Executive Vice President
- FMA
- The Fabricator
- FABTECH
- Canadian Metalworking
Categories
- Additive Manufacturing
- Aluminum Welding
- Arc Welding
- Assembly and Joining
- Automation and Robotics
- Bending and Forming
- Consumables
- Cutting and Weld Prep
- Electric Vehicles
- En Español
- Finishing
- Hydroforming
- Laser Cutting
- Laser Welding
- Machining
- Manufacturing Software
- Materials Handling
- Metals/Materials
- Oxyfuel Cutting
- Plasma Cutting
- Power Tools
- Punching and Other Holemaking
- Roll Forming
- Safety
- Sawing
- Shearing
- Shop Management
- Testing and Measuring
- Tube and Pipe Fabrication
- Tube and Pipe Production
- Waterjet Cutting
Industry Directory
Webcasts
Podcasts
FAB 40
Advertise
Subscribe
Account Login
Search
La tecnología de plegado de metal de precisión permite la manufactura por kits
Cómo las plegadoras de metal les dan a los fabricantes opciones de flujo de partes
- By David Prokop
- January 4, 2024
- Article
- Bending and Forming
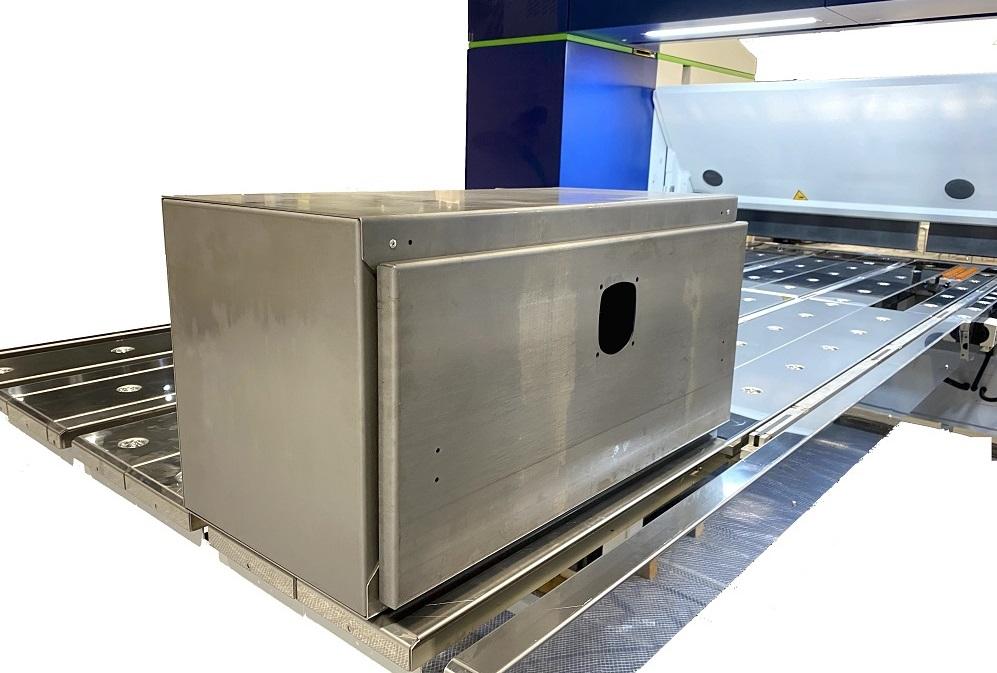
FIGURA 1. Las partes para este subensamble de carrocería son plegadas y formadas en kit antes de enviarse corriente abajo para ensamble y soldadura robótica.
Desde que existe la manufactura, los fabricantes han buscado mejores maneras de hacer su trabajo. Impulsadas por los avances tecnológicos en herramientas y maquinaria, las mejoras en la eficiencia han aumentado los márgenes, han creado una ventaja competitiva, han abierto nuevos mercados, han enfrentado retos de mano de obra, y han brindado una mejora estable en los medios y métodos de producción.
Al mismo tiempo que los avances tecnológicos hacen posibles los cambios más drásticos, los fabricantes se encuentran continuamente con nuevos conceptos de mejora de procesos. Sin embargo, las limitaciones causadas por un solo proceso ineficiente pueden imposibilitar la obtención de mejoras corriente abajo.
