Senior Product Manager Welding
- FMA
- The Fabricator
- FABTECH
- Canadian Metalworking
Categories
- Additive Manufacturing
- Aluminum Welding
- Arc Welding
- Assembly and Joining
- Automation and Robotics
- Bending and Forming
- Consumables
- Cutting and Weld Prep
- Electric Vehicles
- En Español
- Finishing
- Hydroforming
- Laser Cutting
- Laser Welding
- Machining
- Manufacturing Software
- Materials Handling
- Metals/Materials
- Oxyfuel Cutting
- Plasma Cutting
- Power Tools
- Punching and Other Holemaking
- Roll Forming
- Safety
- Sawing
- Shearing
- Shop Management
- Testing and Measuring
- Tube and Pipe Fabrication
- Tube and Pipe Production
- Waterjet Cutting
Industry Directory
Webcasts
Podcasts
FAB 40
Advertise
Subscribe
Account Login
Search
Three benefits of robotic welding
Why even small metal fabrication shops can benefit from robotic automation
- By Josh Leath
- Updated May 9, 2023
- October 14, 2021
- Article
- Automation and Robotics
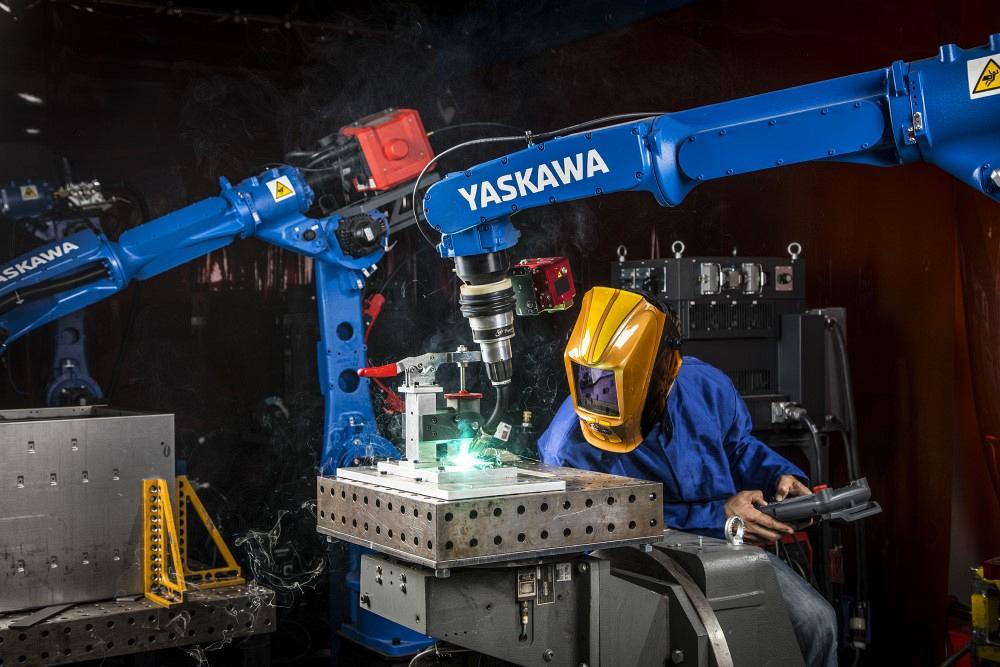
Trained welders are excellent at spotting poor welds, which is why having an experienced set of eyes operating your robot to catch any faults is highly beneficial. Yaskawa America Inc.
If you’re worried about maintaining your current welding workforce, you’re not alone. It’s an ongoing struggle for most manufacturers as new industry growth, a rapidly aging welder population, and a lack of new talent have created a skilled worker chasm that seems nearly impossible to fill.
In fact, the American Welding Society projects a shortage of over 400,000 skilled welding professionals by 2024. This shocking truth has permeated the industrial culture, causing low morale for some stretched thin from working diligently to help fabricate the 50% of products that require some form of welding.
While still highly important, traditional recruitment methods are insufficient to provide the total number of welders needed to maintain the level of production required to meet today’s stringent market demands. Manufacturers are realizing the best way to tackle their workforce shortage dilemmas and boost current employee morale is by embracing a strategic mix of highly adopted technologies and robotic automation combined with human talent. As a result, decision-makers are implementing robots and peripheral technologies introduced via Industry 4.0 to optimize production and build a competitive edge.
Benefits of Robotic Welding
To suggest that all manufacturers view robotic automation as a wonderful thing would be a gross assumption. That said, there are undeniable advantages that those on the decision-making fence may find helpful. In fact, those manufacturers worried about losing skilled welders due to worker burnout or displacing current employees as a result of new technology will most likely find reassurance in that using robotic automation in no way replaces the skill and experience of a manual welder. Instead, robotics allows those individuals to focus their time and energy on complex projects that require skill, creativity, and problem-solving abilities.
