- FMA
- The Fabricator
- FABTECH
- Canadian Metalworking
Categories
- Additive Manufacturing
- Aluminum Welding
- Arc Welding
- Assembly and Joining
- Automation and Robotics
- Bending and Forming
- Consumables
- Cutting and Weld Prep
- Electric Vehicles
- En Español
- Finishing
- Hydroforming
- Laser Cutting
- Laser Welding
- Machining
- Manufacturing Software
- Materials Handling
- Metals/Materials
- Oxyfuel Cutting
- Plasma Cutting
- Power Tools
- Punching and Other Holemaking
- Roll Forming
- Safety
- Sawing
- Shearing
- Shop Management
- Testing and Measuring
- Tube and Pipe Fabrication
- Tube and Pipe Production
- Waterjet Cutting
Industry Directory
Webcasts
Podcasts
FAB 40
Advertise
Subscribe
Account Login
Search
Gearbox system helps machinery-maker simplify maintenance access on roller leveler
- October 8, 2021
- News Release
- Shop Management
Situation
Delta Steel Technologies Inc., a second-generation manufacturing company in Irving, Texas, builds and repairs machinery for steel mills across the country. In its 226,000-sq.-ft. facility, the company’s 120 employees design and manufacture customized stretch levelers, rotary shears, temper mills, and cut-to-length lines. All are used to convert rough coils of steel into flat, precision-cut material suitable for use by automakers, appliance producers, and other manufacturers of sheet metal components and assemblies.
The company also refurbishes, remanufactures, and retrofits legacy equipment; performs cylinder and gearbox repairs; does custom machining and fabrication; and offers turnkey installations of its systems. And many of these systems are highly automated to maximize throughput. Simply put, Delta Steel’s goal is to deliver whatever its customers need to process steel efficiently and profitably.
During one recent project, however, the manufacturer ran into a snag. After delivering the winning bid on a roller leveler, President Joseph Savariego and his design team found that the gearboxes in a critical subassembly had to be placed closer together than they liked. They knew that this configuration would make it difficult for the customer to service the machine in the future.
This roller leveler uses 11 rollers total, five above the sheet and six below. Each roller is attached to a driveshaft, and each driveshaft connects to a gearbox driven by its own 150-HP motor. The designers needed to stack the two rows of components one atop the other to fit everything into the limited space, but this restricted access to the bottom row of drive components. So they developed a slide mechanism that would allow technicians to easily disconnect each gearbox and motor combination from the driveshaft and simply pull it back and out of the way for servicing. Despite this space-saving arrangement, however, a compact but powerful gearbox would still be required.
Resolution
Delta Steel decided to reach out to electromechanical system provider NORD DRIVESYSTEMS, with which it had worked for a number of years. Application Engineer Jeff Wittrock recommended an SK5207 series MaxxDrive large industrial gear unit in a parallel-axis configuration and 14-to-1 drive ratio. With a Unicase one-piece housing, symmetrical design, and extremely high power density for its size, the gearbox would provide the torque, performance, and service life needed for this demanding application.
"There were definitely some challenges," Savariego said. "For example, if one of the bottom gearboxes were to be damaged, how would you access it without having to remove the ones above it? And even the best gearbox and motor needs routine maintenance, which would have been extremely difficult if we'd gone with a less flexible design. That’s what led us to the sliding mechanism, but that meant we had to minimize the driveshaft angle, which in turn required that we keep everything close together. NORD was quite helpful and willing to help us through the entire process until we reached the optimal design.”
Every project is different, Savariego added, noting that details like these often must be worked out after the customer has accepted the preliminary proposal. It’s only as designers delve into the complete requirements that they can understand all of the potential hurdles, making it especially important to partner with suppliers offering a variety of component options backed by experienced support and applications people.
“NORD was able to help us transmit a lot of torque in a fairly small package,” he said. “They were also quite helpful in determining the best way to arrange the gearboxes.”
subscribe now
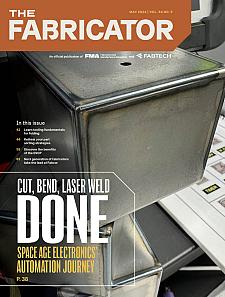
The Fabricator is North America's leading magazine for the metal forming and fabricating industry. The magazine delivers the news, technical articles, and case histories that enable fabricators to do their jobs more efficiently. The Fabricator has served the industry since 1970.
start your free subscription- Stay connected from anywhere
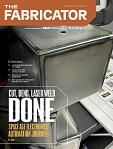
Easily access valuable industry resources now with full access to the digital edition of The Fabricator.
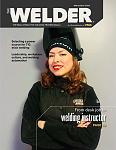
Easily access valuable industry resources now with full access to the digital edition of The Welder.
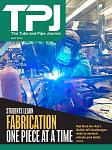
Easily access valuable industry resources now with full access to the digital edition of The Tube and Pipe Journal.
- Podcasting
- Podcast:
- The Fabricator Podcast
- Published:
- 04/16/2024
- Running Time:
- 63:29
In this episode of The Fabricator Podcast, Caleb Chamberlain, co-founder and CEO of OSH Cut, discusses his company’s...
- Trending Articles
Tips for creating sheet metal tubes with perforations
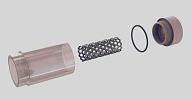
JM Steel triples capacity for solar energy projects at Pennsylvania facility
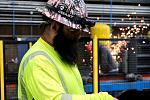
Are two heads better than one in fiber laser cutting?
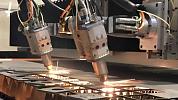
Supporting the metal fabricating industry through FMA
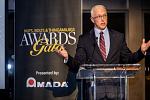
Omco Solar opens second Alabama manufacturing facility
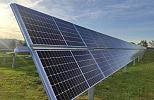
- Industry Events
16th Annual Safety Conference
- April 30 - May 1, 2024
- Elgin,
Pipe and Tube Conference
- May 21 - 22, 2024
- Omaha, NE
World-Class Roll Forming Workshop
- June 5 - 6, 2024
- Louisville, KY
Advanced Laser Application Workshop
- June 25 - 27, 2024
- Novi, MI