Contributing Writer
- FMA
- The Fabricator
- FABTECH
- Canadian Metalworking
Categories
- Additive Manufacturing
- Aluminum Welding
- Arc Welding
- Assembly and Joining
- Automation and Robotics
- Bending and Forming
- Consumables
- Cutting and Weld Prep
- Electric Vehicles
- En Español
- Finishing
- Hydroforming
- Laser Cutting
- Laser Welding
- Machining
- Manufacturing Software
- Materials Handling
- Metals/Materials
- Oxyfuel Cutting
- Plasma Cutting
- Power Tools
- Punching and Other Holemaking
- Roll Forming
- Safety
- Sawing
- Shearing
- Shop Management
- Testing and Measuring
- Tube and Pipe Fabrication
- Tube and Pipe Production
- Waterjet Cutting
Industry Directory
Webcasts
Podcasts
FAB 40
Advertise
Subscribe
Account Login
Search
Aprovechando al máximo el manejo de material
Los avances de máquinas y la automatización ayudan a los talleres a reducir el desperdicio al mínimo
- By Rob Colman
- February 14, 2023
- Article
- Manufacturing Software
El manejo de sobrantes ha cambiado desde el surgimiento de los láseres de fibra y el auge de software de anidado dinámico, de programación avanzada y de control de producción. Estas tecnologías han facilitado la educción del desperdicio al mínimo y les brindan a programadores y operadores opciones en cuanto a la manera de manejar los materiales. Éstas no han eliminado por completo los sobrantes de la ecuación de fabricación, pero han hecho más fácil evitarlos.
Éstas, en combinación con otras tecnologías, han hecho más fácil el manejo y el uso de los sobrantes que siguen generando los talleres.
Usando cortes de hoja estándar
“Cuando las punzonadoras de torreta seguían siendo la opción de corte principal para los fabricantes que procesaban chapa, no siempre era de ayuda la capacidad de anidado dinámico, que abría la puerta a una amplia variedad de partes con base en el tipo de material y en su espesor. La razón de esto era la cantidad de herramental y la secuenciación requerida para crear el nido rápidamente”, dijo Matt Milazzo, gerente de producto de láser, AMADA AMERICA. “Conforme la tecnología de fibra láser se ha vuelto la opción evidente de corte para muchos fabricantes, el anidado dinámico se ha vuelto una herramienta valiosa en la programación y procesamiento rápidos de partes de alta mezcla. Combinado con sistemas automatizados para manejo de material, el anidado dinámico está ayudando a los fabricantes a volverse más eficientes al mismo tiempo que se maximiza el uso de material”.
Los láseres con frecuencia permiten un uso exhaustivo de material, minimizando costos, y en muchos casos, evitando la creación de sobrantes.
La programación láser para generar código para cualquier número de partes y geometría con base en un tipo y espesor de material en particular se ha vuelto algo común”, dijo Matt Milazzo. “Los clientes están buscando anidar partes dinámicamente sin basarse en un orden en particular sino más bien en un tipo de material en particular, espesor, utilización del material y en la fecha de entrega. Los requerimientos de construcción que cubren a diversos clientes o ensambles pueden procesarse juntos. Los clientes pueden permitir que el software llene una hoja para usar el material de la manera más eficiente posible. ‘Reglas’ en el software, como por ejemplo cumplir la utilización de un material en particular antes que crear el nido para producción puede resultar benéfico”.
“En muchos casos, el uso de anidado dinámico les ha permitido a los clientes minimizar el número de tamaños de hoja diferentes que deben mantener en inventario, lo que reduce los costos de material. Hay muchos ejemplos de clientes que adoptan estos métodos, mientras que clientes que operan un solo láser o varios láseres nunca usan el mismo nido a lo largo de todo un día dado”.
El único problema que puede surgir al producir partes para varias órdenes en el mismo nido puede estar en el proceso de clasificación y en asegurar que esas partes sean canalizadas de manera correcta a partir de ahí. Por supuesto, los fabricantes de máquinas están ideando maneras de ayudar a manejar esto también.
“Con un software, un taller puede monitorear todo el flujo de trabajo de producción de sus órdenes”, dijo Kevin Cuseo, ingeniero de ventas de productos de software, TRUMPF North America. “Usando el software mediante PCs y tablets con aplicaciones web, usted puede usar nuestro software Oseon para darle al personal en la planta de producción acceso personalizado a los procesos. Si hablamos de una hoja llena de partes de varias órdenes, usted tendría a un operador responsable de remover partes de un esqueleto, y su tablet le mostraría una vista general de cómo se ve esa hoja anidada, qué partes están en la misma y cómo deben canalizarse a partir de ahí”.
