Business Development Manager – Metal Fabrication
- FMA
- The Fabricator
- FABTECH
- Canadian Metalworking
Categories
- Additive Manufacturing
- Aluminum Welding
- Arc Welding
- Assembly and Joining
- Automation and Robotics
- Bending and Forming
- Consumables
- Cutting and Weld Prep
- Electric Vehicles
- En Español
- Finishing
- Hydroforming
- Laser Cutting
- Laser Welding
- Machining
- Manufacturing Software
- Materials Handling
- Metals/Materials
- Oxyfuel Cutting
- Plasma Cutting
- Power Tools
- Punching and Other Holemaking
- Roll Forming
- Safety
- Sawing
- Shearing
- Shop Management
- Testing and Measuring
- Tube and Pipe Fabrication
- Tube and Pipe Production
- Waterjet Cutting
Industry Directory
Webcasts
Podcasts
FAB 40
Advertise
Subscribe
Account Login
Search
Using power tools effectively
Tips to improve shop safety when using power tools and accessories
- By David Jescovitch
- November 10, 2014
- Article
- Power Tools
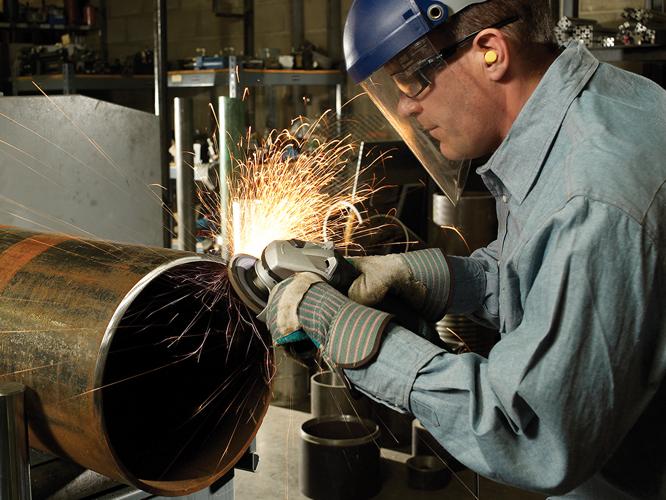
Following basic safety practices when using tools contributes to safe work conditions for the tool operator and others in close proximity. It also means cost savings for the fabrication shop through improved productivity and extended consumable life.
When it comes to using tools such as right-angle grinders, flap discs, die grinders, and cutoff wheels, you should keep in mind some basic tips to help promote safe and proper usage.
Raising awareness of basic safety practices and thinking about safety before the job starts—and after the job is complete—can help curb accidents and injuries in the shop.
Practicing these basic safety rules when using tools not only contributes to safer conditions for you, it can also contribute to cost savings for the fabrication shop through improved productivity and extended consumable life. Additionally, labor-hours are maximized when injuries are prevented.
Practice Basic Safety.
The following tips can help you improve safety regardless of your application or work environment.
Wear proper safety gear. Most manufacturers’ tool and accessory instructions include specifications about the recommended safety gear. In most situations, face and eye protection are the common first level of protection.
Keep aisles and work areas clear of clutter. This can help prevent accidental trips and falls in the shop. In addition, doing so benefits your shop’s productivity when operators don’t have to step over clutter or take the time to search for tools or accessories.
Read the manufacturer’s instructions before using the tool. It’s important that you understand the basic safety information and proper usage for each tool or accessory. It’s also a good idea to read any material safety data sheets before using the tool to familiarize yourself with specific safety considerations for the materials being used.
Inspect the tool or accessory each time it is used. While it sounds obvious, the simple act of a quick once-over inspection can help you to determine if anything is wrong with the tool or accessory, such as chips in the grinding wheel or a frayed cord on a power tool. This is an especially important step when multiple people use the same tools and accessories over the course of numerous work shifts in a fabrication shop.
Choose the Right Tools
Another key step for optimizing safety in the shop is choosing the right tool or accessory for the application and the material. For example, don’t use an electric drill for a job that might require a grinder. Anytime you force the tool to operate in a way that it’s not designed to be used, you automatically increase the risk for injury either to yourself or to those around you.
Even when you do choose the appropriate accessory or tool and use it as it’s intended, take it a step further by checking that all the necessary tool guards are attached and secured properly before an accessory is mounted on the tool.
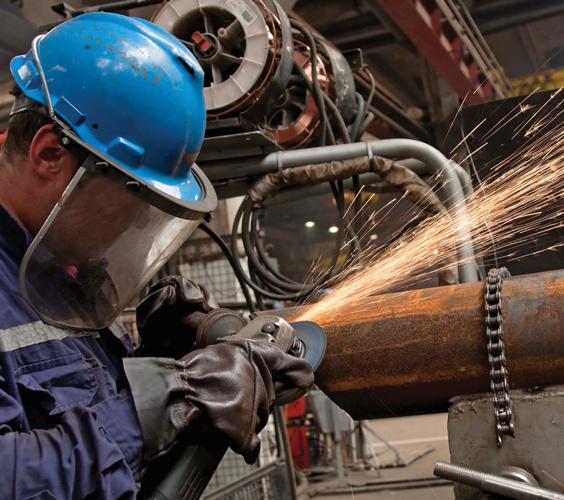
The SPOT method highlights four factors that can limit the potential for injury when using wire brushes and abrasives. SPOT stands for speed and size, pressure, orientation, and time.
