Senior Process Engineer, Technology Advancement Team
- FMA
- The Fabricator
- FABTECH
- Canadian Metalworking
Categories
- Additive Manufacturing
- Aluminum Welding
- Arc Welding
- Assembly and Joining
- Automation and Robotics
- Bending and Forming
- Consumables
- Cutting and Weld Prep
- Electric Vehicles
- En Español
- Finishing
- Hydroforming
- Laser Cutting
- Laser Welding
- Machining
- Manufacturing Software
- Materials Handling
- Metals/Materials
- Oxyfuel Cutting
- Plasma Cutting
- Power Tools
- Punching and Other Holemaking
- Roll Forming
- Safety
- Sawing
- Shearing
- Shop Management
- Testing and Measuring
- Tube and Pipe Fabrication
- Tube and Pipe Production
- Waterjet Cutting
Industry Directory
Webcasts
Podcasts
FAB 40
Advertise
Subscribe
Account Login
Search
How to operate a robotic welder: Uniting welders and robots
4 reasons skilled welders make the best robotic welding operators
- By Jack Moore
- Updated May 9, 2023
- July 22, 2020
- Article
- Automation and Robotics
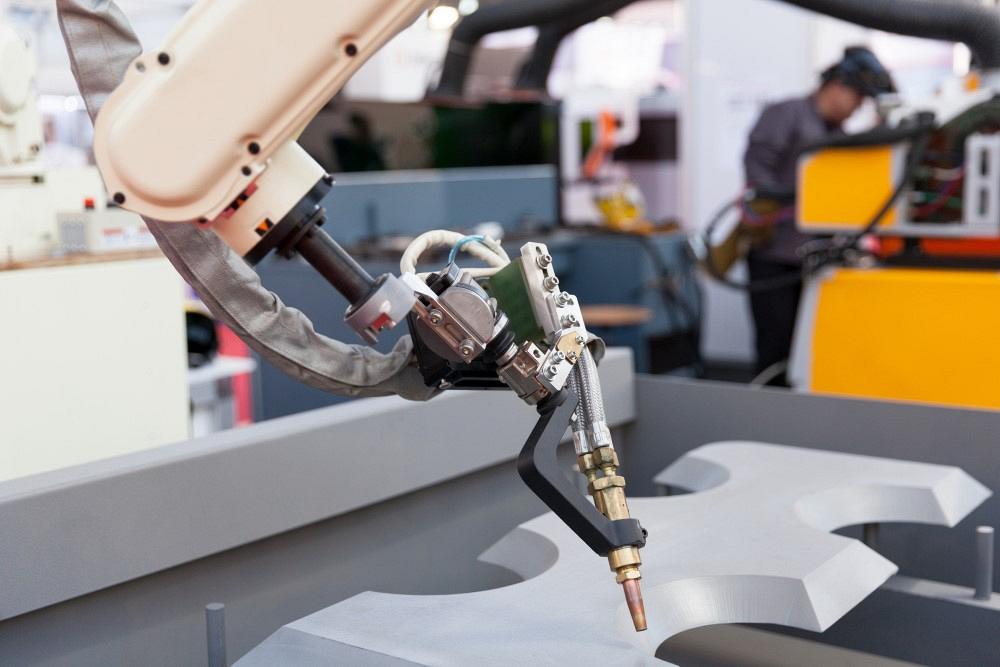
Putting your robotic welding operation in the hands of a skilled and experienced welder offers several benefits by combining the best attributes of both man and machine. Getty Images
Skilled welders capable of handling multiple weld processes are becoming a rare commodity. In fact, the American Welding Society projects a shortage of over 375,000 skilled welding professionals who fabricate 50% of all handmade products that require some form of welding by 2023. This shortage not only affects goods that are created manually, it also affects those welded with robotic automation because the most talented welders make the best robot programmers.
While advanced robotic welding technology makes it easier for manufacturers to tackle difficult, dangerous, and dirty jobs, having a skilled welder on hand to champion the process is what makes implementation and programming successful.
No. 1: It’s Easier to Teach a Welder How to Program a Robot Than It Is to Teach a Programmer How to Weld
It’s common in the robotic welding industry to hear someone say that it’s a lot easier to teach a person how to program a robot than it is to teach them how to weld and fabricate. It takes less time to learn robot controller basics than to learn a welding process with all its variables and subtle adjustments of control parameters. Thus, it’s often more efficient to take skilled welders equipped with years of invaluable knowledge they’ve amassed while on the job and teach them how to program a robot, rather than teach robot technicians welding processes.