Entonces, en este caso, con una hoja llena, sería de utilidad clasificar por órdenes separadas.
Posibilidades de las partes de relleno
Si los clientes desean adoptar el anidado tipo dinámico y al mismo tiempo mantener una utilización alta de material, entonces otra opción es el rellenado automático de áreas sin usar de la hoja con partes de relleno.
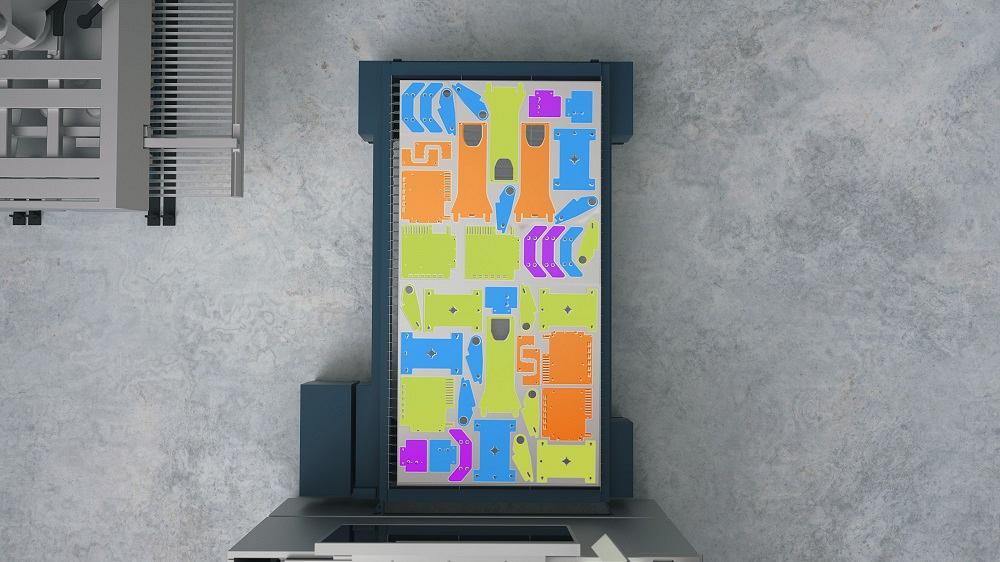
El único problema que puede surgir al producir partes para varias órdenes en el mismo nido para evitar sobrantes puede estar en el proceso de clasificación y en asegurar que las partes se canalicen correctamente a partir de ahí. Por supuesto, los fabricantes de máquinas están ideando maneras de ayudar a manejar esto también. Por ejemplo, el software Oseon de TRUMPF le da al personal de la planta de producción acceso personalizado a los procesos. En esta imagen vemos cómo la Guía de Clasificación de la compañía puede ayudar a los operadores a quitar y colocar varias órdenes de una hoja. TRUMPF
“Digamos que estamos haciendo gabinetes eléctricos y sabemos que varias piezas de una abrazadera específica van a ir en cada ensamble”, dijo Milazzo. “Podemos designar varios números de partes diferentes como partes de relleno. En este ejemplo, se puede optimizarse la utilización de material mientras se permite que el software monitoree las cantidades de partes de relleno producidas. Como ejemplo, usted puede preestablecer la cantidad de esa abrazadera específica, por decir, en 500 piezas; si el software pudiera no llegar a su valor mínimo de utilización de material, el software ocuparía automáticamente las áreas sin usar de la hoja con la mayor cantidad posible de abrazaderas de “relleno” para cumplir con sus criterios de utilización, y procedería a crear ese nido. El software irá restando a la cantidad preestablecida conforme las partes de relleno se inserten automáticamente en el calendario de producción. Podemos manejar cualquier número de partes, cantidades y geometrías asociadas con partes de relleno y finalmente minimizar la creación de sobrantes mientras se maximiza la utilización de hoja”.
El otro beneficio de procesar hojas llenas, recalcó Milazzo, es que normalmente el “tiempo de rayo activo” es mayor, lo cual puede ayudar a equilibrar el tiempo que tarda la automatización ejecutando el ciclo mientras que el láser corta.
La opción de inventario flexible
Sin embargo, a algunos talleres les gusta la consistencia y no desean manejar piezas de trabajo en proceso (WIP, por sus siglas en inglés) en la planta de producción. En este caso, Milazzo indica que “juntar” un grupo de partes que forman un ensamble o subensamble específico puede ser una opción valiosa.
“En este caso, puede tener sentido ordenar una hoja de tamaño especial para que pueda maximizar el material mientras que produce “kits” completos de partes cada vez que programa una corrida”, dijo.
Para aquellos talleres que sí almacenan diferentes tamaños de hoja y desean procesar órdenes de clientes específicos por separado usando más de un tamaño de hoja, la tecnología actualmente es lo suficientemente robusta para manejarlo.