1. Robots Allow Welders to Perform Difficult, One-Off Welds. One robot is generally as productive as 2½ welders with arc-on time, which is why many companies find that adding a robotic workcell is enough to help optimize operations. Usually equipped with one or two arc welding robots, a robust weld package, and peripheral technology for seam tracking, today’s robotic welding systems are a cost-effective way to integrate robotics into your welding processes.
The benefits of adopting robotic welding include maintaining production schedules and performing welds for high-volume runs, freeing up workers to focus on high-value tasks. Performing basic welds over and over can become redundant, often leading to employee boredom, burnout, and occasionally ergonomic injury. Implementing robots that allow skilled workers to take on other tasks such as short runs or custom fabrication for specialty orders is a win-win.
2. Robotic Welding Creates New Job Opportunities for Experienced Welders. Having a robot means you also need someone on staff who can operate and program it. For welding applications, retraining and redeploying a skilled welder for this task is ideal. After all, welders understand how filler metals, welding parameters, torch angles, materials, and shielding gas affect the overall weld itself. Plus, a welder has prior experience in creating uniform welds, mitigating spatter, reducing porosity, preventing undercut, and achieving the specified aesthetics.
While intelligent tools are available to help robotic programmers with these concepts, having prior knowledge of them makes the programming process easier to learn, it speeds up the integration process, and it results in less downtime between changeovers for greater throughput and faster return on investment.
Finally, trained welders are excellent at spotting poor welds. Things like part changeover, bad tooling, or even a poorly done “touchup” can affect weld quality and integrity. Having an intuitive welder with an experienced set of eyes to catch these faults is extremely beneficial.
3. Robotic Welding Helps You Stay Competitive. Not only can robots help increase product quality, they can boost product throughput – two things that often facilitate a competitive edge. Typically, high-throughput shops that take on more orders require dedicated personnel to handle increased activity and sometimes must hire new employees to meet demand.
From sales and finance to manufacturing and shipping, many departments are tasked with heavier workloads. Decision-makers who embrace robotic automation can use it to help address high-throughput needs and use resources to invest in long-term employees instead of always hiring from temp agencies.
Automated Welding Processes for Long-term Success
Whether your shop employs an arc welding, spot welding, or material handling robot, for that matter, the use of robotic arms on the shop floor can create unique opportunities, especially for welding professionals. Savvy business leaders with a solid, well-communicated implementation plan often find that robots allow manual workers to focus on tasks that are more in line with their specific skill sets.
Placing your skilled workers in positions that allow them to showcase their talents while relying on robotic welding technology to perform the more mundane tasks increases employee morale, optimizes product quality, and increases part throughput, leading to a more competitive company in the long run. As mentioned, jobs that typically are created from robotic implementation and utilization include robot programmers and operators. Robotic technicians, tooling engineers, and control engineers are other positions that frequently evolve, opening the doorway for rewarding opportunities for your current employees.
About the Author
Josh Leath
100 Automation Way
Miamisburg, OH 45342
(937)-847-6200
About the Publication
subscribe now
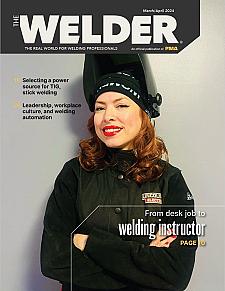
The Welder, formerly known as Practical Welding Today, is a showcase of the real people who make the products we use and work with every day. This magazine has served the welding community in North America well for more than 20 years.
start your free subscription- Stay connected from anywhere
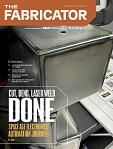
Easily access valuable industry resources now with full access to the digital edition of The Fabricator.
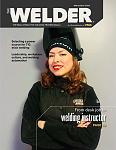
Easily access valuable industry resources now with full access to the digital edition of The Welder.
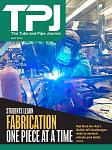
Easily access valuable industry resources now with full access to the digital edition of The Tube and Pipe Journal.
- Podcasting
- Podcast:
- The Fabricator Podcast
- Published:
- 04/16/2024
- Running Time:
- 63:29
In this episode of The Fabricator Podcast, Caleb Chamberlain, co-founder and CEO of OSH Cut, discusses his company’s...
- Trending Articles
Sheffield Forgemasters makes global leap in welding technology
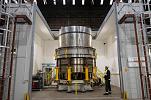
ESAB unveils Texas facility renovation
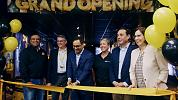
Engine-driven welding machines include integrated air compressors
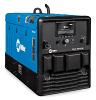
The impact of sine and square waves in aluminum AC welding, Part I
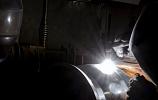
How welders can stay safe during grinding
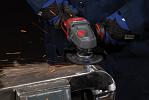
- Industry Events
16th Annual Safety Conference
- April 30 - May 1, 2024
- Elgin,
Pipe and Tube Conference
- May 21 - 22, 2024
- Omaha, NE
World-Class Roll Forming Workshop
- June 5 - 6, 2024
- Louisville, KY
Advanced Laser Application Workshop
- June 25 - 27, 2024
- Novi, MI