- FMA
- The Fabricator
- FABTECH
- Canadian Metalworking
Categories
- Additive Manufacturing
- Aluminum Welding
- Arc Welding
- Assembly and Joining
- Automation and Robotics
- Bending and Forming
- Consumables
- Cutting and Weld Prep
- Electric Vehicles
- En Español
- Finishing
- Hydroforming
- Laser Cutting
- Laser Welding
- Machining
- Manufacturing Software
- Materials Handling
- Metals/Materials
- Oxyfuel Cutting
- Plasma Cutting
- Power Tools
- Punching and Other Holemaking
- Roll Forming
- Safety
- Sawing
- Shearing
- Shop Management
- Testing and Measuring
- Tube and Pipe Fabrication
- Tube and Pipe Production
- Waterjet Cutting
Industry Directory
Webcasts
Podcasts
FAB 40
Advertise
Subscribe
Account Login
Search
Dodging the drought – in business
California-based custom fabricator leans on skilled workers, versatility
- By Amanda Carlson
- August 4, 2015
- Article
- Arc Welding
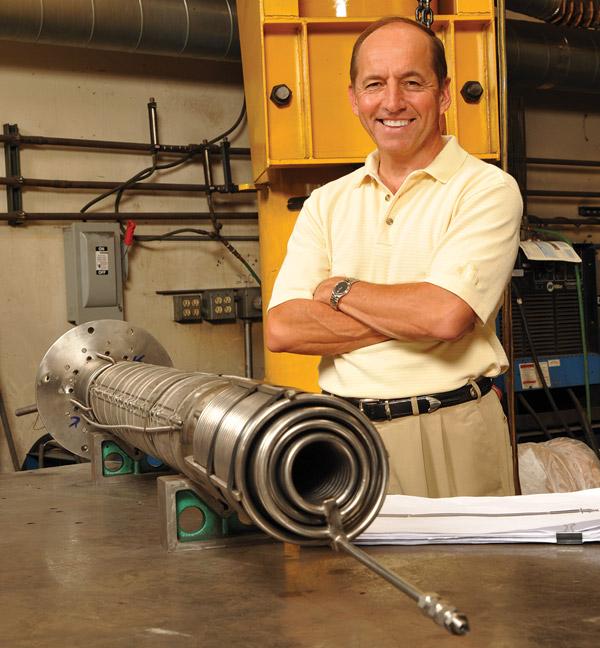
Mike Kartsonis, president and owner of Dynamic Fabrication, credits an intelligent and fabrication-savvy staff for the company’s ability to handle working on critical components belonging to aerospace and defense projects and welding to strict codes that include AWS D1.1, D1.2, D14.1, and D17.1
While the drought in California has led to major water conservation efforts and has wreaked havoc on everything from simple daily tasks to industries like agriculture and energy, there are no signs of a drought—in business, that is—at Dynamic Fabrication, a Santa Ana, Calif.-based custom fabrication, welding, and machine shop. Much of that has to do with the company’s diverse capabilities, as well as its ability to take on unique, difficult, and critical projects that demand strict adherence to codes.
Specializing in short-run, quick-turnaround prototype and R&D work for the aerospace, military, pharmaceutical, and oil and gas industries, just to name a few, the 34-year-old company relies heavily on highly intelligent and skilled workers and machine tools that are on par with current technology, which allow it to live up to its promise to deliver quality work in a timely fashion.
Mike Kartsonis, president and owner of Dynamic Fabrication, said he initially intended the company to be a specialty welding firm but wound up expanding by accident.
“I found out I needed something machined so I’d have to wait a couple of weeks for it to get done. I needed it faster than that, so I bought a little mill and a little lathe and saw and a brake and a shear, roll, punch, tube bender. I bought my first building in 1996 and then my second in 2002,” Kartsonis explained.
Since then he’s made continuous investments in equipment and personnel, the latter being crucial to the company’s growth and success.
“The key is the people. I can bring in as much work as I want, but if they can’t do it in a timely manner, it doesn’t make much sense. I have a great team of people that work well together. Nobody works for me; everyone works with me.”
Without an incredibly intelligent and fabrication-saavy staff, the company would have no business working on critical components belonging to aerospace and defense projects and welding to strict codes that include AWS D1.1, D1.2, D14.1, and D17.1
Practical Welding Today® spoke to Kartsonsis about his business, what it’s like juggling such a variety of projects, and what his concerns are presently and moving forward.
