Metal Processing Market Manager
- FMA
- The Fabricator
- FABTECH
- Canadian Metalworking
Categories
- Additive Manufacturing
- Aluminum Welding
- Arc Welding
- Assembly and Joining
- Automation and Robotics
- Bending and Forming
- Consumables
- Cutting and Weld Prep
- Electric Vehicles
- En Español
- Finishing
- Hydroforming
- Laser Cutting
- Laser Welding
- Machining
- Manufacturing Software
- Materials Handling
- Metals/Materials
- Oxyfuel Cutting
- Plasma Cutting
- Power Tools
- Punching and Other Holemaking
- Roll Forming
- Safety
- Sawing
- Shearing
- Shop Management
- Testing and Measuring
- Tube and Pipe Fabrication
- Tube and Pipe Production
- Waterjet Cutting
Industry Directory
Webcasts
Podcasts
FAB 40
Advertise
Subscribe
Account Login
Search
The facts about hex chrome fume
What welders need to know about the health hazards associated with exposure
- By Jon Ladwig
- September 16, 2020
- Article
- Shop Management
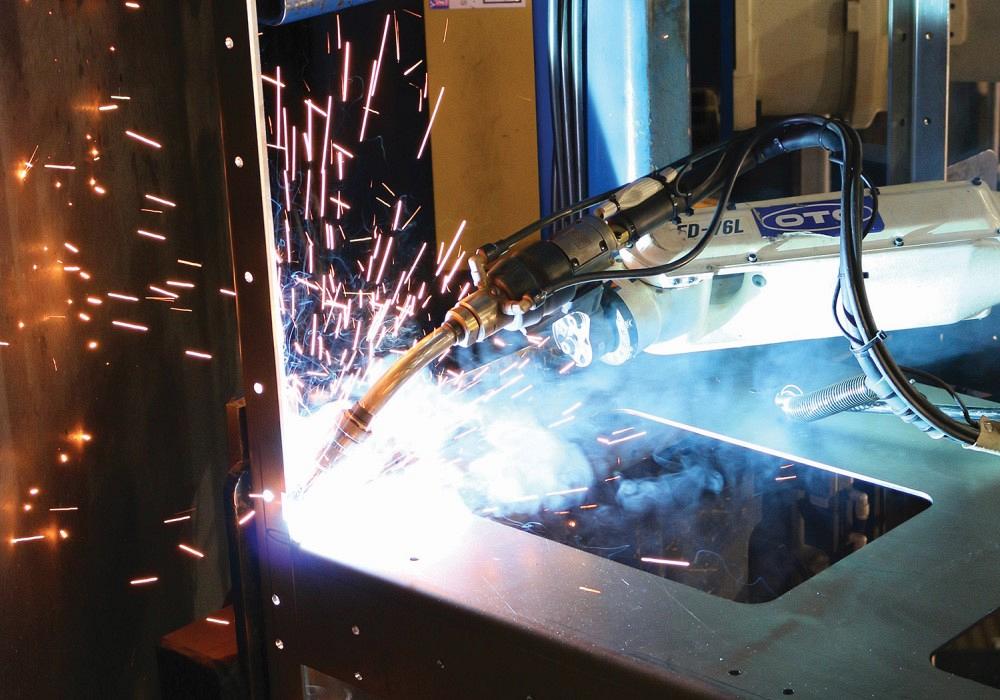
Hex chrome is produced during welding and other types of hot work on stainless steel and other metals that contain chromium. Images provided
Hexavalent chromium (hex chrome) is a carcinogenic substance produced in a variety of welding and metalworking processes. It is imperative for facilities to take proper steps to protect employees from dangerous hex chrome fume.
To do so, employers must be well-versed in the health problems associated with exposure to fumes, the methods and processes that produce hex chrome, and acceptable engineering controls for safety and regulatory compliance.
Workplace Exposure to Hex Chrome
According to a study by the National Institute for Occupational Safety and Health (NIOSH), an estimated 558,000 U.S. workers were exposed to airborne hexavalent chromium compounds in the workplace in one year. Exposure generally occurs during hot work such as welding on stainless steel and other alloy steels that contain chromium. The largest number of workers identified as potentially exposed to hex chrome in the NIOSH study were those working in carbon steel welding, stainless steel welding, painting, electroplating, steel mills, and iron and steel foundries.
A number of industrial processes used to manufacture stainless steel parts carry a risk of hex chrome exposure including welding, thermal spray (plasma, electric arc, and combustion), plasma and laser cutting, dip tanks, anodizing and plating lines, spray painting, and smelting of ferrochromium ore.