La relación entre el corte y el doblado es un buen ejemplo. Sin herramientas duras por las que haya que preocuparse, el corte láser ha hecho que el corte sea extraordinariamente flexible. Aunque si usted va corriente abajo podría ver a un operador tomando herramientas, procesando partes de prueba y haciendo todas las verificaciones necesarias para empezar a operar en una máquina de doblado antigua. Configuraciones extensas e impredecibles demandan lotes de cierta cantidad.
Los tamaños de lote más pequeños se vuelven un reto, y la producción basada en kits – donde cada pieza en un ensamble o subensamble se procesa en secuencia, moviéndose en “kits” de un centro de trabajo al siguiente – simplemente se vuelve algo impráctico. Aunque ciertos métodos flexibles de doblado han hecho práctica y rentable la producción basada en kits. Actualmente, esto incluye la tecnología de plegado de precisión.
La producción en kits demanda flexibilidad
La crisis de mano de obra de la actualidad está forzando a las compañías a reevaluar sus métodos de producción, y esto incluye la producción en kits. Cuando se emplea, el flujo basado en kits puede afectar enormemente la eficiencia de la producción, y puede verse beneficiado cada proceso corriente abajo.
La manufactura en kits produce grupos de partes similares o disímiles que forman subensambles o ensambles completos. Con frecuencia alimentan directamente operaciones corriente abajo como ensamble o soldadura robótica (vea la Figura 1). Los kits se producen en el orden de necesidad y se entregan justo a tiempo para alimentar el siguiente proceso.
Este tipo de producción es increíblemente eficiente pues elimina la mayoría de los problemas generados por el mayor infractor de la manufactura esbelta: la sobreproducción. Sin embargo, un requerimiento evita que la mayoría adopte este concepto increíblemente eficiente: la producción eficiente de una sola pieza. Esto, repito, tiene que ver con el tiempo de configuración – especialmente si cada parte en un kit requiere una configuración única de máquina. Si un sistema no es flexible (por ejemplo, que una configuración de herramental pueda producir diversas formas), y no puede cambiar rápidamente, comúnmente producir kits no es algo práctico.
Sin embargo, en todo el taller de fabricación la tecnología en evolución ha hecho que lo impráctico sea práctico. Remóntese a principios de la década de 1980, cuando imperaban las punzonadoras de torreta. Típicamente producían partes cortadas en grandes cantidades para compensar costos de configuración sin valor agregado. Esta acumulación de producto obstruía los procesos corriente abajo y se volvía difícil de manejar. Los fabricantes a veces gastaban mucho dinero para manejar el problema, y sin embargo conseguían poco alivio.
La mala utilización y la alta demanda de mano de obra hacen a las torretas el objetivo perfecto para ser reemplazadas por una tecnología de alto impacto: el corte láser. Cuando entraron los láseres en el mercado del punzonado a mediados de la década de 1980, cambió para siempre la manera de cortar piezas. Los láseres introdujeron la posibilidad de moverse entre tipos de material y espesores sin esfuerzo y sin restricciones de herramental, eliminando la importancia del volumen de producción. Rápidamente siguieron los láseres automatizados, y pudieron cortarse más piezas de lo que alguna vez se creyó posible.
Ya sin estar atadas a un proceso de corte ineficiente de piezas, las compañías pudieron programar la producción para beneficiar a las operaciones corriente abajo. Sin embargo, debido a algunas ineficiencias inherentes en el formado, este nivel increíble de producción esbelta de piezas cortadas sólo pudo impulsar la eficiencia hasta ahí.