Disconnect the tool from its power source before attaching or removing an accessory. Doing so eliminates the danger of the tool powering on accidentally while the accessory is being attached or removed.
Also, be sure to secure and properly clamp the workpiece to reduce the risk of injury from potential slipping or the piece moving. Never use a tool that has been modified, as modifications may change how the tool can be safely operated.
Employ the SPOT Method
One way to ensure that you are properly and safely using tools, accessories, and consumables is to employ the SPOT method, which highlights four factors you control that can limit the potential for injury when using wire brushes and abrasives. SPOT stands for speed and size, pressure, orientation, and time.
Speed and size. It’s important to match the speed and size of the accessory to the speed and size of the tool. The RPM rating of the accessory should meet or exceed the maximum RPM rating of the tool for safest use. Just because an accessory fits on a specific tool does not mean it can be used safely with that tool.
Pressure. Using the appropriate pressure for the tool helps contribute to safe usage. Pushing hard to get the job done adds to the potential for injury, and it also can lead to greater operator fatigue.
Orientation. Any tool or accessory needs to be used at the proper angle to the workpiece for maximum safety. A wire brush, for example, is designed so that the wire tips do the work in striking the base material. Take care, then, to use it at the appropriate angle to ensure the wire tips are working as intended.
Time. Using an accessory for too long can be unsafe. When it shows signs of physical damage or wear, you should replace it as soon as possible. Never use a tool or accessory that has visible signs of fatigue, such as a crack in a grinding wheel or long wire breakage on a brush. Inspect the tool or accessory before each use to determine its condition; this not only affects your own safety, but the tool or accessory’s productivity.
Be Aware of Your Surroundings
Improving safety in the shop happens in part by increasing awareness of your surroundings and what others around you are doing. Continue to pay attention to your safety even after the work is completed. Eye injuries commonly occur after the work is done and eye protection is removed. Keep your protective eyewear on when you brush debris or grit out of your hair or remove your cap or do-rag. Debris from your hair or cap can still enter the eye, causing injury.
The bottom line: You are your own last line of defense. Whether it’s using the proper safety gear or verifying that the speed of the tool and accessory match—no matter what box the item came from—you play a role in making sure safe practices are always being followed, which can contribute to greater productivity, cost savings, and efficiency.
About the Author
David Jescovitch
One Weiler Drive
Cresco, 18326
570-595-7495
About the Publication
Related Companies
subscribe now
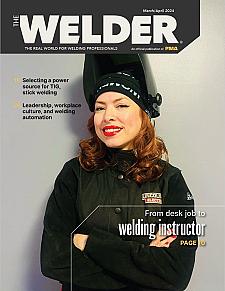
The Welder, formerly known as Practical Welding Today, is a showcase of the real people who make the products we use and work with every day. This magazine has served the welding community in North America well for more than 20 years.
start your free subscription- Stay connected from anywhere
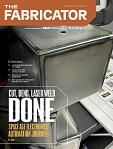
Easily access valuable industry resources now with full access to the digital edition of The Fabricator.
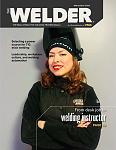
Easily access valuable industry resources now with full access to the digital edition of The Welder.
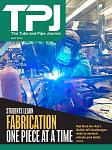
Easily access valuable industry resources now with full access to the digital edition of The Tube and Pipe Journal.
- Podcasting
- Podcast:
- The Fabricator Podcast
- Published:
- 04/16/2024
- Running Time:
- 63:29
In this episode of The Fabricator Podcast, Caleb Chamberlain, co-founder and CEO of OSH Cut, discusses his company’s...
- Trending Articles
Sheffield Forgemasters makes global leap in welding technology
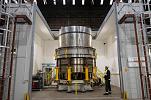
ESAB unveils Texas facility renovation
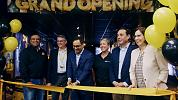
Engine-driven welding machines include integrated air compressors
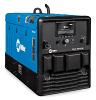
How welders can stay safe during grinding
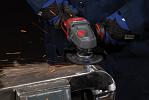
The impact of sine and square waves in aluminum AC welding, Part I
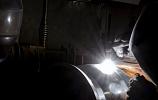
- Industry Events
16th Annual Safety Conference
- April 30 - May 1, 2024
- Elgin,
Pipe and Tube Conference
- May 21 - 22, 2024
- Omaha, NE
World-Class Roll Forming Workshop
- June 5 - 6, 2024
- Louisville, KY
Advanced Laser Application Workshop
- June 25 - 27, 2024
- Novi, MI