Exposure to hex chrome can occur by inhalation, absorption through the skin, or even ingestion by mouth if employees don’t wash their hands sufficiently.
Hex Chrome Health Risks
NIOSH considers all hex chrome compounds to be occupational carcinogens. Lung cancer is the greatest health danger associated with exposure, but other major health problems include nasal septum ulcerations and perforations, skin ulcerations, and allergic and irritant contact dermatitis.
Once in the body, hex chrome typically targets the organs, especially the respiratory tract. Breathing in high levels of it can cause nose and throat irritation. Symptoms may include runny nose, sneezing, coughing, itching, and a burning sensation. Repeated or prolonged exposure can cause sores to develop in the nose, resulting in nosebleeds.
Other problems can include damage to mucous membranes, perforation of septum tissue between the nostrils of the nose, and damage to the lungs. Some people develop allergies to hex chrome so that inhaling chromate compounds can cause asthma symptoms such as wheezing and shortness of breath.
People also can develop an allergic reaction on their skin called allergic contact dermatitis. This occurs from handling liquids or solids containing hexavalent chromium. Once an employee develops that allergy, brief skin contact with the toxin causes swelling and a red, itchy rash that becomes crusty and thickens with prolonged exposure. Allergic contact dermatitis is long-lasting and more severe with repeated skin contact. Contact with cuts and open sores can also lead to chrome ulcers, which heal slowly and leave scars.
OSHA Standard
The Occupational Safety and Health Administration (OSHA) sets the standard for allowable hex chrome levels in the workplace and enforces compliance, but it does not prescribe solutions for mitigation. OSHA’s May 2006 rule drastically reduced the permissible level of exposure to hex chrome in the workplace from 52 to 5 micrograms per cubic meter (μg/m3), a tenfold reduction. More specifically, the current permissible exposure limit (PEL) is 5 μg/m3 time-weighted average (TWA) in an 8-hour shift.
OSHA’s hexavalent chromium standard (3373-10) published in 2009 notes three main categories of engineering controls:
- Substitution. Using a different, less toxic material to reduce exposure.
- Isolation. Enclosing or encapsulating the source of exposure completely.
- Ventilation. Using exhaust and dust collection/filtration equipment to capture airborne hex chrome fume particles near the source of generation.
Even with these engineering controls, employers are responsible for understanding the hazards and engineering the best available control technology (BACT) for their operations. OSHA’s job is to enforce the hex chrome standard and monitor compliance in industrial workplaces.
Air Monitoring to Determine Compliance
OSHA stipulates that every company that generates hex chrome during an industrial process must monitor the air to determine the 8-hour TWA exposure for each affected worker. OSHA offers two options for determining exposure, which are spelled out in detail in the standard:
- Scheduled monitoring option
- Performance-oriented option
If you use the scheduled monitoring option, you must perform exposure monitoring initially and periodically. For exposures that are determined to be at or above OSHA’s PEL of 5 μg/m3 in an 8-hour TWA, exposure monitoring must be performed at least every three months.
For exposures that are at or above OSHA’s Action Level of 2.5 μg/m3 (8-hour TWA), exposure monitoring must be performed every six months. Additionally, exposure monitoring must be performed whenever there is a change in work processes or materials that may result in new or additional exposures to hex chrome.
