Applications Engineering Manager/CWI
- FMA
- The Fabricator
- FABTECH
- Canadian Metalworking
Categories
- Additive Manufacturing
- Aluminum Welding
- Arc Welding
- Assembly and Joining
- Automation and Robotics
- Bending and Forming
- Consumables
- Cutting and Weld Prep
- Electric Vehicles
- En Español
- Finishing
- Hydroforming
- Laser Cutting
- Laser Welding
- Machining
- Manufacturing Software
- Materials Handling
- Metals/Materials
- Oxyfuel Cutting
- Plasma Cutting
- Power Tools
- Punching and Other Holemaking
- Roll Forming
- Safety
- Sawing
- Shearing
- Shop Management
- Testing and Measuring
- Tube and Pipe Fabrication
- Tube and Pipe Production
- Waterjet Cutting
Industry Directory
Webcasts
Podcasts
FAB 40
Advertise
Subscribe
Account Login
Search
Addressing 8 common misconceptions about welding metal-cored wire
Understanding the capabilities and limitations for arc welding operations
- By Tre’ Heflin-King
- Updated June 11, 2023
- June 10, 2023
- Article
- Arc Welding
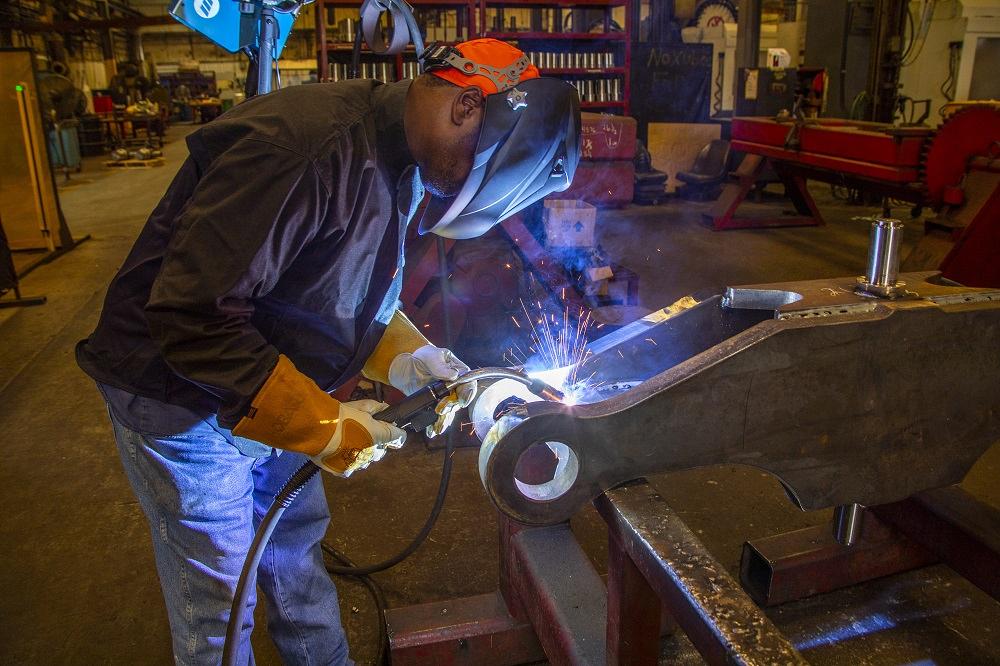
In some welding operations, using metal-cored wire eliminates certain nonvalue-added activities, allowing operators to spend time on other tasks that improve productivity.
Metal-cored wire is a hollow metal sheath filled with metallic powders, alloys, and arc stabilizers that provide benefits such as lower oxidation, higher impact strengths, and reduced silicon depositions in the final weld.
You might know this wire typically delivers fast travel speeds and high deposition rates, but it’s important to understand the other capabilities and limitations of metal-cored wire before using it in your arc welding operations. Let’s take a look at eight common misconceptions about this filler metal.
1. Metal-Cored Wire Is Too Expensive
Metal-cored wire, on average, costs more per pound than other types of filler metal when considering only the upfront purchase cost. However, it’s important to look at the preweld and postweld time savings, which can offset the initial cost. This can result in payback that justifies the additional investment or process change.
In some welding operations, using metal-cored wire eliminates certain nonvalue-added activities, allowing operators to spend time on other tasks that improve productivity. Since metal-cored wire tends to create little to no spatter, it eliminates the need for applying antispatter in the preweld phase or for chipping spatter after welding.
Because it also minimizes defects such as undercutting or lack of fusion, postweld activities such as grinding and rework usually aren’t necessary, saving labor time and money. Additionally, reducing postweld activities helps increase the flow of completed parts to other stages of production, such as painting or coating, improving overall productivity.
2. Metal-Cored Wire Can Weld Over Any Dirty Material
The characteristics of metal-cored wire make it especially suitable to weld through mill scale, oil, and other debris, which saves time and money in preweld cleaning. However, be aware that an excessive amount of contamination on the base metal can impede quality, so cleaning might still be required.
