Technical Liaison Manager
- FMA
- The Fabricator
- FABTECH
- Canadian Metalworking
Categories
- Additive Manufacturing
- Aluminum Welding
- Arc Welding
- Assembly and Joining
- Automation and Robotics
- Bending and Forming
- Consumables
- Cutting and Weld Prep
- Electric Vehicles
- En Español
- Finishing
- Hydroforming
- Laser Cutting
- Laser Welding
- Machining
- Manufacturing Software
- Materials Handling
- Metals/Materials
- Oxyfuel Cutting
- Plasma Cutting
- Power Tools
- Punching and Other Holemaking
- Roll Forming
- Safety
- Sawing
- Shearing
- Shop Management
- Testing and Measuring
- Tube and Pipe Fabrication
- Tube and Pipe Production
- Waterjet Cutting
Industry Directory
Webcasts
Podcasts
FAB 40
Advertise
Subscribe
Account Login
Search
Consumables Corner: Why a shop using GMAW with C25 shielding gas experienced porosity
- By David Meyer and Rob Koltz
- June 22, 2022
- Article
- Consumables
Q: Our shop does a lot of welding-related repair on construction and farm equipment, as well as large steel castings and forgings primarily using flux-cored arc welding (FCAW) with CO2 shielding gas. However, these processes generate smoke and welding spatter. We tried using a gas metal arc welding (GMAW) filler metal with C25 shielding gas but experienced a lot of porosity. Any ideas as to why?
A: Based on the information you provided, we see several possible causes for the porosity you are experiencing.
Porosity occurs when nitrogen, oxygen, or hydrogen become trapped in the weld pool during solidification. Oxygen and nitrogen typically come from atmospheric contamination, while hydrogen comes from grease, oil paint, dirt, or water contamination.
Ineffective shielding gas coverage caused by flow rates that are too high or too low, hose leaks, air drafts, or holding the welding gun too far away from the weld joint can lead to porosity as well. Even a small amount of atmosphere mixed with the shielding gas in any of these scenarios can trigger it.
Porosity caused by hydrogen typically comes from welding on joints that were cleaned and prepared incorrectly. You should remove any surface contamination and then preheat to eliminate any moisture that may be present.
Since you mentioned repair work, we suspect your GMAW porosity issues stem from a surface area that is not cleaned properly. Use soap and water or acetone to remove any visible contaminants, dry the surface, and grind or use a wire wheel on the surface.
Since you did not mention any porosity issues with your current process, it is possible the FCAW wire you use has a greater cleaning capability than the GMAW wire.
Depending upon their respective classifications, GMAW and FCAW may have similar or very different levels of manganese and silicon, common deoxidizing elements.
Deoxidizers in solid GMAW wires come solely from the steel used to make the wire. With FCAW wires, the deoxidizing elements come primarily from the wire’s core.
FCAW wires may be designed with core ingredients (both slag and deoxidation ingredients) specifically tailored to provide better porosity resistance. Slag cover resulting from FCAW contributes to porosity resistance by preventing absorption of atmospheric nitrogen through the molten weld metal surface.
As an active gas, 100% CO2 improves porosity resistance with FCAW because the high arc temperature causes the gas molecules to disassociate—or separate—allowing the controlled amount of oxygen to react with other elements. This traps impurities in the slag layer that are removed after welding.
A C25 shielding gas—which is 25% CO2 and 75% argon—does not provide as much cleaning action. Argon is an inert gas that provides no cleaning action of the weld puddle, although it displaces air from the weld joint.
A 100% CO2 shielding gas does tend to produce more smoke and spatter, but it also reduces the risk of porosity. You could incorporate vigorous preweld cleaning with the GMAW process, or you could invest in localized fume extraction and stick with FCAW.
A closer look at the costs (including rework) of mitigating spatter, porosity, and fume should help you to determine what is best for your shop.
About the Authors
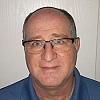
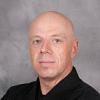
Rob Koltz
Application Engineer
411 S. Ebenezer Rd.
Florence, 29501
636-485-2253
About the Publication
Related Companies
subscribe now
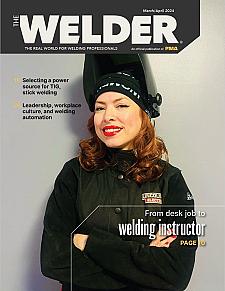
The Welder, formerly known as Practical Welding Today, is a showcase of the real people who make the products we use and work with every day. This magazine has served the welding community in North America well for more than 20 years.
start your free subscription- Stay connected from anywhere
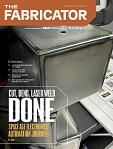
Easily access valuable industry resources now with full access to the digital edition of The Fabricator.
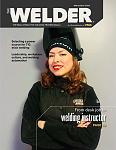
Easily access valuable industry resources now with full access to the digital edition of The Welder.
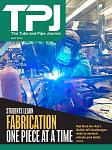
Easily access valuable industry resources now with full access to the digital edition of The Tube and Pipe Journal.
- Podcasting
- Podcast:
- The Fabricator Podcast
- Published:
- 04/16/2024
- Running Time:
- 63:29
In this episode of The Fabricator Podcast, Caleb Chamberlain, co-founder and CEO of OSH Cut, discusses his company’s...
- Trending Articles
Sheffield Forgemasters makes global leap in welding technology
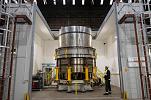
ESAB unveils Texas facility renovation
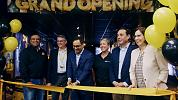
Engine-driven welding machines include integrated air compressors
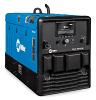
How welders can stay safe during grinding
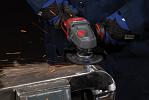
The impact of sine and square waves in aluminum AC welding, Part I
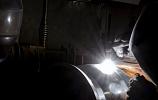
- Industry Events
16th Annual Safety Conference
- April 30 - May 1, 2024
- Elgin,
Pipe and Tube Conference
- May 21 - 22, 2024
- Omaha, NE
World-Class Roll Forming Workshop
- June 5 - 6, 2024
- Louisville, KY
Advanced Laser Application Workshop
- June 25 - 27, 2024
- Novi, MI