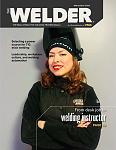
Easily access valuable industry resources now with full access to the digital edition of The Welder.
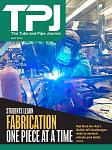
Easily access valuable industry resources now with full access to the digital edition of The Tube and Pipe Journal.
- Podcasting
- Podcast:
- The Fabricator Podcast
- Published:
- 04/16/2024
- Running Time:
- 63:29
In this episode of The Fabricator Podcast, Caleb Chamberlain, co-founder and CEO of OSH Cut, discusses his company’s...
- Trending Articles
Tips for creating sheet metal tubes with perforations
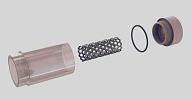
Supporting the metal fabricating industry through FMA
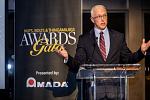
JM Steel triples capacity for solar energy projects at Pennsylvania facility
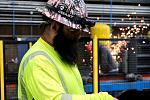
Are two heads better than one in fiber laser cutting?
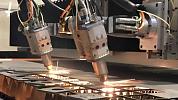
Fabricating favorite childhood memories
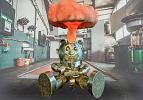
- Industry Events
16th Annual Safety Conference
- April 30 - May 1, 2024
- Elgin,
Pipe and Tube Conference
- May 21 - 22, 2024
- Omaha, NE
World-Class Roll Forming Workshop
- June 5 - 6, 2024
- Louisville, KY
Advanced Laser Application Workshop
- June 25 - 27, 2024
- Novi, MI