AWS CWI, CWE, NDE Level III
- FMA
- The Fabricator
- FABTECH
- Canadian Metalworking
Categories
- Additive Manufacturing
- Aluminum Welding
- Arc Welding
- Assembly and Joining
- Automation and Robotics
- Bending and Forming
- Consumables
- Cutting and Weld Prep
- Electric Vehicles
- En Español
- Finishing
- Hydroforming
- Laser Cutting
- Laser Welding
- Machining
- Manufacturing Software
- Materials Handling
- Metals/Materials
- Oxyfuel Cutting
- Plasma Cutting
- Power Tools
- Punching and Other Holemaking
- Roll Forming
- Safety
- Sawing
- Shearing
- Shop Management
- Testing and Measuring
- Tube and Pipe Fabrication
- Tube and Pipe Production
- Waterjet Cutting
Industry Directory
Webcasts
Podcasts
FAB 40
Advertise
Subscribe
Account Login
Search
Why welders need advanced training
- By Professor R. Carlisle "Carl" Smith
- July 10, 2007
- Article
- Arc Welding
Welding trade publications are loaded with headlines proclaiming, "Critical welder shortage!" This fact is undeniable, but we need to add, "Many welders are undertrained!"
Vocational schools (now referred to as technical centers) do a good job with hands-on training. (I need to say as an aside that alltraining is vocational training. I am not ashamed to be a product of a vocational school!)
Vocational centers in West Virginia, my home state, were established in the 1960s through the efforts of then Gov. Arch A. Moore Jr. and Sen. Robert C. Byrd, who was a shipyard welder.
Young instructors generally are enthusiastic in the shop and do their best to train and encourage the students. But we are rapidly losing welding instructors from the "old school." These instructors not only were dedicated to their profession, but were deeply concerned with producing students of whom they could be proud. Old-school instructors now are at retirement age, although many of them are still working for the love of teaching.
Young instructors have not been able to receive the technical training that was afforded old-school instructors in the early days of vocational training programs. State department budgets for technical and industrial education have been reduced over the years to the point that very few instructors are able to attend summer sessions at Hobart, Lincoln, or community colleges. For several years West Virginia University at Parkersburg offered summer seminars in metallurgy, nondestructive testing, welding inspection, and state-of-the-art equipment. Now it seems that computer training has captured the bulk of the budgets.
While attending an American Welding Society (AWS) Education Committee meeting in Miami, I discovered that the problem of limited training for instructors is not just in West Virginia, but nationwide. Student competence is directly affected by the instructor's knowledge base.
Industry complains about the limited knowledge of welding school graduates, but not loudly enough. The complaints usually are that the welder has good hands-on skills, but can't read drawings or specifications well enough to work independently in the shop. Many welding supervisors are reporting that students have very little metallurgical knowledge or the ability to determine the weld requirements by looking at the drawings, specifications, and welding procedures. Supervisors would like to be able to hand the welder a drawing, specification, and a welding procedure and depend on the welder to do the job.
Welding Sustains Our Infrastructure
The educational system as a whole seems to be unaware that a very large portion of our infrastructure depends on the welding industry for maintenance and construction. The education systems need to lend an ear to the industry's advisory committees to determine the training needs.
What Are the Needed Training Areas?
Secondary Training. Of course, hands-on training is extremely important. Proper techniques must be presented to the students for each process and its variations. Various modes of transfer in the GMAW processes require different travel angles and work angles for the torch or electrode. The shielding gas also determines whether a pushor dragtravel angle should be used.
Different methods of applying filler material for the GTAW process must be taught. For some materials, the laymethod along with walking the cupshould be used. For welding aluminum or titanium, the dippingmethod is most common.
The correct polarity and the amperage and voltage requirements to use with each type of electrode should be learned at this stage. How to set up the equipment for each process should be taught at the beginning of training. These are just a few of the hands-on techniques that often are not presented to the student.