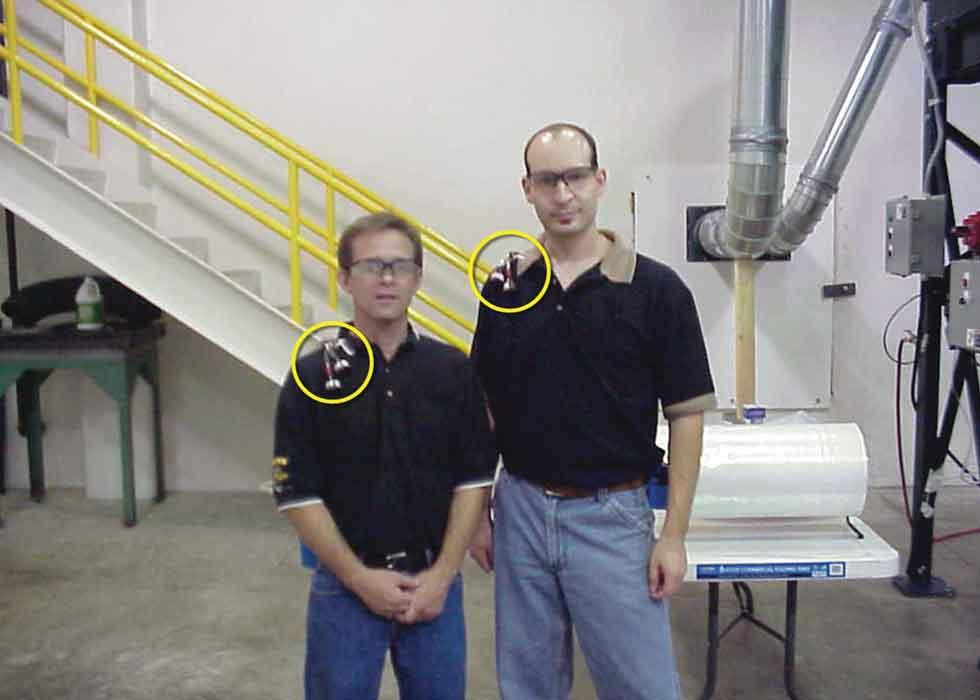
To monitor air quality, workers wear a small air pump and filter that draws a measured volume of air at a steady flow rate to simulate respiration. The material collected in the filter provides an accurate snapshot of exposure levels.
Scheduled monitoring is accomplished through personal air sampling. Workers wear a small air pump and filter that draws a measured volume of air at a steady flow rate to simulate respiration. The material collected in the filter provides an accurate snapshot of exposure to hex chrome.
Exposure is defined as the concentration of contaminant to which an employee would be exposed without using personal protective equipment, like a respirator.
Alternatively, OSHA allows the performance-oriented option whereby exposures can be estimated using any combination of air sampling, historical monitoring data, or objective data. Objective data equates to air monitoring data from industrywide surveys or calculations based on the composition or chemical and physical properties of a substance demonstrating the employee exposure to hex chrome associated with a particular product or material or a specific process, operation, or activity. The data must reflect workplace conditions closely resembling the processes, types of material, control methods, work practices, and environmental conditions in the employer’s current operations.
Whichever approach is the best for your situation, the standard requires you to keep an accurate record of all air monitoring performed.
Capturing and Controlling Hex Chrome Fumes
A high-efficiency cartridge-style dust collector is the type of filtration system that best captures hex chrome. Older-style baghouse collectors and electrostatic precipitators do not typically offer high enough filtration efficiencies to remove this toxic contaminant to the required level.
vHere are four examples of systems that generally are used to clean up welding and other processes that generate metallic dust and fumes.Tip extraction systems. These systems capture welding fumes at the tip of the welding gun, thus removing a good percentage of fumes.
Source-capture systems. This is a popular choice for applications involving small parts and fixture welding. These systems typically use fume exhaust welding guns, fume arms, backdraft slotted hoods, or small hoods with side curtains. This approach is usually limited to work envelopes of 5 cu. ft. or less.Enclosures and hoods. These also capture dust and fumes at their source and are typically used for medium-sized areas that are 12 by 20 ft. or less. Enclosures around robotic welding processes that have proper airflow will capture toxic fumes and remove them from the space. Hoods should be positioned as close as possible to the source of the hex chrome to prevent toxic fumes from escaping, and they should be ducted to the cartridge collector.
Ambient or general air-cleaning systems. These systems are often chosen to serve larger areas that have restrictions due to large weldments, overhead cranes, and big material handling clearances. They can enable a facility to capture fumes from multiple operations. Though popular for general welding applications, ambient systems alone generally are not the preferred choice for hex chrome.
