- FMA
- The Fabricator
- FABTECH
- Canadian Metalworking
Categories
- Additive Manufacturing
- Aluminum Welding
- Arc Welding
- Assembly and Joining
- Automation and Robotics
- Bending and Forming
- Consumables
- Cutting and Weld Prep
- Electric Vehicles
- En Español
- Finishing
- Hydroforming
- Laser Cutting
- Laser Welding
- Machining
- Manufacturing Software
- Materials Handling
- Metals/Materials
- Oxyfuel Cutting
- Plasma Cutting
- Power Tools
- Punching and Other Holemaking
- Roll Forming
- Safety
- Sawing
- Shearing
- Shop Management
- Testing and Measuring
- Tube and Pipe Fabrication
- Tube and Pipe Production
- Waterjet Cutting
Industry Directory
Webcasts
Podcasts
FAB 40
Advertise
Subscribe
Account Login
Search
Laser cutting machines with automation help metal service center chain expand in-house processing
- July 1, 2021
- News Release
- Laser Cutting
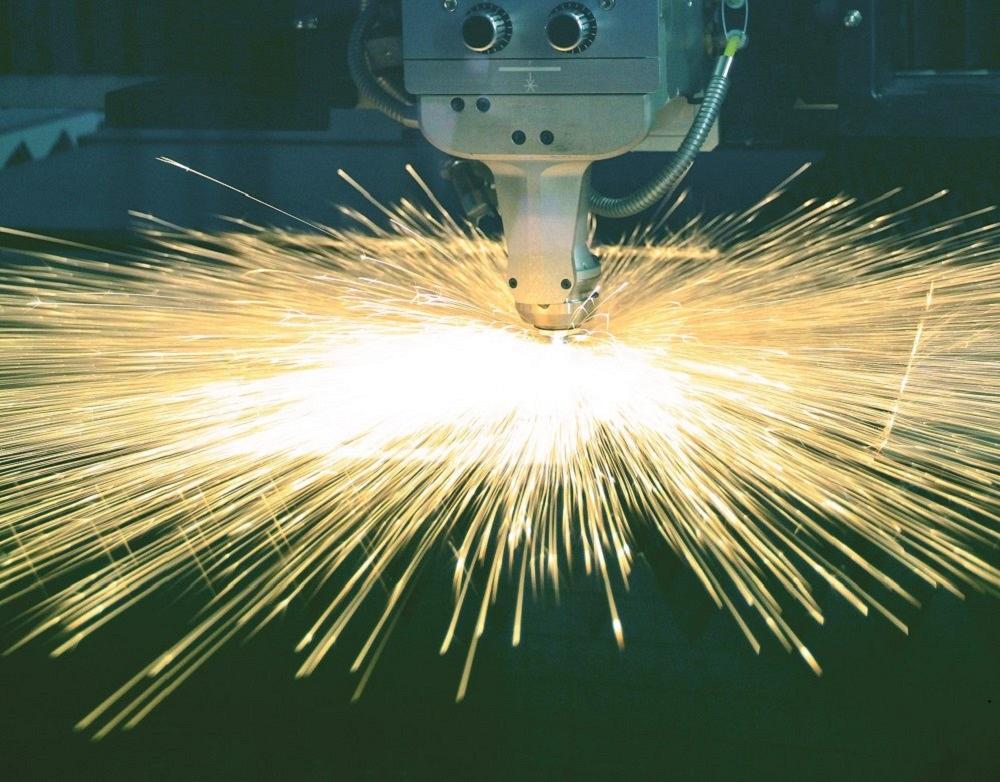
Boyd Metals installed one of its three Prima Power Laser Genius machines at its Fort Smith, Ark., location.
Situation
Boyd Metals is a metals service center that offers metal processing and metal distribution from locations in Fort Smith, Ark.; Joplin, Mo.; Oklahoma City, Okla.; Little Rock, Ark.; and Tyler, Texas. The company’s inventory lines include carbon steel, stainless steel, aluminum, red metals, and fiberglass. Boyd Metals carries a variety of products, including structural shapes, sheet and plate, pipe and tubing, valves and fittings, and expanded metals and gratings.
