Editor
- FMA
- The Fabricator
- FABTECH
- Canadian Metalworking
Categories
- Additive Manufacturing
- Aluminum Welding
- Arc Welding
- Assembly and Joining
- Automation and Robotics
- Bending and Forming
- Consumables
- Cutting and Weld Prep
- Electric Vehicles
- En Español
- Finishing
- Hydroforming
- Laser Cutting
- Laser Welding
- Machining
- Manufacturing Software
- Materials Handling
- Metals/Materials
- Oxyfuel Cutting
- Plasma Cutting
- Power Tools
- Punching and Other Holemaking
- Roll Forming
- Safety
- Sawing
- Shearing
- Shop Management
- Testing and Measuring
- Tube and Pipe Fabrication
- Tube and Pipe Production
- Waterjet Cutting
Industry Directory
Webcasts
Podcasts
FAB 40
Advertise
Subscribe
Account Login
Search
Advice on small business ownership and becoming a certified welding inspector
From welder to business owner to CWI, Jeremy Condrey is a one-man band with Southern Weld Co.
- By Rafael Guerrero
- August 12, 2023
- Article
- Shop Management
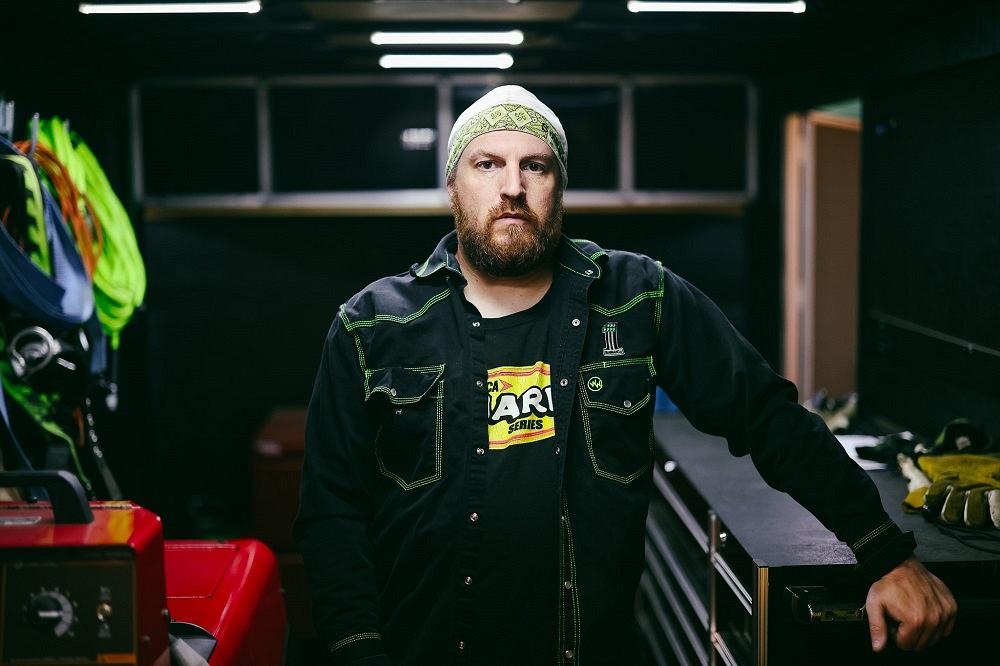
Jeremy Condrey is the owner and founder of S.C.-based Southern Weld Co., whose services include welding, inspections, consulting, and training. Images: Wayne Waweru
Count Jeremy Condrey as a fan of Johnny Cash.
In fact, he compares his trajectory and the growth of his small business, Southern Weld Co., to Cash’s “One Piece at a Time.”
“That’s the only way I’ve been able to do it. This whole business has been done one piece at a time, one step at a time,” said Condrey, who has certified welding inspector (CWI) and certified welding educator (CWE) certifications from the American Welding Society. “My whole career has been that way, learning different welding processes and learning this and learning that.”
Condrey launched Southern Weld Co. in 2020, at a time “when everybody else was shutting down” because of the COVID-19 pandemic.
“You couldn’t get in front of somebody to shake their hand … they're all standing behind the glass, looking at me like, ‘You’re not coming in here, we don’t even know who you are,’” he said.
Nonetheless, Condrey navigated the pandemic and continued on. For now, Condrey is a one-man band at his Wellford, S.C.-based business, offering services that include welding, inspections, consulting, and training (he said he’d like to hire someday).
“Welding itself is probably the least of what I do now,” he said. “When I started, I had to take in anything and everything. But I’m slowly starting to get into more consulting and procedure writing and inspections and things like that, which is the direction I wanted to go in anyway.”
