Contributing Writer
- FMA
- The Fabricator
- FABTECH
- Canadian Metalworking
Categories
- Additive Manufacturing
- Aluminum Welding
- Arc Welding
- Assembly and Joining
- Automation and Robotics
- Bending and Forming
- Consumables
- Cutting and Weld Prep
- Electric Vehicles
- En Español
- Finishing
- Hydroforming
- Laser Cutting
- Laser Welding
- Machining
- Manufacturing Software
- Materials Handling
- Metals/Materials
- Oxyfuel Cutting
- Plasma Cutting
- Power Tools
- Punching and Other Holemaking
- Roll Forming
- Safety
- Sawing
- Shearing
- Shop Management
- Testing and Measuring
- Tube and Pipe Fabrication
- Tube and Pipe Production
- Waterjet Cutting
Industry Directory
Webcasts
Podcasts
FAB 40
Advertise
Subscribe
Account Login
Search
Metallurgy Matters: Influencing weld strength
- By Bob Capudean
- April 24, 2015
- Article
- Metals/Materials
Weld metal strength: It’s a subject that’s often discussed, and just as often misunderstood. To fully consider how strong weld metal will be or how you can strengthen it, you have to think about not only the preweld decisions that influence weld strength, but also the postweld reactions and available mechanisms that influence it.
For example, the designer, engineer, or welder (or sometimes all three) makes conscious decisions concerning base metal and filler metal composition, welding process, weldment design, and weld joint design. All of these have a significant influence on the strength of the finished product.
On the other hand, a number of solid-state reactions that take place in the weld metal and heat-affected zone (HAZ) are important as strengthening mechanisms, and each can have a powerful influence on the decisions that were made before welding.
In other words, the decisions made concerning base metal, filler metal, weld process, and weld joint design are directly—and often significantly—influenced by mechanisms used to increase strength after welding, or by reactions that take place once the weld is complete.
Another consideration that’s often overlooked is a base metal’s weldability, something we’ll look at more closely in a later issue.
Basic Terminology
Before we continue, let’s quickly review some critical terminology:
Weld Metal. When we talk about weld metal, we’re talking about the portions of the base metal and filler metal that meld during welding. Weld metal is usually a mixture of base metal and filler metal.
Solid-state Reactions. These reactions take place in the metal when the metal is a solid. These can happen in the HAZ, in the weld metal after it has cooled, or in the base metal as it goes through temperature changes.
Heat-affected Zone. The HAZ is the portion of the base metal that didn’t melt, but had its mechanical properties or microstructure altered by the heat of welding. The HAZ is directly adjacent the weld metal and is defined by a measurable change in properties, not a specific temperature.
Weld Metal-strengthening Mechanisms
Compared to base metals, there aren’t many ways to strengthen the weld metal after welding: for example, you don’t usually cold-work the weld metal to add strength. But four solid-state reactions, or mechanisms, can strengthen the weld metal, and where applicable, these are additive, meaning the strength gained from one mechanism is added to the strength gained from another, assuming more than one can be applied to the specific weld metal.
The four mechanisms are:
- Solidification grain structure, which is common to all welds.
- Solid-solution strengthening, which applies to any alloy type.
- Transformation hardening, which applies only to specific alloy groups.
- Precipitation hardening, which applies only to specific alloy groups.
Solidification grain structure simply refers to the weld metal’s grain structure when it solidifies. Remember that weld metals freeze quickly compared to molten steel in the mill. Fast-freezing creates a segregation pattern within each individual weld metal grain.
This, in turn, results in a microstructure consisting of fine dendrite arms in a solute-rich network. Microstructures like this impede plastic flow during tensile testing, and that results in weld metals with higher yield-to-tensile-strength ratios than base metals.
Solid-solution strengthening of weld metals is functionally the same as solid-solution hardening of base metals. Base metals are hardened at the mill by adding alloys that don’t fit easily into the base metal’s crystal lattice. These alloying metals cause stress within the base metal’s crystal structure, which increases tensile strength and decreases ductility.
The same basic process works for strengthening weld metals, but in this case, the alloys are added during welding via the filler metal. Both substitutional and interstitial alloying elements will strengthen ferrous and nonferrous weld metals.
Transformation hardening is common when dealing with base metals such as mild steel. It involves the heat-quench-tempering heat treatment cycle used to adjust strength and ductility combinations for specific applications.
But transformation hardening can also take place in ferrous weld metals. This is true even if the austenite changes to something other than martensite during cooling. The weld thermal cycle’s rapid cooling reduces the transformation temperature of austenite.
The lower transformation temperature causes a ferrite-carbide to form—one that’s stronger and finer than the ferrite-carbide that’s formed at higher temperatures. Consequently, the weld metal is stronger (see Figure 1).
Precipitation-hardening alloy systems often strengthen weld metals by an aging process. And in multipass welds, certain weld metal zones along with some areas of the HAZ will be aged or even over-aged simply by the heat of welding.
Despite this, and despite the areas of over-aged weld metal, an aging heat treatment will strengthen both the HAZ and the weld metal. But the over-aged areas won’t strengthen to the same level as the base metal. Also, some aluminum precipitation-hardening weld metal will age naturally at room temperature.
We’ll get into more detail on strengthening and hardening processes in future columns, but for now this should give you an idea of what it takes to develop and maintain given levels of strength in the weld metal. Next time we’ll look at the strength and toughness, as well as the effects of welding heat, on the HAZ.
About the Author
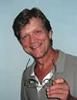
Bob Capudean
Back Alley Customs
About the Publication
subscribe now
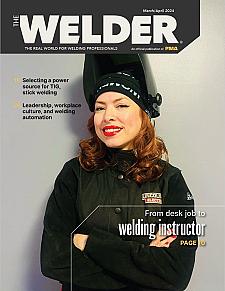
The Welder, formerly known as Practical Welding Today, is a showcase of the real people who make the products we use and work with every day. This magazine has served the welding community in North America well for more than 20 years.
start your free subscription- Stay connected from anywhere
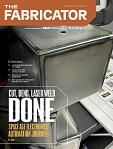
Easily access valuable industry resources now with full access to the digital edition of The Fabricator.
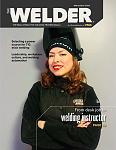
Easily access valuable industry resources now with full access to the digital edition of The Welder.
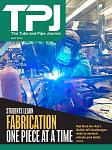
Easily access valuable industry resources now with full access to the digital edition of The Tube and Pipe Journal.
- Podcasting
- Podcast:
- The Fabricator Podcast
- Published:
- 04/16/2024
- Running Time:
- 63:29
In this episode of The Fabricator Podcast, Caleb Chamberlain, co-founder and CEO of OSH Cut, discusses his company’s...
- Trending Articles
Sheffield Forgemasters makes global leap in welding technology
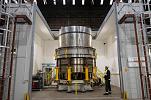
ESAB unveils Texas facility renovation
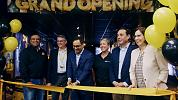
Engine-driven welding machines include integrated air compressors
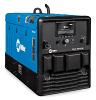
How welders can stay safe during grinding
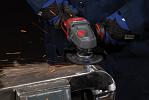
The impact of sine and square waves in aluminum AC welding, Part I
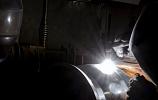
- Industry Events
16th Annual Safety Conference
- April 30 - May 1, 2024
- Elgin,
Pipe and Tube Conference
- May 21 - 22, 2024
- Omaha, NE
World-Class Roll Forming Workshop
- June 5 - 6, 2024
- Louisville, KY
Advanced Laser Application Workshop
- June 25 - 27, 2024
- Novi, MI