Independent welding consumables professional
- FMA
- The Fabricator
- FABTECH
- Canadian Metalworking
Categories
- Additive Manufacturing
- Aluminum Welding
- Arc Welding
- Assembly and Joining
- Automation and Robotics
- Bending and Forming
- Consumables
- Cutting and Weld Prep
- Electric Vehicles
- En Español
- Finishing
- Hydroforming
- Laser Cutting
- Laser Welding
- Machining
- Manufacturing Software
- Materials Handling
- Metals/Materials
- Oxyfuel Cutting
- Plasma Cutting
- Power Tools
- Punching and Other Holemaking
- Roll Forming
- Safety
- Sawing
- Shearing
- Shop Management
- Testing and Measuring
- Tube and Pipe Fabrication
- Tube and Pipe Production
- Waterjet Cutting
Industry Directory
Webcasts
Podcasts
FAB 40
Advertise
Subscribe
Account Login
Search
Consumables Corner: Addressing penetration problems in stainless steel SAW
- By Nino Mascalco, Rob Koltz, and Steve Sigler
- September 22, 2017
- Article
- Consumables
We manufacture carbon and stainless steel tanks using flux-cored arc welding (FCAW) and gas metal arc welding (GMAW). Recently we purchased a submerged arc welding (SAW) system for increased weld deposition but we are having a difficult time attaining a full-penetration weld without backgouging. We typically weld ½-in. material with a 1/4-in. deep, 45-degree V-groove joint and no root opening with a single 3/32-in. dia. wire. We've had some success with the carbon steel, but the stainless steel is giving us a lot of problems. Any recommendations?
There are a number of reasons this may be happening, but if material thickness, joint design, and weld parameters are all correct, then the likely reason is that stainless steel has higher resistance to heat transfer. Let's take a look at some important factors in this application.
Typical complete-joint-penetration (CJP) welds are most easily attained by backgouging to the weld metal on the other side of the joint. However, this is not the most economical or operator-friendly way depending on the available equipment your shop may have.
The variables that could be individually or jointly affecting your ability to gain fullpen welds are:
- Weld parameters, such as amperage, voltage, electrode stick out (ESO) or contact-tip-to-work distance (CTWD), and travel speed.
- Heat input.
- Torch work and travel angles.
- Bevel and opening depth.
- Root face.
- Root opening.
- Wire placement in joint.
Basic concepts like maintaining a consistent bevel depth or root face are key to being successful and repeatable. Also, wire placement in the middle of the joint is key to delivering full-penetration welds consistently.
From a welding parameter standpoint, amperage is the electrical energy that provides penetration, however voltage is the largest contributor to penetration. Voltage controls the arc length, so a lower voltage provides a more focused and concentrated welding arc, delivering more penetration. To visualize this relationship, arc length is the point at which the wire melts and the arc cone (think of a funnel turned upside down) begins and is measured to the surface of the molten weld puddle. With a specific amperage, if you increase voltage the arc cone will increase proportionally and create a larger surface area weld puddle, this will reduce the energy per unit area for that amperage and reduce penetration. Higher amperage means a higher wire burnoff rate, leading to a higher weld deposition rate. But sometimes this can cause the molten weld puddle to run in front of the arc, resulting in lack of fusion (LOF). Also, we must realize than the burnoff rate for carbon steel is different than for stainless steel wires for the same amperage. This could be a contributing factor in your inconsistent results with stainless steel as compared to carbon steel.
ESO is important because if it is excessive, there is too much preheating in the electrode, which degrades penetration ability. The rule of thumb for SAW is a stick-out that is the equivalent to eight times the wire diameter. For your setup, that equates to 0.75 in. ± 1/8 in. Once a procedure is developed, it is important to keep the ESO constant.
Travel speed also affects weld penetration. Moving too fast results in low penetration, while moving too slow could allow the molten weld puddle to run in front of the welding arc, preventing penetration. Slow travel speed is also one of the main reasons for slag (or unfused flux) entrapment.
Weld heat input is a mathematical equation that measures the amount of energy put into a weld joint. The formula is defined as:
Volts x Amps x 60/Travel speed (IPM) = Joules/in.
For stainless steel, the rule of thumb for the maximum heat input is 50,000 joules/in. to prevent degrading the corrosion resistance of the base material’s heat-affected zone (HAZ). If the tanks are circular, then torch position, with respect to top dead center (TDC) or bottom dead center (BDC) on the circular welds, is important as well. When welding on the outer circular welds, the torch should be located with a slight downhill angle, so as the tank turns, the weld puddle solidifies near the 12 o'clock position. The inside welds should be slightly uphill to allow the weld puddle to solidify near the 6 o'clock position.
If all of the aforementioned variables hit a correct operating window and you still are having problems, then you may have to make some adjustments to the weld joint design. Simply changing the joint design to a double V-groove with an approximate 4-mm root face would allow the arc to penetrate adequately. This option largely depends on your capabilities for joint beveling. If you have to perform more material handling, such as turning the plate to bevel the opposite side, this may be more time-consuming and even less safe compared to backgouging.
Increasing the bevel angle to allow more access for the electrode to target the bottom of the joint may help. Increasing the depth of the bevel will reduce the root face and amount of base material the welding arc has to penetrate on the back side. Keep in mind, both of these options will increase the amount of weld metal required to fill the joint and may cause other issues, like distortion.
Overall, take a close look at your capabilities and even perform some time and safety studies to determine which variable adjustments make the most economic sense.
About the Authors
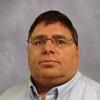
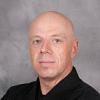
Rob Koltz
Application Engineer
411 S. Ebenezer Rd.
Florence, 29501
636-485-2253
Steve Sigler
Application Engineer
411 S. Ebenezer Rd.
Florence, South Carolina 29501
636-485-2253
About the Publication
Related Companies
subscribe now
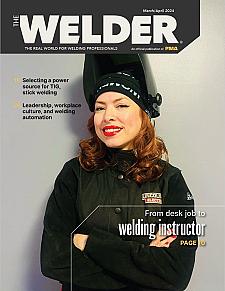
The Welder, formerly known as Practical Welding Today, is a showcase of the real people who make the products we use and work with every day. This magazine has served the welding community in North America well for more than 20 years.
start your free subscription- Stay connected from anywhere
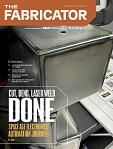
Easily access valuable industry resources now with full access to the digital edition of The Fabricator.
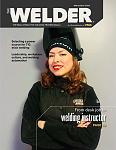
Easily access valuable industry resources now with full access to the digital edition of The Welder.
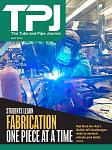
Easily access valuable industry resources now with full access to the digital edition of The Tube and Pipe Journal.
- Podcasting
- Podcast:
- The Fabricator Podcast
- Published:
- 04/16/2024
- Running Time:
- 63:29
In this episode of The Fabricator Podcast, Caleb Chamberlain, co-founder and CEO of OSH Cut, discusses his company’s...
- Industry Events
16th Annual Safety Conference
- April 30 - May 1, 2024
- Elgin,
Pipe and Tube Conference
- May 21 - 22, 2024
- Omaha, NE
World-Class Roll Forming Workshop
- June 5 - 6, 2024
- Louisville, KY
Advanced Laser Application Workshop
- June 25 - 27, 2024
- Novi, MI