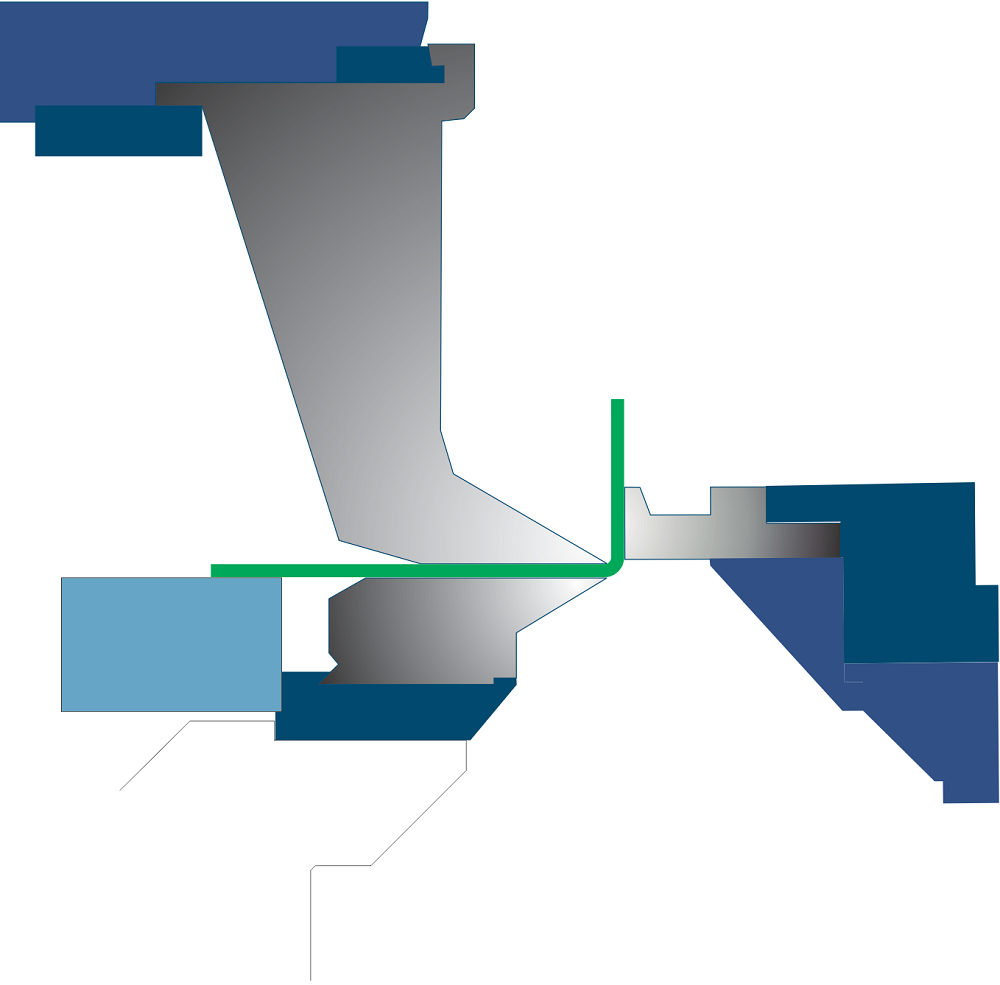
FIGURA 2. Una plegadora dobla de la misma manera que mide un transportador. El espesor del material no tiene impacto en el ángulo creado o medido.
Combatiendo el cuello de botella del doblado
La tecnología de doblado ha evolucionado significativamente, aunque para muchas operaciones el formado sigue siendo un proceso sumamente arduo, complicado e ineficiente que requiere operadores altamente experimentados. En los talleres comunes, las máquinas sólo producen dobleces alrededor del 10 al 15% del tiempo. Las variaciones en la dirección del grano, el espesor y la resistencia a la tracción causan estragos al tratar de formar piezas de trabajo exactas de manera confiable, y esto requiere que los operadores verifiquen y vuelvan a verificar las partes. La fatiga aparece conforme levantan, voltean y colocan partes grandes y cargan herramientas para los cambios.
Una operación podría combatir estos retos de diversas maneras, como abrir las tolerancias de formado para atender problemas de exactitud y producir lotes mayores para reducir el impacto de configuraciones extensas de máquina. Sin embargo, las decisiones en el formado pueden causar graves efectos en cadena corriente abajo. Las partes mal formadas son difíciles de soldar robóticamente, y requieren más soldadura, más rectificado, más acabado. El ensamble es más tardado, y esto involucra más gente y más esfuerzo.
Las soluciones que implican cantidades mayores esperan mejorar la eficiencia mediante procesos y movimiento repetidos. Sin embargo, producir lotes más grandes tiene un tremendo impacto en la manera en que fluye el trabajo por las operaciones corriente abajo. El resultado final: un fabricante hace más de lo que se necesita, y las operaciones corriente abajo sufren.
Cada parte extra no necesitada evita que se produzca una parte necesitada y compromete la capacidad de responder rápidamente a las necesidades del cliente. Además, si una parte de configuración tiene error, ¿cuántas partes se hacen incorrectamente hasta que el error se descubre y se repara? Las partes extra ocupan valioso espacio de producción; éstas tienen que apilarse, rastrearse, almacenarse, encontrarse y recuperarse cuando se necesiten de nuevo. Las partes se dañan, se pierden, o un cambio de ingeniería convierte en desperdicio ese carro de partes cortadas y formadas.