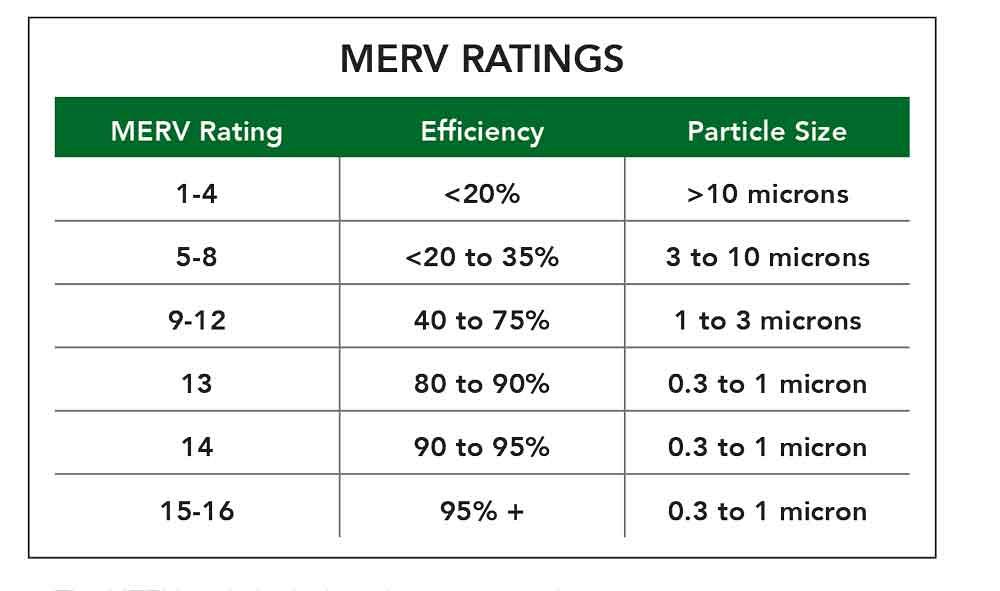
The MERV scale is designed to represent the worst-case performance of a filter for dealing with particles in the range of 0.3 to 10 microns. The higher the MERV rating, the greater the percentage of particles captured on each pass. This chart shows the removal efficiencies of filters with various MERV designations.
Ambient systems blow clean air into the workspace, reducing fume concentrations and moving fumes out of the space to be drawn into a cartridge filter system. They reduce the overall concentration of hazardous dust in the space, but they do not remove fumes from the breathing zone. Therefore, personal respiratory protection still may be required. In addition, workers can use fans to direct fumes away from the breathing zone. A well-designed ambient system includes adjustable diffusers, allowing clean air to be directed toward the workstation, reducing fume concentration and providing worker comfort as well.
Filter Efficiency Ratings
It’s important to understand filter efficiency measures and how they differ when you are selecting filters to capture hex chrome effectively.
Minimum efficiency reporting value (MERV) is a measurement scale designed in 1987 by the American Society of Heating, Refrigerating and Air-Conditioning Engineers (ASHRAE) to compare the effectiveness of air filters.
The MERV scale, which goes from 1 to 16, represents the worst-case performance of a filter for dealing with particles in the range of 0.3 to 10 microns. The higher the MERV rating, the greater the percentage of particles captured on each pass. The accompanying chart shows the removal efficiencies of filters with various MERV designations.
Though the MERV scale is a useful tool, do not rely on it alone when selecting dust collector filters. MERV ratings apply only to new filters, and the efficiency of dust collector filters changes a lot during actual use.
Mass density efficiency, defined as the weight per unit volume of air, is a more relevant predictor of OSHA compliance. For example, using this measurement, a filter manufacturer might guarantee that emissions will not exceed 5 mg/m3 at the discharge of the dust collector using high-efficiency nanofiber media.
Particle count efficiency is another measure based on particle count and is useful in evaluating filters in the higher filtration efficiency ranges. For example, a HEPA filter rated at 99.97% efficiency at 0.3 microns will capture 9,997 of 10,000 same-sized particles in the airstream.
HEPA Filtration for Hex Chrome Control
No matter the type of cartridge dust collection system, it must be equipped with a HEPA safety-monitoring filter, sometimes called a final filter, secondary filter, or afterfilter.
A filter rated at MERV 15-16 will extract airborne particulates down to 5 mg/m3. This level of filtration efficiency will satisfy the great majority of general indoor air quality requirements. However, the PEL for hex chrome under the OSHA standard is 5 μg/m3 (not milligrams)—1,000 times stricter than a MERV 16 air filter can reliably produce.
As a result, for processes involving hazardous metals, it is recommended that you use the following filter types:
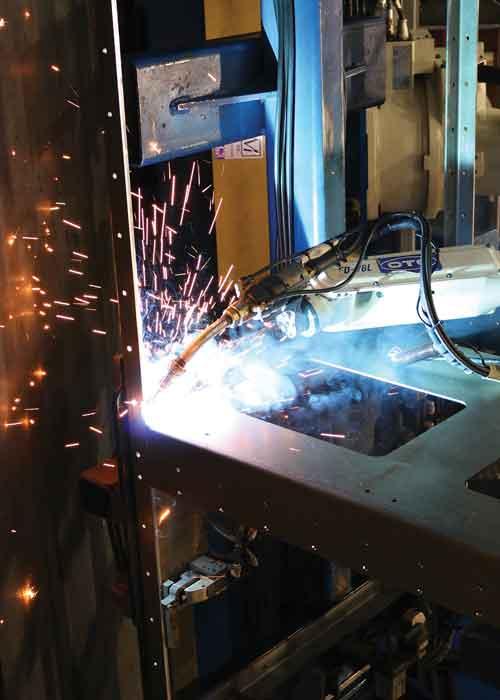
Hex chrome is produced during welding and other types of hot work on stainless steel and other metals that contain chromium.