Most welding codes state that any excessive oil, grease, mill scale, or other debris should be removed from the weld area and adjacent area. But operations may not know what constitutes an excessive amount of contamination. If the metal-cored wire being used welds through the debris and the finished weld stays within acceptable levels for porosity, it’s fine to skip the preweld cleaning step. But when weld quality is affected, either through unacceptable porosity levels or too much weld contamination, then those contaminants should be removed in preweld cleaning.
3. Significant Deposition Rate Increases Are Always Achievable
The spec sheet for each metal-cored wire includes a range of achievable deposition rates with that wire. Much higher deposition rates are possible while still creating quality welds, and companies can sometimes achieve a 10% to 30% improvement in deposition rates, depending on how optimized their current welding process is.
But be aware that the actual deposition rate will depend on the application. Metal-cored wires are typically recommended for use with flat, horizontal welds. Using a pulsed welding process will allow metal-cored wires to be used in all positions, such as vertical-up welding, but this reduces the amperage and therefore the deposition rates that are achievable, especially compared to an all-position flux-cored product.
4. Wire Stick-Out Can Remain the Same for Metal-Cored Wire as for Solid Wire
It’s often assumed that metal-cored wire can be run with the same stick-out as solid wire, but that is not always the case. Solid wire typically requires a tighter stick-out, while metal-cored wire needs a longer one because of the wider arc and higher amount of filler metal being deposited.
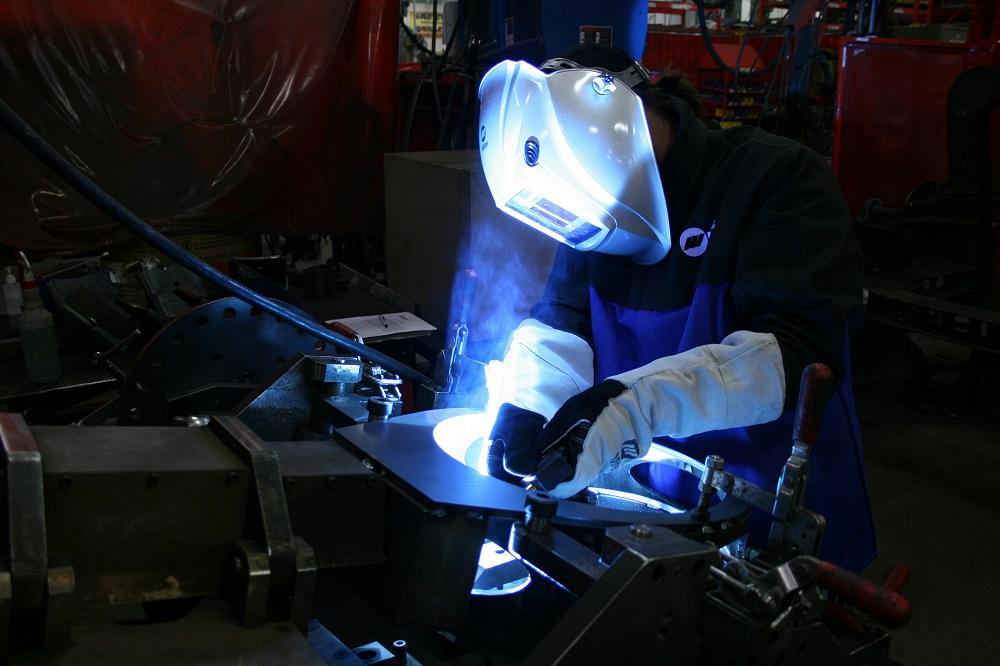
Metal-cored wire is a hollow metal sheath filled with metallic powders, alloys, and arc stabilizers that provide benefits such as lower oxidation, higher impact strengths, and reduced silicon depositions in the final weld.
When determining the proper stick-out for metal-cored wire, you need to consider three main factors: wire diameter, wire feed speed, and amperage. Typically, smaller wire diameters use a shorter stick-out. For example, with a 0.35-in.-dia. wire, a stick-out of 1/2 to 5/8 in. would be common. Using a longer one than that with a small-diameter wire will cause the wire to wander when it comes out of the contact tip. A 0.45-in.-dia. wire would use a stick-out of 3/4 to 7/8 in., while a 1/16-in.-dia. wire would use one from 3/4 to 1-1/4 in. As the wire feed speed and amperage are increased, it’s important to increase the wire stick-out. A longer one can also help improve the deposition rate slightly.
When in doubt about the proper wire stick-out, consult the wire data sheet.
5. Gun Angles Can Remain the Same for Metal-Cored Wire as for Solid Wire
When using metal-cored wire, you need to adjust the travel angle and work angle of the gun. Solid wire can often be used with either a push or a drag welding technique. But achieving a flat bead with metal-cored wire requires a 15- to 30-degree travel angle with the push technique. Using a drag technique with metal-cored wire can result in a crowned weld bead. The work angle should be 45 to 55 degrees.