La capacidad de ir de una parte a otra con poco o ningún esfuerzo ni destreza es algo absolutamente necesario para el flujo efectivo de kits. Las dobladoras de panel han soportado por años la producción en kits. Sin embargo, las partes fuera del alcance de la dobladora de panel, debido a las limitaciones en el tamaño de la parte, longitud de pestaña o espesor, se dejaron a los conceptos de producción tradicionales. Aquí es donde el plegado llena una necesidad, ofreciendo formado flexible y productivo adecuado para la producción basada en kits, sin importar el tamaño de la parte.
Por qué el plegado es flexible
Después de que la pieza de trabajo se coloca en la máquina plegadora, el brazo superior (también llamado brazo de sujeción) fija el material contra el brazo inferior. El brazo de plegado se mueve en un arco, pivoteando la pestaña en su centro de doblez al ángulo deseado (vea la Figura 2).
Las plegadoras modernas tienen varios ejes que se ajustan a los valores de herramienta adecuados para el espesor de material, tipo, radio de doblez interior y ángulo de doblez. Los ejes de la máquina trabajan juntos para crear el equivalente de un dado en V infinitamente variable, ajustándose automáticamente para el espesor del material, el ángulo y el radio de doblez deseado (vea la Figura 3).
Debido a que el herramental de una plegadora opera de manera independiente del tipo de material y espesor, los dobleces de radio de cualquier tamaño, dobladillos y dobleces en S no son más que un programa. Todos se forman con el mismo juego de herramientas (vea la Figura 4). Un solo juego de herramental estándar es capaz de formar una caja de cuatro lados a una profundidad de 15.75 pulgadas (40 cm), en acero suave de 0.196 pulgadas en material de calza (vea la Figura 5). El cambio de herramienta simplemente es cuestión de apilar los segmentos de herramienta a la longitud requerida para formar la parte.
La estrategia de herramental se simplifica más por la capacidad de las plegadoras de doblar de manera bidireccional, tanto hacia arriba como hacia abajo. El cambio manual de herramientas comúnmente tarda menos de tres minutos. Un cambio automático de herramienta completa su tarea en menos de 90 segundos en promedio, y puede ocurrir en paralelo a la acción del operador que quita la última parte formada y trae a la mesa la siguiente pieza cortada. No se pierde tiempo de producción, y el tiempo de una parte a otra es controlado por la máquina en sí, lo que elimina toda diferencia causada por distracciones del operador.
Un flujo perfecto desde el CAD hasta la parte
Sin embargo, la flexibilidad del formado es sólo una pieza del rompecabezas. Al fabricar kits, los fabricantes deben manejar una cantidad extraordinaria de información. El flujo basado en kits es sumamente eficiente – hasta que alguien abre el programa incorrecto o identifica mal una parte.
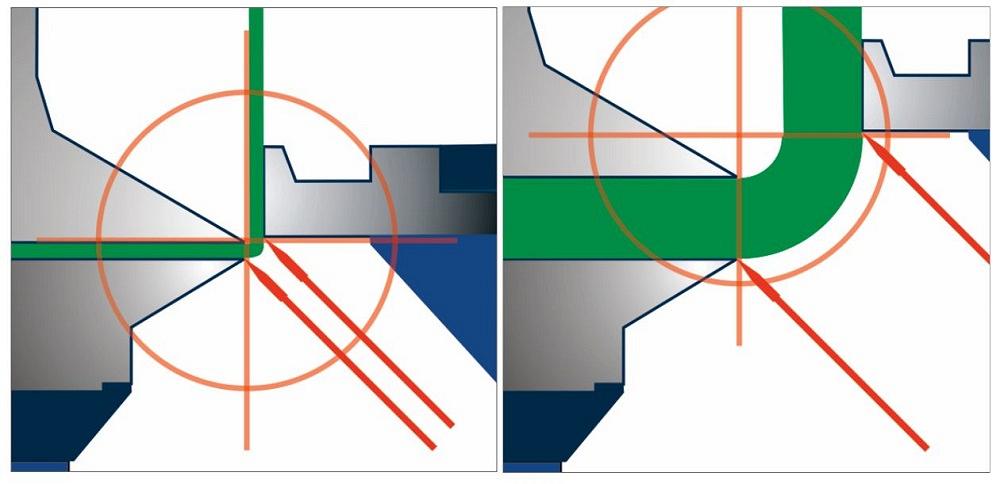
FIGURA 3. Los ejes de una plegadora se ajustan para diferentes espesores de material cambiando el espacio entre la hoja de plegado (la herramienta en el brazo basculante que hace contacto con la pieza de trabajo) y el centro teórico del doblez.
