Technical Liaison Manager
- FMA
- The Fabricator
- FABTECH
- Canadian Metalworking
Categories
- Additive Manufacturing
- Aluminum Welding
- Arc Welding
- Assembly and Joining
- Automation and Robotics
- Bending and Forming
- Consumables
- Cutting and Weld Prep
- Electric Vehicles
- En Español
- Finishing
- Hydroforming
- Laser Cutting
- Laser Welding
- Machining
- Manufacturing Software
- Materials Handling
- Metals/Materials
- Oxyfuel Cutting
- Plasma Cutting
- Power Tools
- Punching and Other Holemaking
- Roll Forming
- Safety
- Sawing
- Shearing
- Shop Management
- Testing and Measuring
- Tube and Pipe Fabrication
- Tube and Pipe Production
- Waterjet Cutting
Industry Directory
Webcasts
Podcasts
FAB 40
Advertise
Subscribe
Account Login
Search
Consumables Corner: Welding process and fillet size limits
What metal fabricators need to consider with large welds
- By David Meyer and Rob Koltz
- Updated August 15, 2022
- August 13, 2022
- Article
- Consumables
Q: In our facility we use mostly FCAW and GMAW processes. We do a lot of T-joint welds in the flat and horizontal positions, and a common weld size is 1/4 to 5/16 in. We do have some 3/8- to 1/2-in. weld requirements as well. Some welders can perform the welds in a single pass while others do multiple passes on the larger welds. Some welders claim that is the proper way to weld sizes that are 3/8 in. or larger. Is this true and if so, what are some guidelines?
A: The answer? It depends. There are some considerations for various applications, so let's dive a little deeper into the subject.
The first thing to consider is what, if any, code you are working to. This often will dictate the largest single-pass weld you are allowed to perform in production. The maximum permitted weld size generally depends on the process, welding position, and wire diameter.
Another important consideration is the maximum qualified heat input value. To perform a large, single-pass weld, you must use a slow travel speed which will result in high heat input values. High heat input typically harms mechanical properties in both the weld metal and the base metal’s heat-affected zone (HAZ). Additionally, using slow travel speed on large, single-pass welds can lead to a lack of penetration at the root of the weld joint.
To perform fillet welds in the flat position (1F), arrange the weld joint so the welding torch can be straight up and down. If the wire diameter is 1/16 in. or larger, you can use a single pass for welds up to ½ in. in size as long as you keep the welding arc on the leading edge of the weld puddle and the heat input below the maximum listed value on the welding procedure specification. This is assuming you are working to a welding code.
Welds made in the horizontal position (2F) can be a bit tricky depending on your process, wire diameter, and skill level. Limit smaller wire diameters (less than 0.052 in.) to maximum single-pass weld sizes of ¼ in., and in a few cases 5/16 in. If the required weld size is greater than this, use multiple passes to perform the weld. This should ensure good penetration at the root of the weld and minimize weld quality issues like excessive throat, undercut, and overlap. Since the weld beads will be smaller, the travel speed should be faster with corresponding lower heat input value, which will minimize potential HAZ issues.
For wire diameters of 1/16 in. and larger, you can perform 2F welds successfully up to 3/8 in., which also is the maximum single-pass size permitted by some codes such as in AWS D1.1.
Any fillet weld greater than 3/8 in. in the 2F position, regardless of wire diameter, shall be performed in a multipass progression.
The bottom line: Making fillets larger than 3/8 in. in a single pass is done at the risk of reduced weld quality. If the application emphasizes productivity ahead of quality, then using one pass for 1/2-in. fillets may be perfectly acceptable. However, in cases where weld quality is paramount, always use multiple passes for welds larger than 3/8 in.
About the Authors
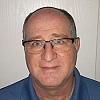
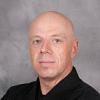
Rob Koltz
Application Engineer
411 S. Ebenezer Rd.
Florence, 29501
636-485-2253
About the Publication
Related Companies
subscribe now
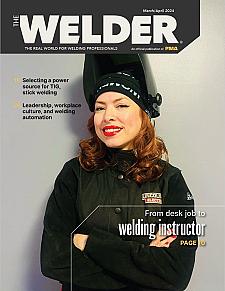
The Welder, formerly known as Practical Welding Today, is a showcase of the real people who make the products we use and work with every day. This magazine has served the welding community in North America well for more than 20 years.
start your free subscription- Stay connected from anywhere
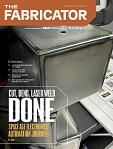
Easily access valuable industry resources now with full access to the digital edition of The Fabricator.
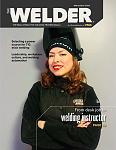
Easily access valuable industry resources now with full access to the digital edition of The Welder.
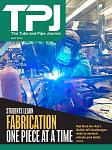
Easily access valuable industry resources now with full access to the digital edition of The Tube and Pipe Journal.
- Podcasting
- Podcast:
- The Fabricator Podcast
- Published:
- 04/16/2024
- Running Time:
- 63:29
In this episode of The Fabricator Podcast, Caleb Chamberlain, co-founder and CEO of OSH Cut, discusses his company’s...
- Trending Articles
Sheffield Forgemasters makes global leap in welding technology
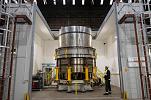
ESAB unveils Texas facility renovation
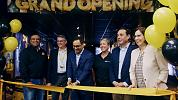
Engine-driven welding machines include integrated air compressors
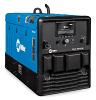
How welders can stay safe during grinding
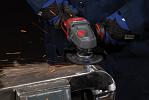
The impact of sine and square waves in aluminum AC welding, Part I
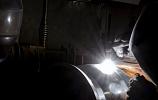
- Industry Events
16th Annual Safety Conference
- April 30 - May 1, 2024
- Elgin,
Pipe and Tube Conference
- May 21 - 22, 2024
- Omaha, NE
World-Class Roll Forming Workshop
- June 5 - 6, 2024
- Louisville, KY
Advanced Laser Application Workshop
- June 25 - 27, 2024
- Novi, MI