“Por ejemplo, con nuestra máquina de anidado esbelto de software TruTops Boost, combinada con nuestras capacidades de manejo de hojas, podemos usar tamaños diferentes de hoja en una corrida para evitar el desperdicio innecesario”, dijo Cuseo. “Sólo es cuestión de decirle al software, ‘hazme un nido que produzca la menor cantidad de desperdicio posible para evitar sobrantes lo más que se pueda”.
Cuando los sobrantes tienen sentido
Cuseo mencionó que con materiales usados regularmente, a veces un nido más holgado tiene más sentido en términos de productividad global que usar cada centímetro de esa hoja.
“Puede crear una regla que diga, ‘prefiero dispersar partes con un margen amplio para facilitar el manejo del proceso de quitar las partes’”, dijo.
Sin embargo, a veces con materiales más caros, un taller deseará sacar el máximo provecho posible de una hoja y ahorrar sobrantes que no puedan usarse inmediatamente para trabajo posterior. Aquí hay otra oportunidad donde el software puede ayudar.
“Digamos que estamos usando 7 pies de una hoja de 10 pies”, dijo Milazzo. “Nuestro software tiene la capacidad de reconocer ese sobrante y crear un inventario de cuántos sobrantes de ese tamaño tenemos. De manera similar, si estamos produciendo partes prototipo en una hoja y tenemos un área usable que sobra, el software puede dictarle al láser que corte la porción sin usar y grabe el tamaño de hoja sobrante”.
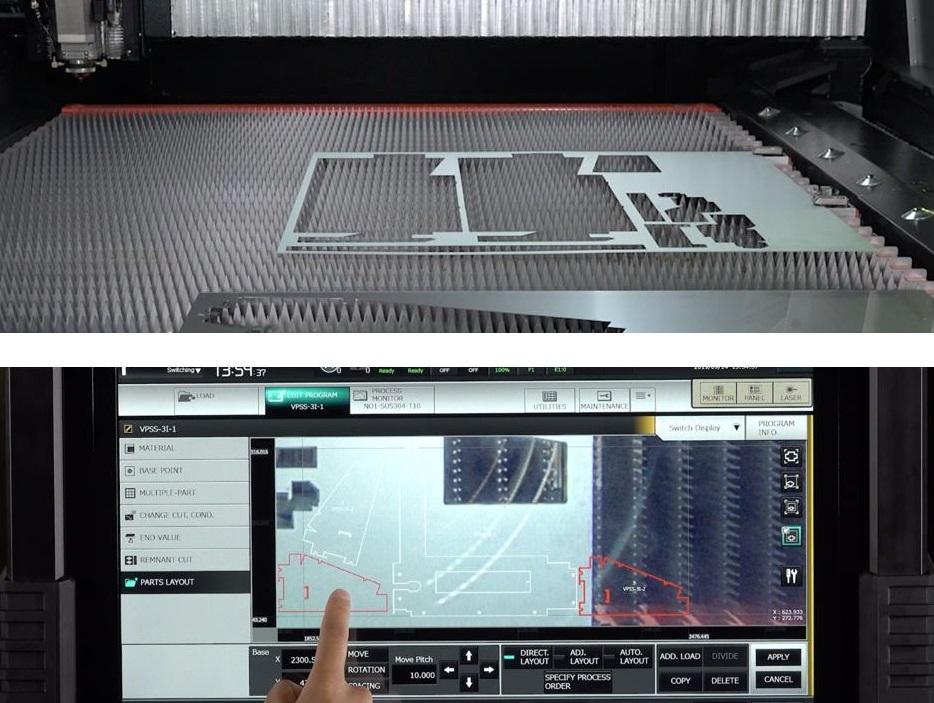
i-CAS Remnant Material con i-CAS Place Part (el que muestre mejor la acción de acomodar una parte en la página): recientemente, algunos fabricantes de máquinas introdujeron en sus máquinas sistemas de cámara para crear una configuración mediante la cual las partes pueden arrastrarse y soltarse en hojas sobrantes para un procesamiento rápido. Aquí podemos ver el sistema de cámara i-CAS de AMADA capturando la forma de un sobrante y un operador arrastrando y soltando partes en un sobrante. AMADA AMERICA
Cuseo mencionó que pueden crearse varios parámetros para la manera en que pueden cortarse los sobrantes. Por ejemplo, puede estandarizarse el tamaño de los sobrantes para ayudar más al manejo en la planta.
Además, con los operadores equipados con tablets en la planta de producción, el operador responsable de quitar las partes verá si hay sobrantes en la hoja que está procesando y podrá etiquetar y almacenar adecuadamente.