Condrey discusses his small business, pursuing his CWI, job site experiences, and more.
The WELDER: What drove you to start Southern Weld?
Jeremy Condrey: Being out on the road and the uncertainty. You're always looking for the next job, you’re always looking for the next thing and it was always a hunt, and I got tired of hunting. With my daughter, I missed out on a lot. There were things in her life I didn’t get to be a part of—birthdays, school events. I'm not going to get any of that back, but I did what I had to do to provide a living.
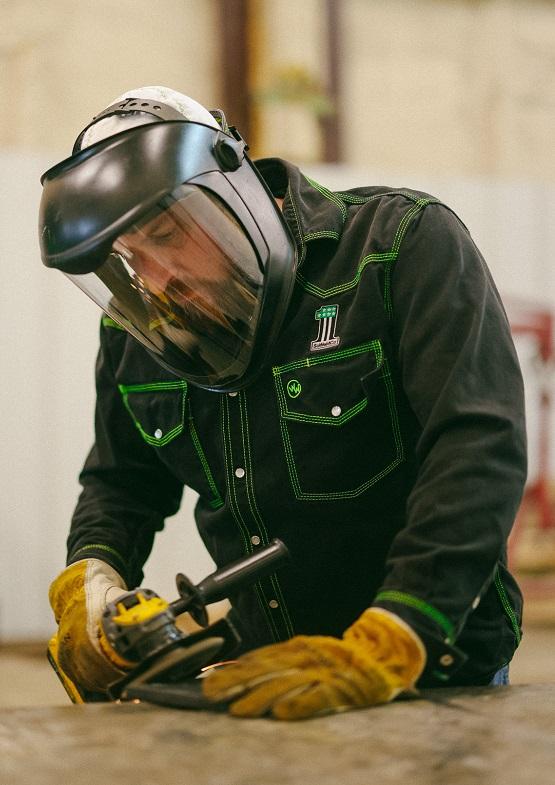
Condrey believes his role as a certified welding inspector is to be a resource for others, someone who can help—and if he does not have the answers, to find someone who does.
I enjoyed traveling and seeing different parts of the country. But I also wanted my own thing. I always wanted to see if I could take something from nothing and make it something.
TW: Can you describe those early days of your business?
Condrey: I started out as a mobile welding business. I bought an enclosed trailer and I had it wrapped.
If I didn’t have anything to do or had any kind of business, I would fill up the tank and I would go out and get on interstates 85 or 26; I-85 runs between Atlanta and Charlotte, and I-26 runs from Asheville, N.C., all the way down to Charleston. And I would go out and ride and go through industrial parks and industrial areas. I’d listen through satellite radio to local stations and listen for traffic reports. Every day, there would be some kind of traffic jam, especially on I-85. If I heard there was a traffic jam, I’d go out and try to get in it ... so people would notice me.
TW: What is in the mobile trailer and what are your capabilities?
Condrey: I started with a Lincoln [Electric] gas welding machine. I added pieces here and there, like a high-frequency box so I can TIG weld aluminum in the field. I’ve a MIG box in there, a plasma cutter, my torches, my gang box from when I traveled around. I was sort of like Johnny Cash: one piece at a time.
I had a lot of people ask me about it because nobody really sees an enclosed trailer in a welding business.
TW: What certifications do you hold?
Condrey: I’m a CWI and a CWE. I currently have welding qualifications for ASME Section IX. I took a couple of pipe tests and procedure tests and sent them off to a lab several states away and had everything analyzed. So I do have actual paperwork on me signed by a third party. I do have some [certifications] but I don’t have everything that I need, but I’ve got a good base.
These tests cost a lot of money. Just to get Section IX, with the coupons and everything, it was a little over $1,000. For a huge corporation, that would be nothing. But right now, I’m it. With $1,000, I can do a lot of stuff.