PWT: What are the main challenges affecting your business presently?
Skilled labor. It’s been an ongoing problem for many years. We do have an in-house training program, and the manufacturing association I belong to has a couple of training centers that we utilize, but it’s an ongoing issue and one of the biggest we face.
PWT: To what do you attribute that?
I’m 60 years old. My generation grew up working with their hands and it wasn’t as much of a disposable society as it is now. Today people just throw things away, whereas my generation had to fix things. The kids aren’t exposed to, for example, building a go-kart, working on a car, or fixing the lawn mower.
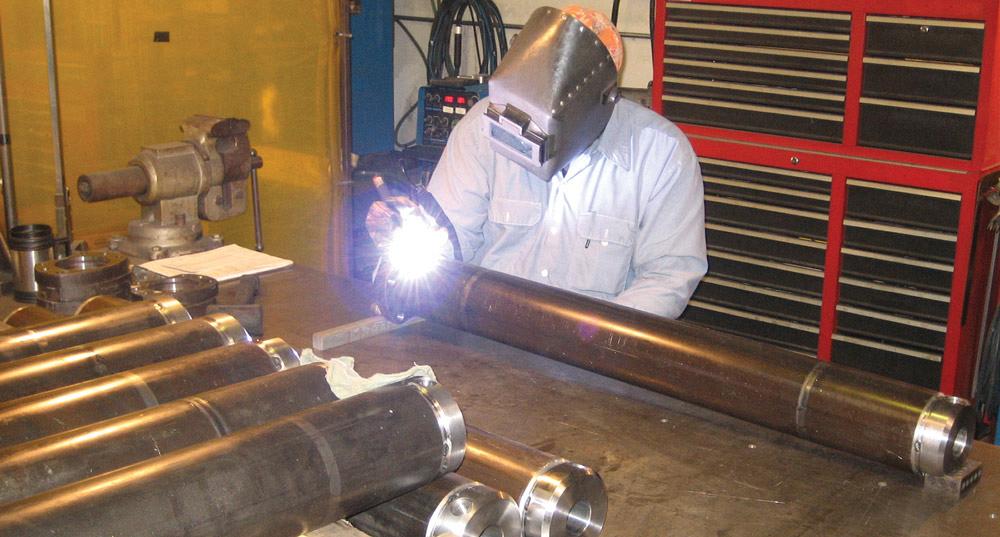
Kartsonis said welders and fabricators at Dynamic Fabrication possess tribal knowledge about manufacturing, how things can be made, and what to expect due to years of experience.
I’ve started a scholarship program for advanced machining training. I donated a fair amount of money to help kids. We have an ongoing mentoring program where we’ve hired kids who have come to work for us doing some deburring and emptying of the trash and now are doing machining and setting up their brake, shear, roll, punch, things like that. That’s exciting to see the kids find a career, something they’re passionate about, and something they enjoy.
The problem is most of the people—the good guys—who have jobs stay put, especially if it’s a good place to work. The good guys aren’t out looking for jobs.
I’m lucky, though, because I’ve got some guys who are in the top 1 percent as far as skills go.
PWT: What qualities put your workers into that 1 percent, in your opinion?
They possess a lot of tribal knowledge—things like understanding manufacturing, how things can be made, and what to expect. If you were to equate that with an experienced baker, for example, they would know when to use two eggs instead of four eggs and why. In the same way our guys just know material and how it will react or warp. They know when to weld it with a bend in it because they know it will warp back to flat, things like that. It’s tribal knowledge and experience.
PWT: How important is that tribal knowledge when it comes to working with exotic metals?
The thing with the exotic metals is that the warpage and the distortion vary. You have your different melting points to control heat.
Let’s say, for example, we have to make a tube out of titanium that is a special diameter, let’s say 10.172 in. in 1⁄16 gauge. We have to roll it to maybe 4 in., but it has such a springback and memory that it’ll come back to 10 in. So say if you want to bend something at 90 degrees, you bend it to 45 and it bends back to 90.
So the exotic metals pose more difficulty because they are harder and tougher because of the nickel they have in them and just the memory that they have. We work with INCONEL®,
Hastelloy®, titanium, magnesium, Invar®, all the so-called exotics. You just have to be careful and know what you’re doing or else you could scrap a part that’s anywhere from $5,000 to $20,000 easy.PWT: What are some of the rigors your company faces when welding and fabricating components for military contracts?