Keep in mind, robotic welding can accommodate multiple types of welding processes, with some being more difficult to support than others, especially from a quality standpoint. For applications and processes that are found to be extremely challenging, having a robot technician with extensive welding expertise can increase throughput and optimize weld quality dramatically, while providing long-term weld system support for greater efficiency.
No. 2: Skilled Welders Understand Process Variables in Robotic Welders
Producing welded assemblies successfully requires knowledge of part variability, weld torch positioning, heat input, and travel speed. These variables are equally essential in robotic applications, but they must be communicated by an operator to the robot control.
A welder’s experience provides this knowledge, making him or her the ideal candidate to program a robot. In fact, many see robotic weld programming as cloning the know-how from the best welders in the industry. Furthermore, leveraging a manual welder’s process expertise can greatly reduce the time it takes to create a new weld program. Skilled welders can influence the robotic welding process in a variety of ways.
- Part Fit-up. As parts are fed from one step of the manufacturing process to the next, they tend to vary in size and shape. These variations can require changes in weld torch position, welding power supply settings, and weld speed or torch oscillation. As these parts are fed to the welder, he or she can automatically adjust the weld process in real time to adapt to these changes in fit-up.
With regards to robotic welding, knowing how parts fit together and understanding where and by how much the process needs to be adapted are critical pieces of information to apply to the robot system. Adjusting welding parameters (specified by the procedure) and accurately deploying robot sensing technologies all require this knowledge, which stems from an experienced welder.
- Robot Path Programming. Many manufacturing facilities supply the welder with a specification of welding conditions to follow for each weld type or location on the part. These specifications define how much the welder can alter the welding parameters to adapt to changes in the to be welded structure. Some areas on the part may require changes to weld torch positioning (in the weld joint) or torch angles.
When applied to a robot system, these nuggets of application knowledge can maximize robotic weld quality and production volumes. Weld defects, distortion concerns, and rework also can be addressed.
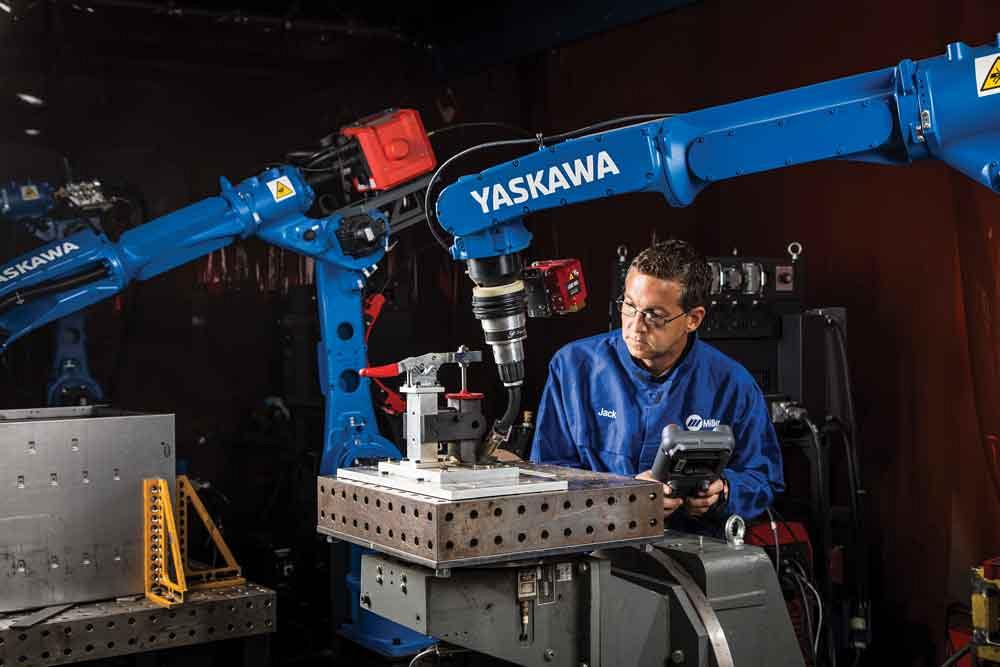
Skilled welders harbor a wealth of application knowledge that they can apply to the successful utilization of a robotic welding workcell, optimizing weld quality and maximizing production volumes.Yaskawa America Inc., Motoman Robotics Division
- Weld Sequencing. To create welded assemblies with the required dimensions, welders typically require a thorough understanding of weld sequencing, or the order in which welds are made. Often this type of knowledge is obtained on the manual welding line where workers are tasked with creating assemblies by fitting subassemblies together.
Not only do these individuals see where assembly problems lie, they are equipped with the skill set to fix problems that surface by manipulating the weld conditions and sequencing, along with other variables that are critical to saving valuable time.