¿Dónde empezar? Todo empieza con un programa. Es fundamental la capacidad de importar al software modelos CAD, incluso ensambles enteros, y hacer programas listos para correr en cuestión de segundos. Esto es la base para el procesamiento exitoso de partes que difieren entre sí. Una programación muy larga dificultaría el tipo de resultado eficiente requerido para la implementación exitosa de la producción en kits.
Los escáneres de código QR o de barras pueden abrir el programa para producción en la máquina e incluso pueden contener información del tamaño de la parte para programación variable. Los kits recurrentes pueden guardarse, detallando cada parte y cantidad en el orden correcto, junto con el número de veces que se va a producir el kit. La estrategia de herramental y el procesamiento sencillo del plegado ayuda al software a determinar rápidamente la secuencia de doblado, optimizar el proceso de doblado y el movimiento de la máquina, y calcular las estaciones de herramental necesarias para hacer la tarea.
Una vez configurado el herramental, empieza el formado. Es aquí donde las ventajas del plegado hacen posible la producción en kits. Debido a la manera en que dobla una plegadora, las variaciones en el espesor del material, la tensión y el grano tienen poco o nulo impacto en la exactitud de la parte. La exactitud de un doblez a otro es controlada de manera confiable por la máquina, ya que la parte se sujeta al indicador de vacío que automáticamente alimenta la parte de un doblez al siguiente.
El poder calibrar desde atrás de la parte, fuera de la pestaña, en una muesca o pestaña adyacente brinda varios puntos de referencia para una amplia variedad de diseño de partes. Brazos neumáticos de escuadrado también suben y bajan automáticamente según se requiera. Pueden producirse simultáneamente piezas de trabajo del tamaño correcto, lo cual puede ser especialmente útil para partes en espejo (vea la Figura 6).
Exactitud, consistencia, sustentabilidad
La exactitud de la primera parte es algo fundamental en la producción en kits. Los métodos tradicionales de doblado pueden requerir varios dobleces de prueba para acercarse a la exactitud de las partes, tanto en la longitud de la pestaña como en el ángulo. Sin embargo, cuando producen kits, las máquinas con frecuencia doblan una parte única tras otra; no hay dobleces de prueba. La máquina forma sólo una parte antes de moverse a una parte diferente, y si esa parte no es exacta, la producción en kits se perturba, y todo el proceso podría no cumplir los requerimientos de producción.
Finalmente, el proceso también necesita ser sustentable. Sin importar el tamaño de la parte, la ergonomía del plegado libera al operador de levantar, voltear o batallar para manipular perfiles. Nunca se necesita más de un operador (vea la Figura 7), y el tamaño de la parte no tiene impacto en la exactitud de la misma.
Estos beneficios ergonómicos ayudan a estandarizar los tiempos de operación, lo cual es crucial para alimentar la producción corriente abajo. Los tiempos de doblez erráticos e inconsistentes hacen que la programación sea un reto – aunque los tiempos de operación en una plegadora varían poco. Una parte grande ciertamente tardará más que una parte pequeña, pero es una diferencia de segundos, no de minutos.
Acerca de la seguridad
Las consideraciones de seguridad son un factor importante en todo proceso de manufactura. Aun cuando las cortinas de luz han reducido sustancialmente las lesiones por compresión, las lesiones por movimiento repetitivo siguen siendo un problema con ciertos equipos, y poco puede hacerse para prevenirlas. La fatiga del operador reduce rápidamente el rendimiento, introduce error en las partes y aumenta el riesgo de lesión.
El plegado es un proceso seguro, lo cual es aún más importante cuando se les pide a operadores menos experimentados que mantengan una alta velocidad de producción. Algunos sistemas rotan y reposicionan automáticamente la pieza de trabajo entre dobleces, y algunos ofrecen automatización de la carga y descarga de partes. Eso tiene evidentes beneficios de seguridad, pero además ayuda con el flujo de partes – especialmente en la manufactura en kits.