Postsecondary Training (Community Colleges). Students need to understand the welding detailportion of a drawing. They must learn which side to weld and exactly where to place the weld. Knowledge of welding symbols is an absolute. One of the most common questions apprentice welders ask is related to the weld size for a groove weld that has no size on the symbol. The student needs to know that this means it is a complete joint penetration weld (CJP). Another area of confusion is with the staggered, intermittent weld. Where does it start and stop?
Students are rarely introduced to welding procedure specifications. The WPS may be the most important document that the welder receives when a job commences, and it must be a part of the curriculum. The applicable code reference, process, base material, filler metal requirements, electrical characteristics, techniques, preheat requirements, and gas mixtures are determined by consulting this document.
The various codes also should be presented to students, at least to show them how to read the sometimes complicated sections. In some cases, the customer specification makes reference to a code section. For example, the minimum weld length for a stitch (intermittent) weld may not be called out on a drawing, so AWS Structural Code D1.1, para. 2.3.2.4 must be consulted for determining the length.
Metallurgy is an essential component of any welding curriculum. The welder doesn't need to acquire the knowledge base of a metallurgist, but a course in basic welding metallurgyis essential. A welder needs to know what takes place when a stainless alloy is overheated and a chromium-molybdenum alloy (or any quenched and tempered steel) is not properly preheated. The AWS textbook Basic Welding Metallurgyis good, and Lincoln's Metals and How to Weld Themalso is very basic and an easy read. The authors, Duane K. Miller and Omar Blodgett, respectively, are excellent teachers.
Every postsecondary institution should have a set of codes and a set of AWS Welding Handbooks, which were compiled by Harvey Castner from the Edison Welding Institute.
Every student should be encouraged to join appropriate trade associations, such as AWS, and attend meetings. The associations provide a wealth of information, and some offer scholarships for those who qualify. Many of my students have secured jobs through their association with companies at AWS meetings.
Last, but not least, the welder needs to learn to be a welding inspector. Knowing the difference between an acceptable and unacceptable weld is a part of the welder's job. The use of fillet gauges and other weld gauges (for undercut, bead height, etc.) should be taught. AWS's Visual Inspection Workshopand Guide for Visual Inspection of Weldsare excellent resources.
The topics covered in this article are the minimum essentials for welding training. The hands-on portion must be taught in the secondary institutions, and the technology portion in the community colleges or other postsecondary institutions.
About the Author
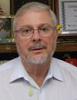
Professor R. Carlisle "Carl" Smith
Weld Inspection & Consulting
PO Box 841
St. Albans, WV 25177
304-549-5606
About the Publication
subscribe now
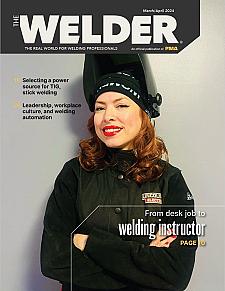
The Welder, formerly known as Practical Welding Today, is a showcase of the real people who make the products we use and work with every day. This magazine has served the welding community in North America well for more than 20 years.
start your free subscription- Stay connected from anywhere
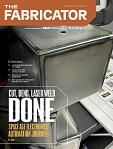
Easily access valuable industry resources now with full access to the digital edition of The Fabricator.
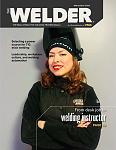
Easily access valuable industry resources now with full access to the digital edition of The Welder.
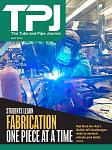
Easily access valuable industry resources now with full access to the digital edition of The Tube and Pipe Journal.
- Podcasting
- Podcast:
- The Fabricator Podcast
- Published:
- 04/30/2024
- Running Time:
- 53:00
Seth Feldman of Iowa-based Wertzbaugher Services joins The Fabricator Podcast to offer his take as a Gen Zer...
- Industry Events
Pipe and Tube Conference
- May 21 - 22, 2024
- Omaha, NE
World-Class Roll Forming Workshop
- June 5 - 6, 2024
- Louisville, KY
Advanced Laser Application Workshop
- June 25 - 27, 2024
- Novi, MI