- FMA
- The Fabricator
- FABTECH
- Canadian Metalworking
Categories
- Additive Manufacturing
- Aluminum Welding
- Arc Welding
- Assembly and Joining
- Automation and Robotics
- Bending and Forming
- Consumables
- Cutting and Weld Prep
- Electric Vehicles
- En Español
- Finishing
- Hydroforming
- Laser Cutting
- Laser Welding
- Machining
- Manufacturing Software
- Materials Handling
- Metals/Materials
- Oxyfuel Cutting
- Plasma Cutting
- Power Tools
- Punching and Other Holemaking
- Roll Forming
- Safety
- Sawing
- Shearing
- Shop Management
- Testing and Measuring
- Tube and Pipe Fabrication
- Tube and Pipe Production
- Waterjet Cutting
Industry Directory
Webcasts
Podcasts
FAB 40
Advertise
Subscribe
Account Login
Search
Storage, sawing, and sorting upgrades help machine manufacturer improve efficiency
- January 31, 2023
- News Release
- Sawing
Situation
Haver & Boecker Maschinenfabrik is a manufacturer of wire mesh, as well as machines for handling and processing bulk materials. Its plant in Münster, Germany, about an hour from company headquarters in Oelde, includes sheet metal processing, frame manufacturing, a shot blasting and paint system, and a sawing center that comprises an automated bar storage system and two seamlessly connected circular saws.
Round and flat materials, tubes, hollow sections, and angles in numerous cross-sections are stored in 1,037 shelves of the 6-m-high system. The parts are primarily steel and stainless steel, but also aluminum and other metals.
“As a manufacturer of special machinery, we deal with an extremely wide variety of materials, but only in very small batch sizes,” said Christian Hinse, work preparation manager. “Just under one-third of the parts we saw are unique pieces, and for 90% of the parts, we are between a batch size of one and 10.”
After more than 20 years in service, the sawing center from Kasto Maschinenbau was no longer compatible with current technology; the PLC had been discontinued, and obtaining spare parts was becoming increasingly difficult.
“We had also introduced SAP [enterprise resource planning software] in the company, but the existing system was only connected to SAP IM via FTP [file transfer protocol],” Hinse explained. “Therefore, there was a lack of transparency in the current stock levels.”
In addition, the integrated production circular saw from Kasto was heavily worn and had reached the end of its life expectancy. Downtimes were increasing, and cutting results were no longer satisfactory.
Resolution
Representatives from Haver & Boecker and Kasto got together and decided to fully modernize the sawing center so that it would again meet current requirements.
“The steel construction of the bar storage system was still in perfect condition; therefore, a complete replacement would not have been economically viable,” Hinse said. “However, within the scope of the project, we did remove a second storage area with 320 cassettes. Materials were kept in this area that could not be stored in a cantilever storage system. This reduction created additional space in the hall.”
Kasto expanded the bar storage system by three rows of racks and by 60 cassette spaces within the bar storage system, so the necessary capacity remained available.
The operating gantry crane, which independently stores and removes materials up to 6.5 m long, also needed modernization. Kasto replaced the control cabinets, energy supply system, measuring and control technology, and hoist and traversing motors with new components and installed an S7 controller to replace the outdated PLC. These changes doubled the crane’s speed from 30 to 60 m/min.
The KASTOlogic system now is used for warehouse management. It is connected to the SAP ERP system via a jointly defined interface. “This speeds up and streamlines our processes tremendously since, for example, sawing orders are now also transmitted electronically to the miter saw,” said Project Manager Claudia Bürger.
Instead of two manual saws connected to the former cassette storage system and an automatic circular saw connected to the bar storage system, there are now two sawing machines connected to the bar storage system.
One of them is the KASTOflex A universal circular sawing machine for materials with a diameter of up to 150 mm, which delivers straight and miter cuts automatically. Next to it is a KASTOvariospeed SC 15, a CNC, fully automatic production circular saw for cutting solid materials, profiles, and tubes in all grades. The saw is connected to the robot handling system KASTOsort, which removes and deposits the cut pieces.
“We have optimized our processes and made them more efficient, which allows us to achieve sustainable cost savings,” Bürger said. "We have a better overview of our inventories, can react more flexibly to short-notice changes, and experience fewer downtimes.”
Related Companies
subscribe now
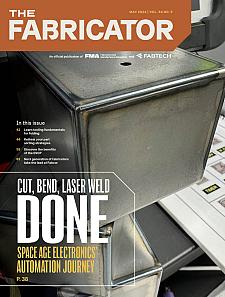
The Fabricator is North America's leading magazine for the metal forming and fabricating industry. The magazine delivers the news, technical articles, and case histories that enable fabricators to do their jobs more efficiently. The Fabricator has served the industry since 1970.
start your free subscription- Stay connected from anywhere
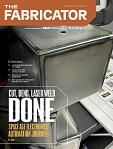
Easily access valuable industry resources now with full access to the digital edition of The Fabricator.
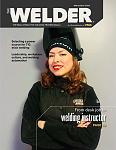
Easily access valuable industry resources now with full access to the digital edition of The Welder.
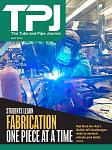
Easily access valuable industry resources now with full access to the digital edition of The Tube and Pipe Journal.
- Podcasting
- Podcast:
- The Fabricator Podcast
- Published:
- 04/16/2024
- Running Time:
- 63:29
In this episode of The Fabricator Podcast, Caleb Chamberlain, co-founder and CEO of OSH Cut, discusses his company’s...
- Trending Articles
Tips for creating sheet metal tubes with perforations
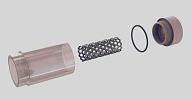
Are two heads better than one in fiber laser cutting?
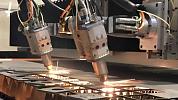
Supporting the metal fabricating industry through FMA
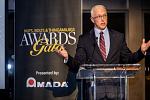
JM Steel triples capacity for solar energy projects at Pennsylvania facility
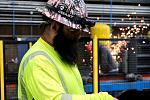
Omco Solar opens second Alabama manufacturing facility
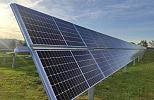
- Industry Events
16th Annual Safety Conference
- April 30 - May 1, 2024
- Elgin,
Pipe and Tube Conference
- May 21 - 22, 2024
- Omaha, NE
World-Class Roll Forming Workshop
- June 5 - 6, 2024
- Louisville, KY
Advanced Laser Application Workshop
- June 25 - 27, 2024
- Novi, MI