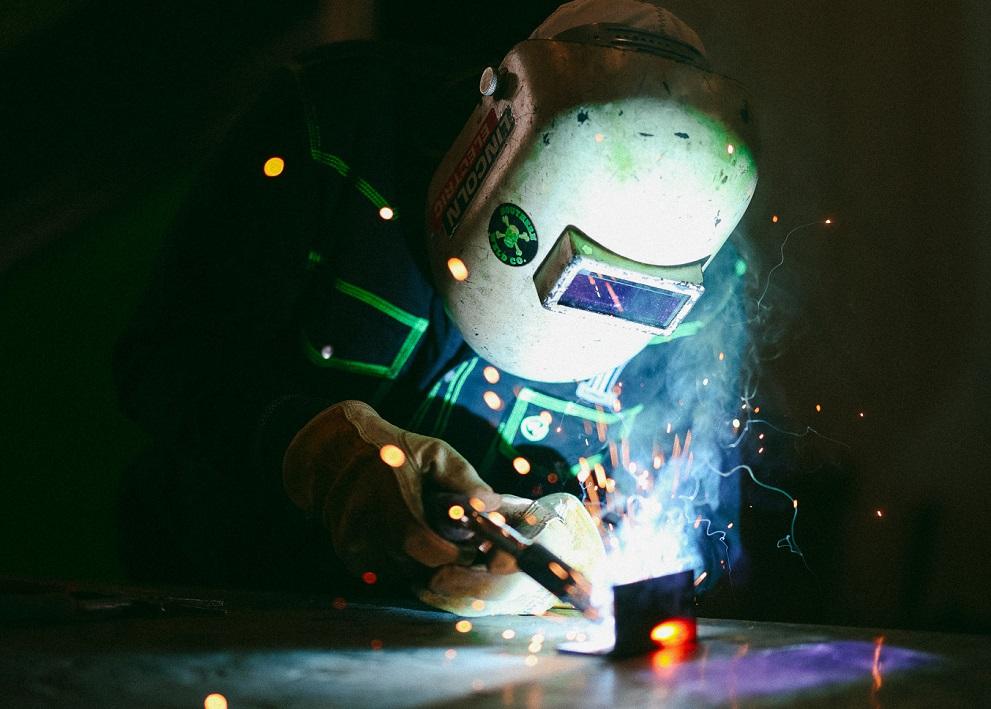
Condrey launched Southern Weld Co. in 2020, just as the COVID-19 pandemic forced others to shut down, making introductions to others more difficult.
TW: Do any projects you’ve welded on over the years stand out to you?
Condrey: There’s a local company that has me do work for them and they do work on exotic cars. I’ve done welding repairs on a Ford GT40 and the last thing I did for them was build fuel lines for a 1954 Mercedes 300SL Gullwing.
Usually, when somebody calls me and they say they have a car, I always tell them I don’t work on cars. But for some reason that day, I asked what car.
I’ve worked on some nuclear power plants, and I’ve been on some pretty diverse projects. Chemical plants, power plants, fab shops, and things like that, but I’ve kind of been everywhere. That was what I thought helped me when I went to get my CWI and understanding all these different processes. I was fortunate enough to do a lot of different stuff.
TW: Why did you pursue CWI certification?
Condrey: I wanted to make myself a better welder. I figured if I got my CWI certification, I would have a better understanding of how I was getting by. What I mean by that is when you produce a weld, a lot of these guys don’t understand codes, reading drawings, and meeting standards. They just know that their foreman told them to weld this. And whether it was good or bad, they never really understand why. So I wanted a deeper understanding of what I'm actually doing.
When I got my CWI, I really thought things were going to get easier, but it wasn’t. The challenge was to get somebody to even give me a job as a CWI.
Fortunately, somebody gave me a shot and here I am, six years later. My first job was at a power plant that was being built from the ground up. I made a lot of mistakes; luckily, I was able to learn from it. That was really good training for me. I looked at thousands of welds on that job and it really opened my eyes to what is out there with a CWI.
TW: Could you provide some real-world examples of inspecting welders?
Condrey: There were things that I saw about cup and tungsten sizes that really stood out to me. Everybody loves to TIG weld: It’s clean; you get that pretty Instagram shot; you can get a good, high-quality weld out of it. But I would notice guys would put the root in with the same cup that they put the cap on with, and they would run the same tungsten and the same heat all the way out. They would never change it.
And this really happened: I had a guy blow four TIG rigs before lunch one day. They called out to somebody from quality control, and I happened to be nearby. He was welding 2-in. socket welds at 230 amps. He had somehow bypassed his regulator to where it was just pouring argon. Our procedure called for 20 to 50 CFM and he’s out there cranking it up straight, going way hotter than what the procedure called for. I'm standing there and it sounded like a jet taking off of an aircraft carrier.
“You know why this is happening? You’ve maxed out everything you're doing, and you’re not getting a better weld out of this because you’re not actually penetrating all the way down there. You’re just laying your wire down there and just trying to smoke it all in. I guarantee if I cut this thing up, you’re going to have a family of four living in these voids.”
TW: How do you see yourself as a CWI when you’re out in the field?