- A high-efficiency nanofiber media dust collector filter that delivers tested efficiency of MERV 15 per the ASHRAE standard 52.2. This represents the best available control technology to provide the first line of filtration.
- A HEPA-rated secondary or safety monitoring filter tested to provide 99.97% particle removal efficiency at 0.3 microns. The HEPA filter is needed to protect employees at a level required to meet the hex chrome standard. It will also prevent collected dust from re-entering the workspace if there’s a leak in the dust collector’s primary filtering system.
As noted above, filter efficiency ratings are useful for comparing like products, but they do not guarantee OSHA compliance. Ask your filtration vendor to provide a written guarantee that the system will keep emissions at or below 5 μg/m3 at the fan discharge—that is, downstream of the secondary HEPA filter. Your vendor should also be willing to guarantee the emissions performance of the primary dust collector filters. Be wary of vendors who will not provide a written guarantee or who tell you it is unnecessary to use a HEPA filter for hex chrome applications.
Remember, a filter performance guarantee is not a substitute for the air quality monitoring procedures required under the OSHA hex chrome standard. However, it can help to ensure that you will achieve the required results.
Helpful Hex Chrome Reference Material
- American Society of Heating, Refrigerating and Air-Conditioning Engineers (ASHRAE) Standard 52.2: Method of Testing General Ventilation Air-Cleaning Devices for Removal Efficiency by Particle Size
- National Institute for Occupational Safety and Health (NIOSH) Criteria for a Recommended Standard: Occupational Exposure to Hexavalent Chromium
- OSHA Fact Sheet: Controlling Hazardous Fume and Gases during Welding
- OSHA Fact Sheet: Health Effects of Hexavalent Chromium
- OSHA Occupational Chemical Database, Chromium VI Compounds (Hexavalent Chromium)
- OSHA Standard on Hexavalent Chromium
About the Author
Jon Ladwig
3505 S. Airport Road,
Jonesboro, AR 72401
870-933-8048
About the Publication
subscribe now
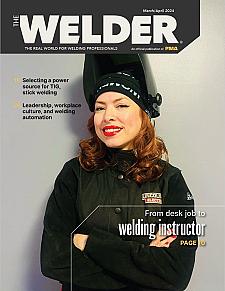
The Welder, formerly known as Practical Welding Today, is a showcase of the real people who make the products we use and work with every day. This magazine has served the welding community in North America well for more than 20 years.
start your free subscription- Stay connected from anywhere
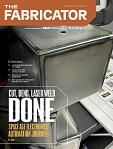
Easily access valuable industry resources now with full access to the digital edition of The Fabricator.
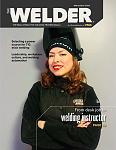
Easily access valuable industry resources now with full access to the digital edition of The Welder.
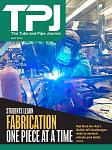
Easily access valuable industry resources now with full access to the digital edition of The Tube and Pipe Journal.
- Podcasting
- Podcast:
- The Fabricator Podcast
- Published:
- 04/16/2024
- Running Time:
- 63:29
In this episode of The Fabricator Podcast, Caleb Chamberlain, co-founder and CEO of OSH Cut, discusses his company’s...
- Trending Articles
Sheffield Forgemasters makes global leap in welding technology
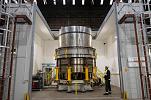
ESAB unveils Texas facility renovation
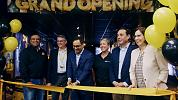
Engine-driven welding machines include integrated air compressors
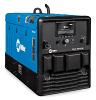
How welders can stay safe during grinding
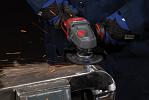
The impact of sine and square waves in aluminum AC welding, Part I
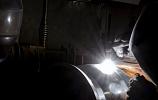
- Industry Events
16th Annual Safety Conference
- April 30 - May 1, 2024
- Elgin,
Pipe and Tube Conference
- May 21 - 22, 2024
- Omaha, NE
World-Class Roll Forming Workshop
- June 5 - 6, 2024
- Louisville, KY
Advanced Laser Application Workshop
- June 25 - 27, 2024
- Novi, MI