- FMA
- The Fabricator
- FABTECH
- Canadian Metalworking
Categories
- Additive Manufacturing
- Aluminum Welding
- Arc Welding
- Assembly and Joining
- Automation and Robotics
- Bending and Forming
- Consumables
- Cutting and Weld Prep
- Electric Vehicles
- En Español
- Finishing
- Hydroforming
- Laser Cutting
- Laser Welding
- Machining
- Manufacturing Software
- Materials Handling
- Metals/Materials
- Oxyfuel Cutting
- Plasma Cutting
- Power Tools
- Punching and Other Holemaking
- Roll Forming
- Safety
- Sawing
- Shearing
- Shop Management
- Testing and Measuring
- Tube and Pipe Fabrication
- Tube and Pipe Production
- Waterjet Cutting
Industry Directory
Webcasts
Podcasts
FAB 40
Advertise
Subscribe
Account Login
Search
Zinc phosphate metal finishing line improves part turnaround time for precision machining company
- August 12, 2019
- News Release
- Finishing
Situation
A.R. Machining is a contract manufacturer in Hutto, Texas, specializing in precision machining work for the aerospace, oil, gas, and semiconductor industries. With more than 50 highly trained employees, a 38,000-sq.-ft. manufacturing facility, and more than 24 CNC mills and lathes with 4-axis capability, the company’s fast-turn prototype products include turnkey CNC production, part finishing, and mechanical assembly.
Original equipment manufacturers are demanding fast turnaround time from their suppliers to bring their products to market faster, and A.R. Machining’s customers are no exception. But without in-house finishing capability, the company was hampered. “Using outside finishers took several days and made it difficult to meet customer delivery requirements,” reported Matthew Dobias, president.
“Our oil and gas customers required corrosion-protected parts and just-in-time delivery,” Dobias continued. “These are large, down-hole steel components that often are stored outdoors before installation, so they are subject to corrosion. In our area, outside finishers are several hours away. Turnaround time was a real problem. Also, their finishing tank sizes were limited for our larger parts. We needed large capacity and ferrous metal corrosion protection.”
As part of its continuous improvement mission, the company decided to investigate in-house finishing options.
Resolution
“We knew about Birchwood Technologies and asked their area account manager, Tom Ingersoll, for metal finishing input,” said Dobias. “Birchwood Technologies chemists performed several no-obligation, no-cost test finishes on our sample parts in their lab. Tom recommended their zinc phosphate process and showed us how their MicroLok® MZN and Dri-Touch® Plus IRP3 process combination would answer our needs, so we went with a new system.”
This fine-grained zinc phosphating process is designed for iron and steel components, which make up the majority of A.R. Machining’s present work. Applied at 120 to 160 degrees F, the finish complies with MIL-DTL-16232G, Type Z Classes 1, 2, and 3—important because the company is expanding its work in the military sector. When sealed with a rust preventive, the finish has excellent corrosion resistance and provides antigalling protection and break-in lubricity to critical working surfaces, which are advantageous in certain military applications.
For extra corrosion protection, the Dri-Touch Plus IRP3 heavy-duty protective coating produces a robust film that is suitable for use on parts for limited outside storage, into warehouses, and for certain battlefield conditions. The product is an effective water displacer, with a self-healing, soft waxy film with thick consistency and high moisture resistance. “The combination process really improves the appearance of finished goods,” reported Dobias, “with parts coming out a nice, uniform dark gray or black depending on the material.”
The system comprises seven 220-gal.-capacity tanks with a 48- by 30- by 35-ft. footprint. An overhead crane is positioned above the system to handle large parts, which are up to 6 ft. long by 2 ft. in diameter, as well as baskets of smaller parts. The tank line is equipped with an adjacent ion exchange system, which purifies and recycles the system’s rinse waters. The result is a closed-loop system that conserves water and makes no discharge into the sewer system.
“With our new in-house system, we get same-day finishing. The cost is less than half compared to outside finishing and is improving as more work is added. Just as important, we eliminated many hidden costs using outside finishing vendors, such as the extra part moves, packing and repacking parts, inventorying and inspecting parts when received, and unexpected delays on different part projects,” Dobias added.
Birchwood Technologies
www.birchwoodtechnologies.com
subscribe now
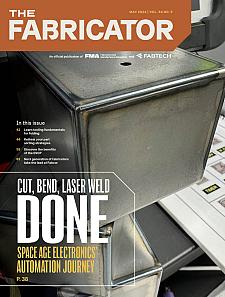
The Fabricator is North America's leading magazine for the metal forming and fabricating industry. The magazine delivers the news, technical articles, and case histories that enable fabricators to do their jobs more efficiently. The Fabricator has served the industry since 1970.
start your free subscription- Stay connected from anywhere
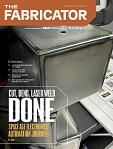
Easily access valuable industry resources now with full access to the digital edition of The Fabricator.
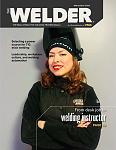
Easily access valuable industry resources now with full access to the digital edition of The Welder.
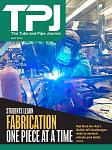
Easily access valuable industry resources now with full access to the digital edition of The Tube and Pipe Journal.
- Podcasting
- Podcast:
- The Fabricator Podcast
- Published:
- 04/16/2024
- Running Time:
- 63:29
In this episode of The Fabricator Podcast, Caleb Chamberlain, co-founder and CEO of OSH Cut, discusses his company’s...
- Trending Articles
Tips for creating sheet metal tubes with perforations
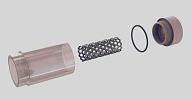
Are two heads better than one in fiber laser cutting?
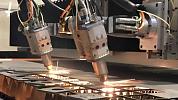
Supporting the metal fabricating industry through FMA
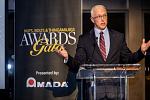
JM Steel triples capacity for solar energy projects at Pennsylvania facility
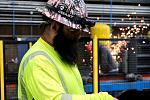
Omco Solar opens second Alabama manufacturing facility
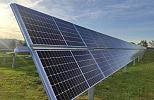
- Industry Events
16th Annual Safety Conference
- April 30 - May 1, 2024
- Elgin,
Pipe and Tube Conference
- May 21 - 22, 2024
- Omaha, NE
World-Class Roll Forming Workshop
- June 5 - 6, 2024
- Louisville, KY
Advanced Laser Application Workshop
- June 25 - 27, 2024
- Novi, MI