- FMA
- The Fabricator
- FABTECH
- Canadian Metalworking
Categories
- Additive Manufacturing
- Aluminum Welding
- Arc Welding
- Assembly and Joining
- Automation and Robotics
- Bending and Forming
- Consumables
- Cutting and Weld Prep
- Electric Vehicles
- En Español
- Finishing
- Hydroforming
- Laser Cutting
- Laser Welding
- Machining
- Manufacturing Software
- Materials Handling
- Metals/Materials
- Oxyfuel Cutting
- Plasma Cutting
- Power Tools
- Punching and Other Holemaking
- Roll Forming
- Safety
- Sawing
- Shearing
- Shop Management
- Testing and Measuring
- Tube and Pipe Fabrication
- Tube and Pipe Production
- Waterjet Cutting
Industry Directory
Webcasts
Podcasts
FAB 40
Advertise
Subscribe
Account Login
Search
Wind turbine manufacturer increases productivity, operator safety with turning table
- February 23, 2022
- News Release
- Materials Handling
Situation
At its new mechatronic competence center in Aurich, Germany, wind turbine manufacturer Enercon produces machine houses and rotor hubs for its EP1 to the EP5 platforms.
After painting, the large-volume cast bodies of the rotor hubs are taken to the assembly line, where their inner workings are installed. Each 71-ton rotor hub (with correspondingly large dimensions) must be turned on the assembly line in the factory—a mammoth task in the intralogistics process.
“Previously we turned the hubs around with two indoor cranes. This could take up to two hours,” explained Keno Claassen, who is responsible for procurement of resources at the competence center.
Resolution
Now Enercon is the first wind turbine manufacturer to break new ground in handling rotor hubs on the assembly line, switching from the use of cranes and slings to the compact Tecdos Tool Mover turning table from RUD Ketten Rieger & Dietz GmbH.
Enercon required a turning table that can safely pick up and turn loads of up to 71 tons and three different hub sizes: 5 degrees, 3.5 degrees, and 2.5 degrees. “The maximum load was not a problem; we were able to meet it by individually adapting our standard range of the [machine],” explained Ralph Roth, who works at RUD in the development and design of Tecdos mechanical engineering.
The rotor hubs have a diameter of up to 3.5 m, and the standard version of the turning table has a supporting surface of 2.5 by 3.5 m. This, together with the Y shape of the hub and a support angle that does not exactly correspond to 90 degrees, was not optimal for a stable turning process. So RUD designed special layers, matched to the three different hub sizes, that can be fitted to the turning table.
The turning process that previously took about two hours with a crane and chain is now completed in just a few minutes. Enercon benefits not only from process optimization and time savings at the Aurich production plant, but the indoor cranes that previously were used to turn the hubs now are free to perform other tasks. And workers benefit from better ergonomics and a safer work environment.
subscribe now
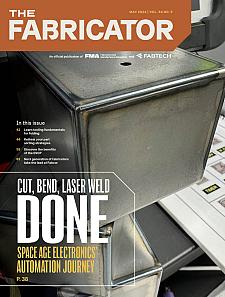
The Fabricator is North America's leading magazine for the metal forming and fabricating industry. The magazine delivers the news, technical articles, and case histories that enable fabricators to do their jobs more efficiently. The Fabricator has served the industry since 1970.
start your free subscription- Stay connected from anywhere
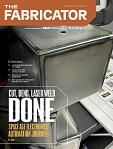
Easily access valuable industry resources now with full access to the digital edition of The Fabricator.
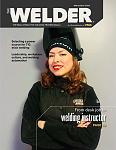
Easily access valuable industry resources now with full access to the digital edition of The Welder.
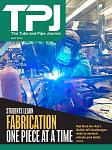
Easily access valuable industry resources now with full access to the digital edition of The Tube and Pipe Journal.
- Podcasting
- Podcast:
- The Fabricator Podcast
- Published:
- 04/16/2024
- Running Time:
- 63:29
In this episode of The Fabricator Podcast, Caleb Chamberlain, co-founder and CEO of OSH Cut, discusses his company’s...
- Trending Articles
Tips for creating sheet metal tubes with perforations
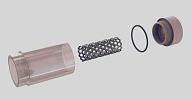
JM Steel triples capacity for solar energy projects at Pennsylvania facility
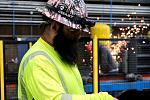
Are two heads better than one in fiber laser cutting?
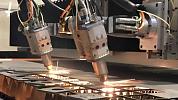
Supporting the metal fabricating industry through FMA
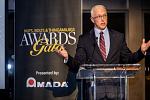
Omco Solar opens second Alabama manufacturing facility
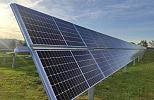
- Industry Events
16th Annual Safety Conference
- April 30 - May 1, 2024
- Elgin,
Pipe and Tube Conference
- May 21 - 22, 2024
- Omaha, NE
World-Class Roll Forming Workshop
- June 5 - 6, 2024
- Louisville, KY
Advanced Laser Application Workshop
- June 25 - 27, 2024
- Novi, MI