Condrey: I’m there as a resource. I've had guys say, “Oh, here comes the fault-finder.” I can't speak for every CWI; I've had some that were amazing and some that were basically just welding cops and were looking for an excuse to fail you. I’ve run into both kinds, and the ones I remember the most are the ones that were there to help.
As an inspector, for me, I want to come out there, and if you’re having trouble, I want to help you. If I can't help you, I’ll find somebody that will. But I'm not going to come out here and try to blame you for something or get you in trouble. I'm not out there to find fault or to write you up or shoot your weld down because I don’t like you.
TW: Does the fact that you can weld give you more credibility when interacting with welders on job sites?
Condrey: My first job [in quality control], it was me and this other guy that got hired. About a week later, I was walking around, hanging out in one area. I had this fitter come up to me and say, “You know, these guys here don’t respect you.” I asked why that is. “Well, you’re just a dumb college boy … you all don’t know nothing about what we do out here. You've only seen what we’ve done in a book.”
I said, “I’ve never been to college. I went to tech school near where I live and learned how to weld. I just took my CWI a couple of months ago and passed it.”
He said, “You can weld?” I said, “Yeah, absolutely.” He didn’t believe me. There were some scraps laying there. I said, “Let me borrow a hood,” and I did a little weld right there.
I started talking to him, and he understood that I could do something and I could talk to him like a person. Nobody even knew what my name was—even though it was on my hard hat—and these guys have already told my story and never asked me about it.
Once I told them that, word got buzzing around the job site and I became one of the inspectors that you wanted to deal with because they knew I wasn’t going to walk up and just shoot you down and make you feel like an idiot. It took a while for me to gain that respectability.
TW: What would you say to someone considering the CWI certification?
Condrey: Well, if you want your CWI, it will take an investment in yourself. Nobody, no company, will come up and say they want to invest in you. You have got to have the willpower and desire because if you do not, you will not pass that exam. Anybody who has ever sat for that exam will tell you that is one of the worst things they’ve ever experienced. The actual test itself is not pleasant. The AWS has done a very great job making it extremely difficult.
About the Author
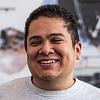
Rafael Guerrero
2135 Point Blvd.
Elgin, IL 60123
(815)-227-8242
Rafael Guerrero. was named editor of The Welder in April 2022. He spent nine years as a journalist in newspapers in the Midwest and Pacific Northwest, covering topics and communities in central Illinois, Washington, and the Chicago area.
About the Publication
subscribe now
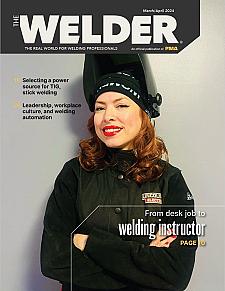
The Welder, formerly known as Practical Welding Today, is a showcase of the real people who make the products we use and work with every day. This magazine has served the welding community in North America well for more than 20 years.
start your free subscription- Stay connected from anywhere
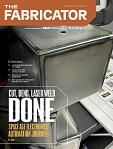
Easily access valuable industry resources now with full access to the digital edition of The Fabricator.
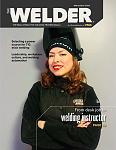
Easily access valuable industry resources now with full access to the digital edition of The Welder.
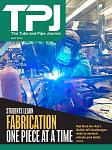
Easily access valuable industry resources now with full access to the digital edition of The Tube and Pipe Journal.
- Podcasting
- Podcast:
- The Fabricator Podcast
- Published:
- 04/16/2024
- Running Time:
- 63:29
In this episode of The Fabricator Podcast, Caleb Chamberlain, co-founder and CEO of OSH Cut, discusses his company’s...
- Trending Articles
Sheffield Forgemasters makes global leap in welding technology
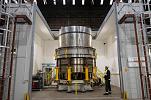
ESAB unveils Texas facility renovation
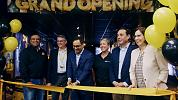
Engine-driven welding machines include integrated air compressors
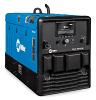
How welders can stay safe during grinding
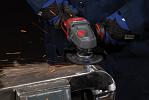
The impact of sine and square waves in aluminum AC welding, Part I
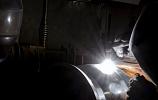
- Industry Events
16th Annual Safety Conference
- April 30 - May 1, 2024
- Elgin,
Pipe and Tube Conference
- May 21 - 22, 2024
- Omaha, NE
World-Class Roll Forming Workshop
- June 5 - 6, 2024
- Louisville, KY
Advanced Laser Application Workshop
- June 25 - 27, 2024
- Novi, MI