The tolerances that we have to meet are getting tighter and tighter, especially on sheet metal and weldments with machine tolerances of ± 0.005, ± 0.010 on, say, an aluminum bent piece that is 0.030 and has three bends in it.
Also, sometimes we run into situations where we’re given a part design that is incredibly difficult to manufacture. Some of the parts that are being designed today are pretty complex, so we’ll call them up and say, “I can’t hold this,” or when we’re quoting it we’ll ask, “Hey, why are you doing it like this?” and we help them out with a little bit of a design review.
PWT: Can you explain the AWS D17.1 certification for aerospace work and why it’s so difficult to navigate?
The standard itself is about 70 pages long and touches on everything from the calibration of your welding machine and all of your gauges to the certification and control of your welding wire, to your welders, and to the need for eye examinations and continuous training.
If we want to certify to AWS D17.1 in 6061 aluminum, for example, and I have a 1-in.-thick plate I have to weld, I have to make sure that the test I certify to is around 1 in. thick. They’ll give me a range that I can weld within—as thin as ½ in. thick and as thick as 2 in. Even though I am testing on a 1-in. coupon, I can go up to maybe 2 or 3 in. thick to maybe ½ in. thick. You have a range.
If I have certification in 1 in. but I want to weld something 1⁄8 in. thick, I’d have to retest and recertify for that. Whether it’s a butt weld or a fillet weld, you have to retest for each of those. A lot of it has to do with the porosity in the weld. Sometimes they’ll allow only 0.002 of porosity for every ½ in. Sometimes they don’t allow for any porosity at all.
About the Author
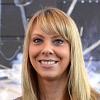
Amanda Carlson
2135 Point Blvd
Elgin, IL 60123
815-227-8260
Amanda Carlson was named as the editor for The WELDER in January 2017. She is responsible for coordinating and writing or editing all of the magazine’s editorial content. Before joining The WELDER, Amanda was a news editor for two years, coordinating and editing all product and industry news items for several publications and thefabricator.com.
About the Publication
subscribe now
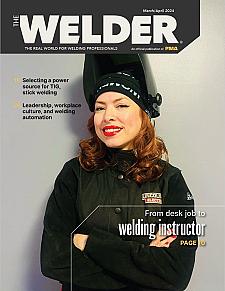
The Welder, formerly known as Practical Welding Today, is a showcase of the real people who make the products we use and work with every day. This magazine has served the welding community in North America well for more than 20 years.
start your free subscription- Stay connected from anywhere
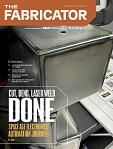
Easily access valuable industry resources now with full access to the digital edition of The Fabricator.
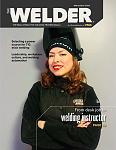
Easily access valuable industry resources now with full access to the digital edition of The Welder.
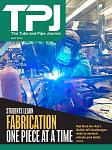
Easily access valuable industry resources now with full access to the digital edition of The Tube and Pipe Journal.
- Podcasting
- Podcast:
- The Fabricator Podcast
- Published:
- 04/16/2024
- Running Time:
- 63:29
In this episode of The Fabricator Podcast, Caleb Chamberlain, co-founder and CEO of OSH Cut, discusses his company’s...
- Trending Articles
Sheffield Forgemasters makes global leap in welding technology
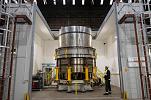
ESAB unveils Texas facility renovation
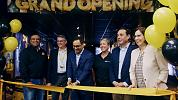
Engine-driven welding machines include integrated air compressors
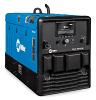
How welders can stay safe during grinding
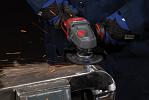
The impact of sine and square waves in aluminum AC welding, Part I
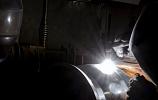
- Industry Events
16th Annual Safety Conference
- April 30 - May 1, 2024
- Elgin,
Pipe and Tube Conference
- May 21 - 22, 2024
- Omaha, NE
World-Class Roll Forming Workshop
- June 5 - 6, 2024
- Louisville, KY
Advanced Laser Application Workshop
- June 25 - 27, 2024
- Novi, MI