No. 3: Skilled Welders Know an Application’s Equipment Needs
When a fabricator is procuring and configuring a new robot system, it is not uncommon for the intended robot operator to be involved in the decision-making process for these equipment setup variables. Programming a robot and its subsequent weld equipment accurately and efficiently requires a full understanding of all critical variables. As an example, process variables for the gas metal arc welding (GMAW) process include wire size, shielding gas composition, power supply operating mode, current, voltage, wire oscillation, travel speed, and torch angles.
For this reason, it can be beneficial to tap the knowledge of a seasoned welder to procure the best equipment for the robotic welding application. Moreover, selecting weld equipment with the help of a veteran welder often results in fewer short-term costs through improved weld quality and production rates, as well as long-term costs through process consistency and improved ROI.
Similarly, when encountering process challenges such as achieving production rate targets, coping with part inconsistencies, reducing part rework, and obtaining weld cosmetics goals, an experienced welder can pull from his or her arsenal of tricks of the trade to adjust parameters as needed.
No. 4: One Skilled Welder Can Influence Multiple Robotic Welders
Each year fewer people enter the welding trade, which means there are fewer people with adequate weld skills to support the demands of the manufacturing sector. To maximize the welders that currently work in general industry fields, it only makes sense to apply their knowledge to robotic welding workcells to meet demand. The wealth of knowledge that they possess can be applied to welding robots to facilitate more applications than would be possible with only manual welding skills and worker availability.
Today one welder can influence multiple welding robots that run multiple shifts per day. Therefore, one welder’s knowledge can affect a dozen or more welding applications. Between increased production rates (robots often weld at higher production speeds than manual welders), increased uptime (robots don’t take breaks), increased daily production volume (robots can work longer hours and for multiple shifts each day), and increased weld quality (the skill of an experienced welder can be applied to multiple robots), the valuable know-how of a skilled welder can be applied with maximum benefit via a welding robot system.
Robotic Welders Mitigate Hazardous Environment
The reality of many welding environments is that they are not climate-controlled. This, combined with the need for welders to clothe themselves in protective gear (jacket, helmet, gloves) and the heat emitted from newly welded parts, can increase the risk for heat-related illnesses. In addition, some welding applications produce hazardous fumes, requiring welders to wear specialty helmets that can make them more susceptible to dehydration. In some extreme situations, welders must work inside metal envelopes or tubes with poor air circulation.
On the flip side, robotic welding can be adapted to perform in many of these applications, allowing welders to use their expertise without placing them in physically challenging and potentially harmful environments.
About the Author
About the Publication
subscribe now
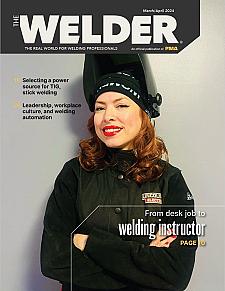
The Welder, formerly known as Practical Welding Today, is a showcase of the real people who make the products we use and work with every day. This magazine has served the welding community in North America well for more than 20 years.
start your free subscription- Stay connected from anywhere
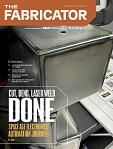
Easily access valuable industry resources now with full access to the digital edition of The Fabricator.
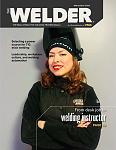
Easily access valuable industry resources now with full access to the digital edition of The Welder.
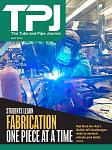
Easily access valuable industry resources now with full access to the digital edition of The Tube and Pipe Journal.
- Podcasting
- Podcast:
- The Fabricator Podcast
- Published:
- 04/16/2024
- Running Time:
- 63:29
In this episode of The Fabricator Podcast, Caleb Chamberlain, co-founder and CEO of OSH Cut, discusses his company’s...
- Trending Articles
Sheffield Forgemasters makes global leap in welding technology
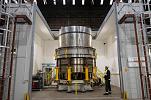
ESAB unveils Texas facility renovation
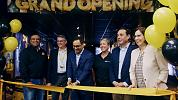
Engine-driven welding machines include integrated air compressors
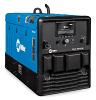
How welders can stay safe during grinding
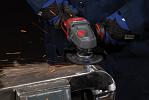
The impact of sine and square waves in aluminum AC welding, Part I
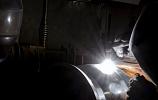
- Industry Events
16th Annual Safety Conference
- April 30 - May 1, 2024
- Elgin,
Pipe and Tube Conference
- May 21 - 22, 2024
- Omaha, NE
World-Class Roll Forming Workshop
- June 5 - 6, 2024
- Louisville, KY
Advanced Laser Application Workshop
- June 25 - 27, 2024
- Novi, MI