Transporte de las piezas de trabajo entre procesos
La producción en kits demanda un transporte eficiente de las piezas de trabajo. Después de todo, el kit no tiene un formado “acabado” hasta que el siguiente proceso puede hacer algo con él – y éste no puede hacer nada mientras los kits permanezcan corriente arriba como piezas de trabajo en proceso (WIP, por sus siglas en inglés).
FIGURA 4. Todos los dobleces, incluyendo dobleces dobles y dobladillos, se hacen con un solo juego de herramientas.
Es aquí donde la banda transportadora puede tener un papel crítico (vea la Figura 8 y Figura 9). Está puesta a la altura de la mesa de la plegadora, y las partes simplemente se empujan hacia ésta en la secuencia correcta – es decir, en el orden en que las necesiten la soldadura o el ensamble (o cualquier otro proceso corriente abajo).
Los carros, personalizados para una agrupación de partes, también son de uso común para ensamblar kits y transferirlos al siguiente proceso. Muchos talleres carecen de una ruta directa de un proceso al siguiente, y en estos escenarios, los carros pueden ser la solución perfecta.
Industria 4.0 para un flujo estable
Mantener un flujo estable de partes con exactitud confiable es la meta, y no inundar el siguiente proceso ni dejarlo sin partes. Es un acto de equilibrio, y la cuarta revolución industrial está haciendo más fácil este acto de equilibrio con la digitalización de datos y la comunicación de máquina a máquina.
La interfaz OPC UA hace que la información del ritmo de producción esté fácilmente disponible. Los datos de una máquina incluso pueden disparar cuándo debe iniciar una operación corriente arriba, sincronizando adecuadamente la entrega de partes al siguiente proceso en línea.
Encontrando el flujo con kits
Aun cuando no sea para todos, la producción en kits ofrece muchos beneficios únicos para las compañías que buscan maneras de compensar la falta de mano de obra y aportar cierta estabilidad a un taller lleno de partes esperando a ser usadas. La sobreproducción inicia una cascada hacia prácticas de desperdicio, las cuales muchos creen necesarias para mantener los niveles de producción. En realidad, si las partes se produjeran cuando se necesitan para alimentar inmediatamente la siguiente etapa de producción, la mayoría quedarían atónitos por las ganancias en rendimiento.
Aun cuando optar por el “kit completo” no sea práctico para sus necesidades particulares, usted podría obtener enormes beneficios adoptando al menos algunos de los conceptos. Implementar una tecnología para formar partes de manera más precisa y sustentable, con menos mano de obra y en cantidades menores beneficiará a todo el proceso de manufactura. La avanzada tecnología de plegado de la actualidad es adecuada para satisfacer las necesidades del fabricante de hoy que busca ese siguiente paso en la eficiencia del proceso.
About the Author
David Prokop
100 International Dr.
Peachtree City, GA 30269
(770) 631-0002
About the Publication
Compañías Relacionadas
subscribe now
FMA Communications ha introducido al mercado la edición en Español de la revista The Fabricator. Esta versión consiste del mismo tipo de artículos técnicos y sección de lanzamientos de nuevos productos que actualmente presentan el personal de primera categoría de Fabricator en Inglés.
start your free subscription- Podcasting
- Podcast:
- The Fabricator Podcast
- Published:
- 04/16/2024
- Running Time:
- 63:29
In this episode of The Fabricator Podcast, Caleb Chamberlain, co-founder and CEO of OSH Cut, discusses his company’s...
- Trending Articles
Los operadores de prensa dobladora inexpertos hacen indispensable el repensar la seguridad
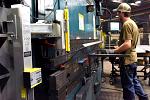
La mezcla de gas auxiliar impulsa la tecnología del láser de fibra
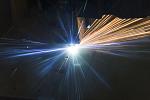
Prescripción para la reducción del desperdicio: arreglo esbelto de las instalaciones
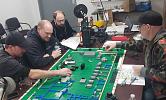
Máquina de corte por láser diseñada para el mercado mexicano
La sierra de doble carro sigue los contornos del tubo perfectamente
- Industry Events
16th Annual Safety Conference
- April 30 - May 1, 2024
- Elgin,
Pipe and Tube Conference
- May 21 - 22, 2024
- Omaha, NE
World-Class Roll Forming Workshop
- June 5 - 6, 2024
- Louisville, KY
Advanced Laser Application Workshop
- June 25 - 27, 2024
- Novi, MI