Industrial Systems and Manufacturing Instructor
- FMA
- The Fabricator
- FABTECH
- Canadian Metalworking
Categories
- Additive Manufacturing
- Aluminum Welding
- Arc Welding
- Assembly and Joining
- Automation and Robotics
- Bending and Forming
- Consumables
- Cutting and Weld Prep
- Electric Vehicles
- En Español
- Finishing
- Hydroforming
- Laser Cutting
- Laser Welding
- Machining
- Manufacturing Software
- Materials Handling
- Metals/Materials
- Oxyfuel Cutting
- Plasma Cutting
- Power Tools
- Punching and Other Holemaking
- Roll Forming
- Safety
- Sawing
- Shearing
- Shop Management
- Testing and Measuring
- Tube and Pipe Fabrication
- Tube and Pipe Production
- Waterjet Cutting
Industry Directory
Webcasts
Podcasts
FAB 40
Advertise
Subscribe
Account Login
Search
Aluminum Etc.: Welding aluminum isn't as difficult as you might think
- By Gina Cutts
- December 16, 2020
- Article
- Aluminum Welding

As welders understand aluminum’s unique properties, pre- and postwelding practices, and equipment settings, it’s not much different than welding any other material. Getty Images
Somewhere along the line, aluminum developed a reputation for being difficult to work with and weld. I’m not sure why that is. It seems to me that as long as you understand aluminum’s unique properties, pre- and postwelding practices, and equipment settings, it’s not much different than any other material.
Being on the education side of the welding industry has given me a unique opportunity to experiment with processes and methods that give new welding students the best start. In doing so I’ve found it beneficial to do my part in trying to remove the stigma surrounding aluminum welding.
I have taught aluminum welding to beginners first, knowing the career opportunities that are waiting for them after graduating. I realize this is contrary to how many new students are taught, which is typically with shielded metal arc welding (SMAW) carbon steel with a 6010 electrode, as it helps to develop muscle memory and puddle identification. While that’s not wrong, I would argue that starting beginners on aluminum has quite a few advantages.
Aluminum doesn’t throw off sparks, which helps new welders to get comfortable and acclimated to what they’re doing, while wearing PPE that is less restrictive than what’s needed during SMAW. Since aluminum is often welded in position, new welders can sit comfortably as they learn about the machine, practice beads, and get used to the foot pedal control during gas tungsten arc welding. Finally, aluminum burns clean, making it easier for new welders to see where they’re welding and how their puddle is forming.
Keeping track of all the items needed to make a successful weld is probably the hardest thing about welding aluminum, which is probably why it developed a reputation for being difficult. While aluminum requires you to pay attention to detail, weld with a steady hand, and possess knowledge of all the welding variables like voltage and gas pressure, the same is true for carbon steel, stainless, and other materials and processes. What sets aluminum apart from the others is the need for a little more precision in those areas.
Aluminum is becoming the go-to alloy for a variety of industries because it lowers production costs. It’s thin, light, and incredibly strong, giving it enough versatility to be used for a range of products, from snowshoes and ladders to industrial lifting equipment. Being comfortable and familiar with aluminum welding can be the foot in the door to a rewarding career.
So take this simple piece of advice: Don’t be intimidated by aluminum.
About the Author
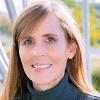
About the Publication
subscribe now
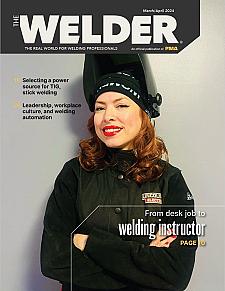
The Welder, formerly known as Practical Welding Today, is a showcase of the real people who make the products we use and work with every day. This magazine has served the welding community in North America well for more than 20 years.
start your free subscription- Stay connected from anywhere
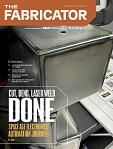
Easily access valuable industry resources now with full access to the digital edition of The Fabricator.
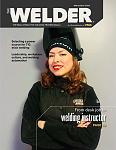
Easily access valuable industry resources now with full access to the digital edition of The Welder.
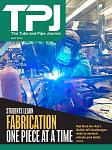
Easily access valuable industry resources now with full access to the digital edition of The Tube and Pipe Journal.
- Podcasting
- Podcast:
- The Fabricator Podcast
- Published:
- 04/16/2024
- Running Time:
- 63:29
In this episode of The Fabricator Podcast, Caleb Chamberlain, co-founder and CEO of OSH Cut, discusses his company’s...
- Trending Articles
Sheffield Forgemasters makes global leap in welding technology
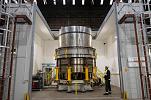
ESAB unveils Texas facility renovation
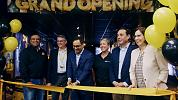
Engine-driven welding machines include integrated air compressors
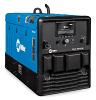
How welders can stay safe during grinding
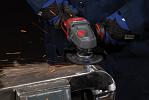
The impact of sine and square waves in aluminum AC welding, Part I
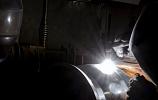
- Industry Events
16th Annual Safety Conference
- April 30 - May 1, 2024
- Elgin,
Pipe and Tube Conference
- May 21 - 22, 2024
- Omaha, NE
World-Class Roll Forming Workshop
- June 5 - 6, 2024
- Louisville, KY
Advanced Laser Application Workshop
- June 25 - 27, 2024
- Novi, MI