“In the past, service centers were expected to just sell raw material of carbon steel, aluminum, stainless steel, and others,” explained Audie Dennis, vice president/general manager of the Joplin facility. “Traditional machines in a service center were cut-to-length lines, slitting lines, saws, etc. However, over the past 25 years, service center customers have demanded more of a turnkey-type operation where they can get a finished part, and even moving more and more into assembly. Today it is almost expected that a service center can provide first-step processing capabilities like plate burning, sawing, laser cutting, and press brake bending. The trend is a move to more value-added services. We want to be a problem-solver for our customers. We find out where their bottlenecks are and solve the problem.”
In 2019 Boyd Metals formed a committee to explore what was available in the 2D fiber laser market. “We met to define what we thought our laser needs were today and would be in the future,” said Steve Harvey, vice president/general manager of the Fort Smith facility. “We surveyed what was available in the market, and we visited with laser users in our geographic areas.
“I happened to read an article in The FABRICATOR magazine on the Prima Power laser machines and, coincidently, received a phone call from the Prima Power salesman introducing himself, so I invited him to stop by and visit,” Harvey continued. “After the committee met, we invited five laser manufacturers to our Fort Smith office to hear what they had to say.”
Resolution
After narrowing their choices down and comparing systems, the committee decided to go with Prima Power.
“They weren’t just making a presentation to us but wanted to be there for us as a partner. They were genuinely interested in helping us move into this market. With the training and everything Prima Power had to offer, there was never any pressure—just good information,” Harvey said.
Boyd Metals purchased three Prima Power Laser Genius machines for the Fort Smith, Joplin, and Oklahoma City facilities, installed in late 2019 and early 2020.
These high-range 2D laser machines cut a variety of materials, including highly reflective metals such as aluminum alloys, copper, and brass. Varied thicknesses can be cut efficiently, although productivity increases particularly with thin and medium-gauge sheet metal. Automation modules make the machines suitable for small batches and large-scale production.
High-dynamic linear motors on the X and Y axes help ensure a 15% increase in productivity compared with conventional drive systems, according to the manufacturer. CNC proprietary management helps guarantee accuracy in cutting and head positioning.
The laser machines have a high-brilliance, 6-kW fiber laser. The fiber cutting head features a single-lens strategy, safe impact protection system, high dynamic focal axis with 35-mm stroke, lens drawer with a quick-alignment system, and a protection glass drawer for simple inspection.
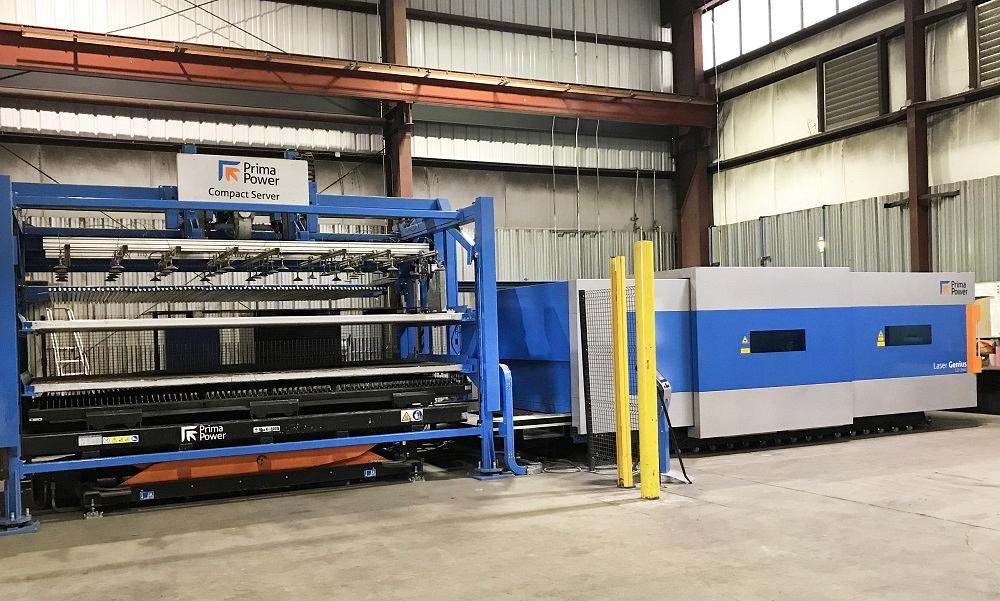
The Compact Server material handling system comprises two storage units: one for blanks and one for processed sheets.