If you switch to metal-cored wire in an automated weld cell, you will likely have to reprogram the gun and torch angles. Leaving those variables the same can result in faster consumable wear when using metal-cored wire. Adjusting settings such as stick-out and gun angle help compensate for the extra filler metal being added to the weld.
6. Operating Parameters Are the Same as Other Wires
The voltage and wire feed speed needed to run metal-cored wire is different than with other wires. For instance, trying to run a metal-cored wire at the same voltage and wire feed speed as a solid wire can result in undercut.
Metal-cored wire also gets into a spray transfer mode at a lower voltage than solid wire, which is beneficial since this can lead to lower heat inputs, especially when you consider the higher travel speeds that typically are achieved. To achieve the same amperage, metal-cored wires do need a higher wire feed speed than solid wires do. Compared to flux-cored wires, metal-cored wires typically have a higher upper-end voltage range.
7. Metal-Cored Wire Can Be Used in Any Application
While metal-cored wires deliver benefits in many applications, they are not suited to every welding application. For example, in applications that require welding on thin 10- or 12-ga. materials, a solid wire is likely the better option to reduce heat. A square butt weld with no gap that requires full penetration is another application that may be hard to fill with metal-cored wire because of its broad penetration profile.
Metal-cored wires are best suited to long, flat, horizontal welds that require high arc-on time. These welds deliver the most payback in productivity and efficiency thanks to the higher travel speeds. A base material that’s 1/8 in. thick or more is also recommended for metal-cored wire.
8. Metal-Cored Wire Has Poor Mechanical Properties
One of the biggest misconceptions about metal-cored wire is that it produces weaker welds than solid wire does. People often believe this is because metal-cored wire is tubular, without a solid cross section like solid wire. But metal-cored wire meets or exceeds the requirements set by the American Welding Society for the given classification.
The minimum tensile, yield, impact, and elongation properties are the same for metal-cored wires as they are for solid wires: 70 KSI minimum tensile strength, 58 KSI minimum yield strength, 22% minimum elongation, and Charpy V-Notch minimum value of 20 ft.-lbs. at -20 degrees F. Many metal-cored wires offer values above these minimums, and that information can be found on the manufacturers’ data sheets. As long as the procedure being used is sound, the metal-cored wire will create a safe weld.
As with any potential change in the welding operation, determining whether metal-cored wire is the best choice takes time. It’s important to understand the basics of metal-cored wire and how it differs from solid wire. It’s a good idea to test a wire change in a limited capacity, even in one weld cell, as a start. This can help you determine if an application is well suited to a wire conversion that can deliver time and cost savings.
About the Author
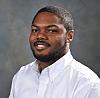
About the Publication
Related Companies
subscribe now
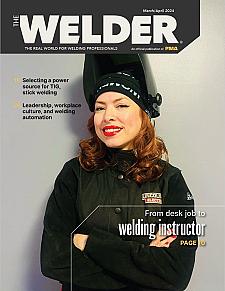
The Welder, formerly known as Practical Welding Today, is a showcase of the real people who make the products we use and work with every day. This magazine has served the welding community in North America well for more than 20 years.
start your free subscription- Stay connected from anywhere
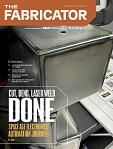
Easily access valuable industry resources now with full access to the digital edition of The Fabricator.
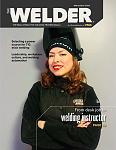
Easily access valuable industry resources now with full access to the digital edition of The Welder.
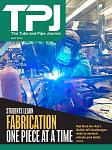
Easily access valuable industry resources now with full access to the digital edition of The Tube and Pipe Journal.
- Podcasting
- Podcast:
- The Fabricator Podcast
- Published:
- 04/16/2024
- Running Time:
- 63:29
In this episode of The Fabricator Podcast, Caleb Chamberlain, co-founder and CEO of OSH Cut, discusses his company’s...
- Trending Articles
Sheffield Forgemasters makes global leap in welding technology
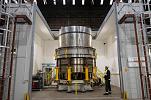
ESAB unveils Texas facility renovation
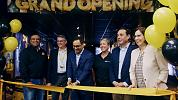
Engine-driven welding machines include integrated air compressors
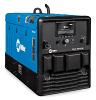
How welders can stay safe during grinding
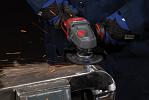
The impact of sine and square waves in aluminum AC welding, Part I
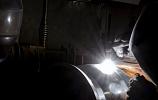
- Industry Events
16th Annual Safety Conference
- April 30 - May 1, 2024
- Elgin,
Pipe and Tube Conference
- May 21 - 22, 2024
- Omaha, NE
World-Class Roll Forming Workshop
- June 5 - 6, 2024
- Louisville, KY
Advanced Laser Application Workshop
- June 25 - 27, 2024
- Novi, MI