“El láser puede grabar y cortar los sobrantes para identificarlos según sea necesario, pero tener esa capacidad en las manos del operador crea más claridad y simplifica el proceso de manejo”, dijo Cuseo.
Actualmente existen muchas opciones de automatización para complementar el procesamiento láser y poder simplificar dónde se almacenan los sobrantes y permitir fácil acceso a éstos para su uso posterior. Además, los sistemas automatizados maximizan el tiempo de procesamiento láser y pueden ser importantes para asegurar que se está obteniendo el máximo de una inversión, maximizando el uso eficiente del tiempo y de los materiales.
Uso efectivo de los sobrantes
El verdadero uso eficiente de esos sobrantes en el pasado ha sido un reto en sí; programar una hoja parcial puede que no tome mucho tiempo, pero puede parecer algo que no vale la pena en un taller de fabricación con un ritmo acelerado.
Recientemente, algunos fabricantes de máquinas introdujeron sistemas de cámara a sus máquinas para crear una configuración mediante la cual las partes pudieran arrastrarse y soltarse en hojas sobrantes para un procesamiento rápido.
“Este tipo de tecnología realmente simplifica la remanufactura post-proceso de partes o agregar partes extra a una orden”, dijo James Gamache, ingeniero de ventas, TruLaser, TRUMPF North America. “Ahorra el tener que volver a la programación porque todo se hace en los controles”.
Nuestras dos ofertas de láser REGIUS y BREVIS incluyen el sistema de cámara i-CAS, el cual crea una imagen exacta del sobrante u hoja tal y como se encuentra encima de la mesa de tablillas, incluyendo partes previas que pudieran haberse cortado ya”, dijo Milazzo. “Varias partes mostradas en el control AMNC 3i pueden luego arrastrarse y soltarse en la imagen del sobrante. Luego usted puede fácilmente cuadricular la parte a una cantidad deseada o insertar partes adicionales según se requiera”.
“Otro aspecto de nuestras máquinas que hacen esta opción efectiva es que usted puede acceder a la cabina por ambos lados, lo que simplifica el poner un sobrante en la cama”.
BREVIS es un láser de fibra de 3 kW más nuevo con una plantilla física pequeña. Tiene un área de corte de 50 por 50 pulgadas (127 x 127 cm), pero puede aceptar una hoja de 48 por 96 pulgadas (121.9 por 243.8 cm).
“BREVIS combina bien con el sistema de cámara i-CAS para poner partes en sobrantes con facilidad”, dijo Milazzo. “Si, por ejemplo, una parte se dobla incorrectamente, si las cantidades fueron inexactas/mal puestas, o si se dañaron partes de alguna otra manera, puede tener sentido producir cantidades pequeñas de partes de repuesto en una máquina compacta como BREVIS en lugar de interrumpir el tiempo productivo de una celda automatizada más grande”.
La clave para los talleres es que hay sistemas de software y diseños de máquina que son adaptables para la manera en que desean trabajar. Cualquiera que sea el enfoque que adopte un taller, la productividad del procesamiento y el manejo efectivo de sobrantes está a su alcance.
About the Author
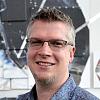
Rob Colman
About the Publication
Compañías Relacionadas
subscribe now
FMA Communications ha introducido al mercado la edición en Español de la revista The Fabricator. Esta versión consiste del mismo tipo de artículos técnicos y sección de lanzamientos de nuevos productos que actualmente presentan el personal de primera categoría de Fabricator en Inglés.
start your free subscription- Podcasting
- Podcast:
- The Fabricator Podcast
- Published:
- 04/16/2024
- Running Time:
- 63:29
In this episode of The Fabricator Podcast, Caleb Chamberlain, co-founder and CEO of OSH Cut, discusses his company’s...
- Trending Articles
Los operadores de prensa dobladora inexpertos hacen indispensable el repensar la seguridad
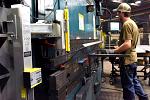
La mezcla de gas auxiliar impulsa la tecnología del láser de fibra
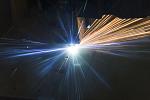
Prescripción para la reducción del desperdicio: arreglo esbelto de las instalaciones
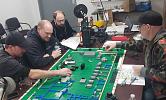
Máquina de corte por láser diseñada para el mercado mexicano
La sierra de doble carro sigue los contornos del tubo perfectamente
- Industry Events
16th Annual Safety Conference
- April 30 - May 1, 2024
- Elgin,
Pipe and Tube Conference
- May 21 - 22, 2024
- Omaha, NE
World-Class Roll Forming Workshop
- June 5 - 6, 2024
- Louisville, KY
Advanced Laser Application Workshop
- June 25 - 27, 2024
- Novi, MI