Industrial Systems and Manufacturing Instructor
- FMA
- The Fabricator
- FABTECH
- Canadian Metalworking
Categories
- Additive Manufacturing
- Aluminum Welding
- Arc Welding
- Assembly and Joining
- Automation and Robotics
- Bending and Forming
- Consumables
- Cutting and Weld Prep
- Electric Vehicles
- En Español
- Finishing
- Hydroforming
- Laser Cutting
- Laser Welding
- Machining
- Manufacturing Software
- Materials Handling
- Metals/Materials
- Oxyfuel Cutting
- Plasma Cutting
- Power Tools
- Punching and Other Holemaking
- Roll Forming
- Safety
- Sawing
- Shearing
- Shop Management
- Testing and Measuring
- Tube and Pipe Fabrication
- Tube and Pipe Production
- Waterjet Cutting
Industry Directory
Webcasts
Podcasts
FAB 40
Advertise
Subscribe
Account Login
Search
Aluminum Etc.: The future looks bright for aluminum in manufacturing
The positives are outweighing the challenges for welders and fabricators
- By Gina Cutts
- August 19, 2023
- Article
- Aluminum Welding
The rising acceptance and preferred use of aluminum in manufacturing is undeniable as aluminum products have gained in popularity over steel for many reasons.
In my opinion, being 100% recyclable is by far the most desirable quality for working with aluminum. But I will expand on this in a future article so I can give it the time this remarkable characteristic deserves.
Aluminum is lightweight with excellent strength, durability, and corrosion resistance. These properties make it an excellent choice for multiple applications, including aerospace, automotive, and construction.
One significant benefit of using aluminum over steel is its weight. Aluminum is about three times lighter than steel, making it a preferred choice in transportation industries where weight reduction is a primary concern. For instance, aluminum-bodied vehicles have become increasingly popular for their fuel economy, improved performance, and reduced emissions. Corporate Average Fuel Economy (CAFE) standards adopted in 2013 significantly increased interest in aluminum.
Another advantage of aluminum products is corrosion resistance. Unlike steel, which is prone to rust and other forms of corrosion, aluminum forms a protective layer when exposed to air, shielding it from further damage. This property makes it an ideal material for use in marine and offshore applications and other harsh environments.
Moreover, the development of advanced manufacturing technologies like 3D printing has made it easier and more cost-effective to produce aluminum products. This development has the potential to lower production costs and increase the adoption of aluminum products in various industries.
Aluminum is not without its drawbacks, however. A significant one is its high initial cost compared to steel. Although aluminum is more durable and requires less maintenance than steel, the initial investment cost can be a major deterrent for many companies.
Additionally, aluminum requires special welding techniques that can be more challenging than those used for steel. This challenge makes it more difficult to find skilled labor to work with aluminum, leading to higher labor costs. Welding educators are addressing this and introducing curriculum to expose students to both steel and aluminum—it is not one or the other anymore.
Compared to steel, aluminum products weigh less, are more durable, and provide corrosion resistance. While the high initial costs and specialized welding techniques associated with aluminum can pose challenges, the future of aluminum in mass manufacturing looks bright due to its attractive properties and advancements in manufacturing technologies.
About the Author
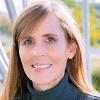
About the Publication
subscribe now
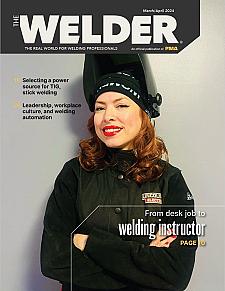
The Welder, formerly known as Practical Welding Today, is a showcase of the real people who make the products we use and work with every day. This magazine has served the welding community in North America well for more than 20 years.
start your free subscription- Stay connected from anywhere
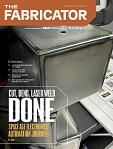
Easily access valuable industry resources now with full access to the digital edition of The Fabricator.
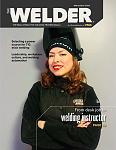
Easily access valuable industry resources now with full access to the digital edition of The Welder.
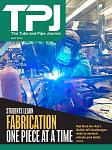
Easily access valuable industry resources now with full access to the digital edition of The Tube and Pipe Journal.
- Podcasting
- Podcast:
- The Fabricator Podcast
- Published:
- 04/16/2024
- Running Time:
- 63:29
In this episode of The Fabricator Podcast, Caleb Chamberlain, co-founder and CEO of OSH Cut, discusses his company’s...
- Trending Articles
Sheffield Forgemasters makes global leap in welding technology
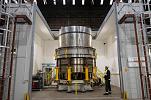
ESAB unveils Texas facility renovation
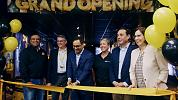
Engine-driven welding machines include integrated air compressors
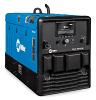
The impact of sine and square waves in aluminum AC welding, Part I
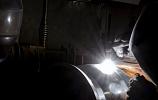
How welders can stay safe during grinding
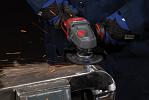
- Industry Events
16th Annual Safety Conference
- April 30 - May 1, 2024
- Elgin,
Pipe and Tube Conference
- May 21 - 22, 2024
- Omaha, NE
World-Class Roll Forming Workshop
- June 5 - 6, 2024
- Louisville, KY
Advanced Laser Application Workshop
- June 25 - 27, 2024
- Novi, MI