Technical Liaison Manager
- FMA
- The Fabricator
- FABTECH
- Canadian Metalworking
Categories
- Additive Manufacturing
- Aluminum Welding
- Arc Welding
- Assembly and Joining
- Automation and Robotics
- Bending and Forming
- Consumables
- Cutting and Weld Prep
- Electric Vehicles
- En Español
- Finishing
- Hydroforming
- Laser Cutting
- Laser Welding
- Machining
- Manufacturing Software
- Materials Handling
- Metals/Materials
- Oxyfuel Cutting
- Plasma Cutting
- Power Tools
- Punching and Other Holemaking
- Roll Forming
- Safety
- Sawing
- Shearing
- Shop Management
- Testing and Measuring
- Tube and Pipe Fabrication
- Tube and Pipe Production
- Waterjet Cutting
Industry Directory
Webcasts
Podcasts
FAB 40
Advertise
Subscribe
Account Login
Search
Consumables Corner: Preheat and interpass temperature defined, Part II
- By David Meyer and Rob Koltz
- November 15, 2022
- Article
- Consumables
Q: I have seen many questions and discussions about preheat and interpass temperatures lately. It appears there is confusion about how and when to measure both of these values. Can you expand on these welding terms?
A: In Part I, we defined preheat and interpass temperature, discussed appropriate measurement locations, and briefly discussed the effects of preheat and interpass temperatures. We will discuss the reasons for preheat and interpass control and discuss their effects in greater depth in this installment.
A common misconception in the welding industry is that the primary purpose of preheat is to remove any water from the surface of the steel to be welded. This is incorrect. The primary purpose of preheat is to slow the cooling rate of the weld zone after the arc has passed. Removing water from the steel’s surface is a secondary benefit.
Slowing the cooling rate of the weld zone is necessary when the steel being welded has a composition that allows for martensite—which is a hard, brittle microstructure—to form during rapid cooling. Martensite formation needs to be avoided as it is prone to cold cracking and sudden, brittle failure under loading.
A rule of thumb for plain carbon steels is carbon content of 0.30% or more requires preheat and interpass control. Preheat/interpass temperatures must be increased for steels with higher carbon content and thicker sections. For low-alloy steels, a carbon equivalent may be calculated to determine the need for preheat (see AWS D1.1 Annex B).
While proper preheat and interpass control provides benefits, excessive preheat and interpass temperatures can cause problems. High preheat/interpass temperatures—especially when welds are made with high heat input—can lead to excessive grain growth in the heat-affected zone (HAZ), which can reduce impact toughness significantly. Controlling the maximum interpass temperature prevents excessive toughness degradation in the HAZ.
Quench and tempered steels get their mechanical properties through a process of intentional rapid cooling (quenching) to create martensite, followed by heating to a specified temperature (tempering) to transform the martensite into a microstructure that is less brittle but still strong. Welding quench and tempered steels using excessively high preheat and interpass temperatures can result in undesirable softening of the HAZ. Steel manufacturers provide preheat/interpass and heat input recommendations for some quench and tempered steels. These recommendations should be followed.
About the Authors
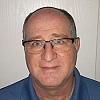
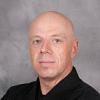
Rob Koltz
Application Engineer
411 S. Ebenezer Rd.
Florence, 29501
636-485-2253
About the Publication
Related Companies
subscribe now
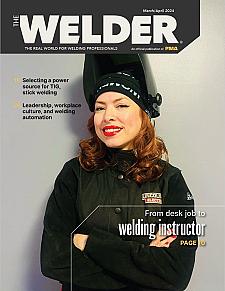
The Welder, formerly known as Practical Welding Today, is a showcase of the real people who make the products we use and work with every day. This magazine has served the welding community in North America well for more than 20 years.
start your free subscription- Stay connected from anywhere
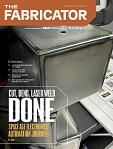
Easily access valuable industry resources now with full access to the digital edition of The Fabricator.
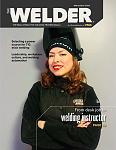
Easily access valuable industry resources now with full access to the digital edition of The Welder.
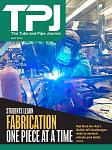
Easily access valuable industry resources now with full access to the digital edition of The Tube and Pipe Journal.
- Podcasting
- Podcast:
- The Fabricator Podcast
- Published:
- 04/16/2024
- Running Time:
- 63:29
In this episode of The Fabricator Podcast, Caleb Chamberlain, co-founder and CEO of OSH Cut, discusses his company’s...
- Trending Articles
Sheffield Forgemasters makes global leap in welding technology
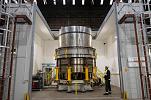
ESAB unveils Texas facility renovation
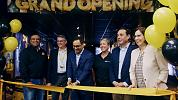
Engine-driven welding machines include integrated air compressors
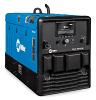
How welders can stay safe during grinding
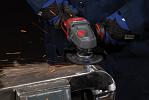
The impact of sine and square waves in aluminum AC welding, Part I
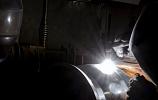
- Industry Events
16th Annual Safety Conference
- April 30 - May 1, 2024
- Elgin,
Pipe and Tube Conference
- May 21 - 22, 2024
- Omaha, NE
World-Class Roll Forming Workshop
- June 5 - 6, 2024
- Louisville, KY
Advanced Laser Application Workshop
- June 25 - 27, 2024
- Novi, MI