The machines’ NC Express e³ software is a scalable CAD/CAM application that can be used for single-part processing or fully automatic batch processing. No matter the production style, the software offers support for any programming of the laser and turrets and handles anything from importing and unfolding 3D models to processing daily ERP data.
Boyd Metals purchased the Compact Server—a small-footprint loading/ unloading device for handling blanks and processed sheets—with each of the three laser machines. It comprises two storage units: one for blanks and one for processed sheets.
“We knew we wanted to go with the fiber laser,” said Richard Schultz, vice president and general manager of the Oklahoma City facility. “What I really liked about the Laser Genius is the small footprint. We also wanted to get some sort of automation, and the Compact Server gave us the automation we needed without adding much to the total footprint.
“There were jobs that we were doing on our high-definition plasma that took hours to perform. Today the Laser Genius with the Compact Server sped the process up tremendously,” Schultz explained. “We can cut the same parts with the Laser Genius in 10% of the time it took on the plasma cutter.”
“Between the time we ordered the laser and the time it was installed, we began servicing a customer that needed a great amount of laser cutting,” said Dennis. “The customer went into a cost-cutting mode, and if we didn’t have the Laser Genius, we may have lost the customer. But by being able to do the laser cutting in-house rather than outsourcing it, we were able to reduce our cost and pass the savings on to the customer. It is now a top account with repetitive business with several hundred thousand dollars per year in laser cutting work.”
“If you can’t produce in-house, you often don’t get a seat at the table,” Harvey said. “We’ve been able to expand into the OEM products, where you must have the tight tolerances, repeatability, and precision to be certified as a supplier.”
“The Laser Genius has opened up a new source of business for us ... a new revenue stream,” concluded Dennis. “We are now able to cut thinner material than we have ever before, with tighter tolerances. We can produce a much higher-quality part with much tighter tolerances that can go right into production. This is more important today, as we are taking on more and more fabrication operations for our customers. We were doing processing for a number of customers that were sending their laser work elsewhere. They were very excited when we installed the Laser Genius. We’ve picked up a great deal of laser cutting business from existing customers.”
Related Companies
subscribe now
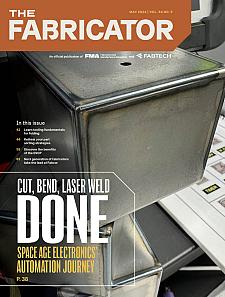
The Fabricator is North America's leading magazine for the metal forming and fabricating industry. The magazine delivers the news, technical articles, and case histories that enable fabricators to do their jobs more efficiently. The Fabricator has served the industry since 1970.
start your free subscription- Stay connected from anywhere
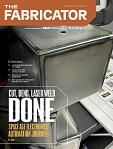
Easily access valuable industry resources now with full access to the digital edition of The Fabricator.
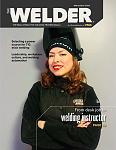
Easily access valuable industry resources now with full access to the digital edition of The Welder.
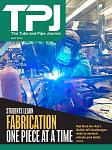
Easily access valuable industry resources now with full access to the digital edition of The Tube and Pipe Journal.
- Podcasting
- Podcast:
- The Fabricator Podcast
- Published:
- 04/16/2024
- Running Time:
- 63:29
In this episode of The Fabricator Podcast, Caleb Chamberlain, co-founder and CEO of OSH Cut, discusses his company’s...
- Trending Articles
Tips for creating sheet metal tubes with perforations
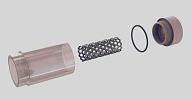
Are two heads better than one in fiber laser cutting?
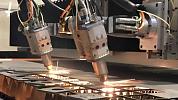
Supporting the metal fabricating industry through FMA
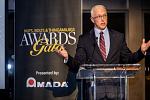
JM Steel triples capacity for solar energy projects at Pennsylvania facility
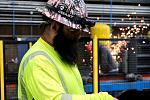
Omco Solar opens second Alabama manufacturing facility
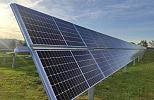
- Industry Events
16th Annual Safety Conference
- April 30 - May 1, 2024
- Elgin,
Pipe and Tube Conference
- May 21 - 22, 2024
- Omaha, NE
World-Class Roll Forming Workshop
- June 5 - 6, 2024
- Louisville, KY
Advanced Laser Application Workshop
- June 25 - 27, 2024
- Novi, MI